Оптимизация складских операций. Практические рекомендации Клуба логистов. Оптимизация складских процессов
Оптимизация технологического процесса на складе (ч. 2) – Склад и техника
В. Дёмин, руководитель проекта «Складская логистика» Координационного совета по логистике
Размещение товаров на хранение
Его необходимо выполнять таким образом, чтобы при последующих технологических операциях число перемещений складских служащих было минимальным. С этой целью делят все товарные позиции на три группы, после чего для их хранения выделяют «горячие» и «холодные» складские зоны. Чтобы оптимально разделить всю номенклатуру, необходимо воспользоваться методиками АВС- и XYZ-анализа. В данном случае, т. е. применительно к технологическому процессу, основным критерием деления товарных позиций на группы станет выступать число подходов/ перемещений складского персонала при выполнении технологический операций, в частности при процедуре комплектации заказов в производство или клиентам.
Степлер SAX 49 | 1238 | 455 | А |
Степлер SAX 51 | 1245 | 410 | А |
Ручка Senator Spring | 4589 | 398 | В |
Ручка Pilot BPGP-10R-F | 4593 | 355 | В |
Ручка Parker Sonet | 4599 | 223 | В |
Ручка Parker Insignia | 4600 | С | |
Ручка Parker Frontier | 4611 | 110 | С |
Ручка Ico Omega | 4678 | 95 | С |
Тонер-картридж HP C7115Х | 5889 | 23 | С |
Тонер-картридж HP C8061A | 5890 | 4 | С |
Таким образом, в группу А вошло 20% товарных позиций (степлер SAX 49 и степлер SAX 51), которые встречались в заказах чаще всего, в группу В – 30% товарных позиций, которые встречались несколько реже, и в группу С – 50% товарных позиций, которые встречались в заказах гораздо реже по сравнению с группой А. На первый взгляд, можно сделать вывод о том, что наибольшее число подходов/ передвижений будет осуществляться по позициям группы А, однако это не совсем так, ведь необходимо учесть еще и такой критерий, как количество отгружаемой продукции. Несмотря на то, что заказов на такую позицию, как «тонер-картридж HP C8061A», было всего четыре, число отгруженных коробов, а следовательно, и число подходов к месту хранения этого товара могло быть гораздо больше.
Рассмотрим методику проведения XYZ-анализа, критерием деления в котором будет число отгруженных универсальных единиц. Пропорциональное деление аналогично соотношению при проведении АВС-анализа, т. е. 20/ 30/ 50. Пример деления товарных позиций по XYZ-анализу приведен в табл. 2.
Тонер-картридж HP C8061A | 5889 | 1800 | X |
Степлер SAX 51 | 1245 | 1550 | X |
Ручка Parker Insignia | 4600 | 580 | Y |
Ручка Senator Spring | 4589 | 530 | Y |
Ручка Ico Omega | 4678 | 525 | Y |
Ручка Pilot BPGP-10R-F | 4593 | 335 | Z |
Степлер SAX 49 | 1238 | 325 | Z |
Тонер-картридж HP C7115Х | 5890 | 305 | Z |
Ручка Parker Frontier | 4611 | 123 | Z |
Ручка Parker Sonet | 4599 | 115 | Z |
Чтобы решить конечную задачу о размещении товаров в «горячую» и «холодные» зоны, необходимо составить матрицу результатов АВС-, XYZ-анализа (табл. 3). Обычно сопоставление результатов проведенного анализа производится в MS Excel с помощью функции сортировки и занимает минимальное количество времени, а в данной публикации мы представим матрицу в виде табл. 3.
Таким образом, после расстановки всех позиций по соответствующим категориям можно сделать вывод, что к «горячей» зоне хранения будут отнесены позиции, находящиеся в квадратах АX, AY, BX (в данном случае – только одна позиция с кодом 1245), к «средней» зоне хранения – позиции, находящиеся в квадратах AZ, BY, CX, и к «холодной» зоне хранения – позиции, находящиеся в квадратах BZ, CZ, CY.
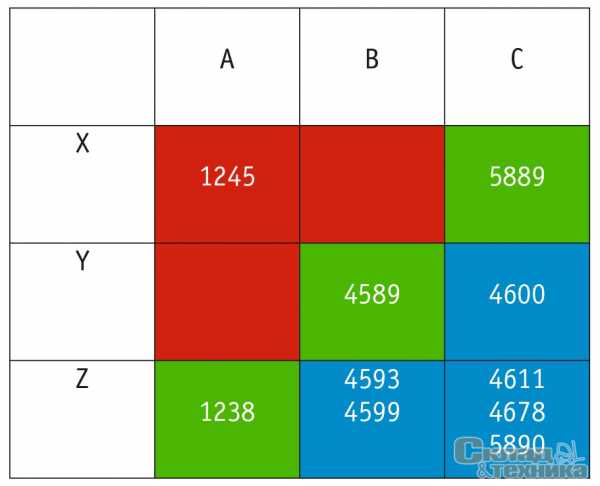
При проведении АВС-, XYZ-анализа следует придерживаться по крайней мере двух правил. Первое – статистические данные должны быть взяты не позднее чем за предыдущий год, с разделением по кварталам и месяцам, так как именно в течение всего годового цикла можно выделить сезоны спроса по каждой товарной позиции, и размещать продукцию по зонам хранения не статично весь год, а перемещать ее между зонами в соответствии с сезонностью спроса. Второе – единицы измерения должны быть унифицированы: если на склад продукция приходит и хранится, допустим, в коробах 15 различных видов, следует измерить геометрические параметры каждого из них и выбрать размеры унифицированного короба, в котором и будет измеряться количество отгружаемой продукции.
После проведения АВС-, XYZ-анализа по каждой товарной позиции вычисляют норму запаса, находящуюся на складе единовременно. Далее определяют число мест хранения для каждой товарной позиции и производят размещение на основе результатов анализа. «Горячая» зона, как правило, располагается ближе к зоне отгрузки, на стеллажах, находящихся в центральном проезде, в нижних ярусах стеллажей, что позволяет существенно сократить время на выполнение технологических операций. Следует отметить, что в настоящее время большинство информационных систем класса ERP или WMS имеют функцию проведения АВС, XYZ-анализа по различным задаваемым критериям.
Второй задачей при размещении продукции на хранение является оптимальное разделение складских запасов. Безусловно, оптимальным является такой вариант, когда весь товарный запас хранится на стеллажах (исключая наливные, насыпные и «негабаритные» грузы), при котором отбираемый запас находится в нижних ярусах стеллажей, а резервный – в верхних. Однако склады с недостаточным финансированием зачастую не имеют возможности приобрести стеллажное оборудование для хранения всего товарного запаса. Для них возможно применение варианта с разделением товарного запаса на две категории и хранением их в двух зонах. В зоне отбираемого запаса на стеллажах хранят только минимальный одно-, двухдневный запас по каждой товарной позиции. В резервной зоне хранения весь оставшийся запас хранится штабельным способом. Пополнение запаса отбираемой зоны хранения производится, как правило, в третью смену, чтобы исключить пересечение потоков. Данный способ позволяет в несколько раз сократить количество стеллажного оборудования и площадь комплектации, а следовательно, и число перемещений между местами отборки.
Комплектация заказов
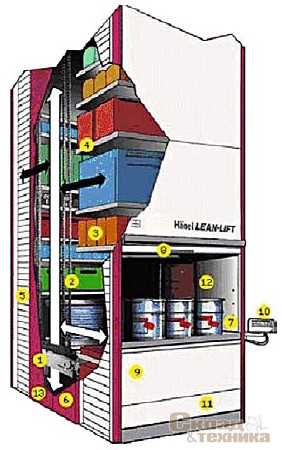
На большинстве складов оптовых торговых и производственных предприятий, а также на складах логистических центров данная операция является ключевой, так как именно от нее зависит уровень логистического обслуживания (скорость выполнения заказа, отсутствие ошибок при сборке и т. д.). При всем том эта операция является одной из самых трудоемких в складском технологическом процессе.
Существует две системы выполнения технологических операций по комплектации – «человек к товару» и «товар к человеку».
Система «товар к человеку» является полностью автоматизированной (рис. 7). Управление передвижением товара осуществляется при помощи пульта управления, при этом сам оператор не производит никаких перемещений, и товар поступает к окну выдачи автоматически. К настоящему времени такие системы в России пока не нашли широкого применения, однако интерес к ним очень высок и число реализованных проектов постоянно растет.
В отношении системы «человек к товару» по результатам хронометража работы комплектовщика, проводимого на 23 складах предприятий оптовой торговли, были получены следующие усредненные результаты: 50% времени комплектовщика расходуется на перемещение между местами отборки, 20% времени – это вынужденный простой (ожидание), 20% – работа с документами, 10% – изъятие с места отборки. Однако существуют методы оптимизации процедуры комплектации, применение которых сокращает общее время сборки заказа за счет полного упразднения простоя и сокращения времени на перемещения между местами отборки.
Рассмотрим типовую схему процесса комплектации заказов (рис. 8).
1. Процедура комплектации начинается с получения накладной на отпуск товара (заявка, лист комплектации и т. д.). Обязательным условием является расположение в документе товарных позиций в соответствии с размещением продукции на складе, иначе создается ситуация, когда накладная составляется в том порядке, как она существует в информационной системе, и комплектовщик вынужден проходить неэффективный путь, т. е. неоднократно возвращаться к ранее пройденным местам и т. д.
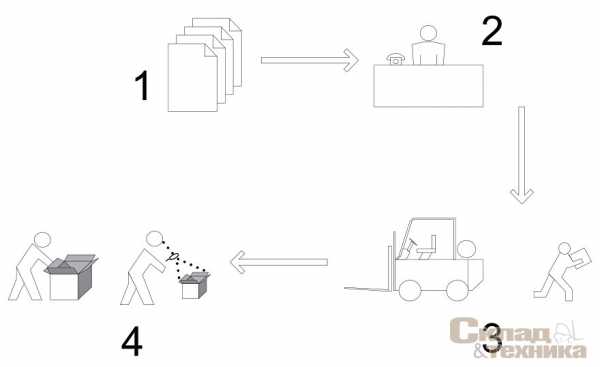
2. Составление маршрутной карты. В работе большинства складов эта процедура не используется вовсе, однако оптимально продуманный путь движения комплектовщика позволяет существенно сократить время на сборку заказа. Критерием составления маршрутной карты будет являться не только размещение адресов нахождения товара в соответствии с их расположением на складе, но и, что более важно, учет принципа «товарного соседства». Например, на складе компании по оптовой продаже канцтоваров комплектовщик с платформенной тележкой отбирает в соответствии с заказом несколько видов ватмана, после чего у него в листе комплектации находится позиция «Бумага для принтера «Снегурочка». Это приводит к тому, что комплектовщик вынужден тратить значительное время на перекладку товара в тележке, а кроме того, эта операция, как правило, проводится в неподготовленных условиях (пыль от бетонного пола и проч.), что часто приводит к ухудшению внешнего вида товара.
3. Отборка груза с мест хранения.
4. Комплектация собранного заказа, его упаковка и маркировка.
Дифференциация в выполнении последних двух операций будет зависеть от вида комплектации – индивидуальной или комплексной. Индивидуальная комплектация заказа заключается в последовательной отборке одного заказа одним сборщиком. Комплексная комплектация – это сборка одного заказа по частям разными комплектовщиками в отдельных секторах склада. При индивидуальной сборке комплектовщик вынужден проходить значительные расстояния, а следовательно, затрачивать большое количество времени при перемещениях между местами отборки. Более того, возрастает вероятность пересечения потоков, т. е. возникновения ситуаций ожидания освобождения технологической зоны другими служащими.
Комплексный способ сборки заказов более эффективен. При таком способе склад разделяется на несколько зон, в каждой из которых работает один комплектовщик. При этом геометрические размеры зон могут быть разными, и важно рассчитать одинаковое число операций, приходящееся на каждую зону, а точнее – время для их выполнения. Например, зона № 7 по геометрическим параметрам будет значительно меньше, чем зона № 1, однако она находится на значительном удалении от зоны приемки/ разгрузки, а значит, время на выполнение операций по доставке заказа будет больше. Пример зонального деления приведен на рис. 9.
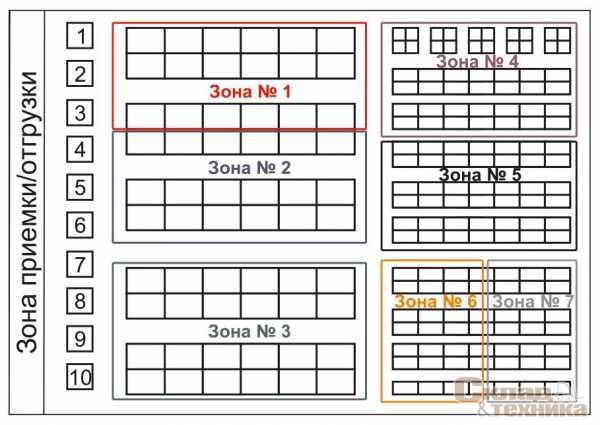
Поступивший заказ разделяют на части, соответствующие зонам склада. После сборки в каждом участке собранную часть передают на участок приемки в квадрат, номер которого обозначен в листе комплектации у каждого комплектовщика, собирающего единый заказ. После сборки всего заказа кладовщик проверяет правильность собранного заказа, а далее производятся предотгрузочные операции.
Преимущества такого метода очевидны. Во-первых, время выполнения заказа сокращается в несколько раз за счет сокращения числа перемещений между местами отборки и упразднения вынужденного простоя. Во-вторых, каждый комплектовщик, «прикрепленный» к конкретной зоне, гораздо быстрее узнает номенклатуру, хранящуюся в ней, и фактически имеет возможность работать без маршрутного листа. В-третьих, появляется возможность закрепить индивидуальную ответственность за состоянием каждой складской зоны. «Минусом» этой системы некоторые руководители складов называют возможность внезапного невыхода на работу части складского персонала и отсутствия в зоне комплектовщика. Однако это уже вопрос административно-организационный, и большинство руководителей крупных складов, вводящие данную систему, сумели справиться с данным негативным фактором методами мотивации и административных взысканий. Во всяком случае, остается возможность «аварийной» переброски персонала из другой зоны.
sitmag.ru
Оптимизация складских процессов при помощи терминалов сбора данных
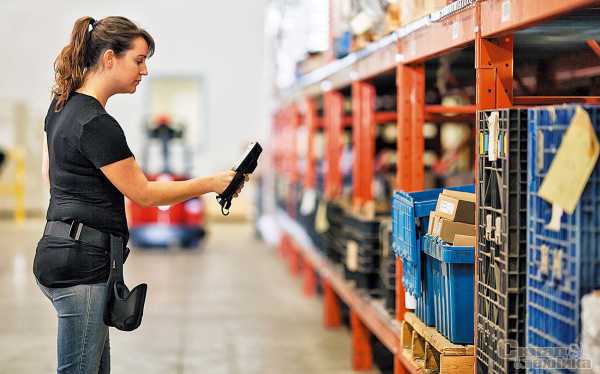
Алексей Шабанов, ведущий менеджер по продукциигруппы компаний «Пилот»
Нелегко отказаться от привычного способа проведения складских процессов. Однако с развитием технологий появляются возможности оптимизировать их, снизив количество времени, затрачиваемого на решение задач, и число операционных ошибок, возникших вследствие действия человеческого фактора. Один из ярких примеров такой оптимизации – использование терминала сбора данных (ТСД), позволяющего «играючи» проводить приемку, инвентаризацию и отгрузку товаров.
Любому складу, независимо от специфики или размера, приходится решать три обязательные задачи: приемка, инвентаризация, комплектация и отгрузка товаров со склада. Многие склады, несмотря на развитие технологий, по-прежнему выполняют эти три задачи вручную. Мало того что процессы проходят медленно, так еще и при их реализации велика вероятность появления операционных ошибок. Чтобы свести на нет влияние этих минусов на работу склада, существуют два пути.
Во-первых, организовать рабочую станцию, чью роль играет обычный компьютер, на который установлена складская информационная система и подключен сканер штрих-кодов. Плюс этого решения в том, что заявленные выше проблемы действительно устраняются. Однако вместо них появляются другие – складские процессы оказываются привязанными к конкретной зоне. Это означает, что, например, при приемке необходимо весь товар при-везти к рабочей станции, чтобы сотрудник склада имел возможность их отсканировать и внести в базу. Если склад небольшой и продукции поступает немного, то этот путь вполне приемлем. Однако если мы имеем дело со складским предприятием большого размера, то привязка к рабочей станции становится обременительной.
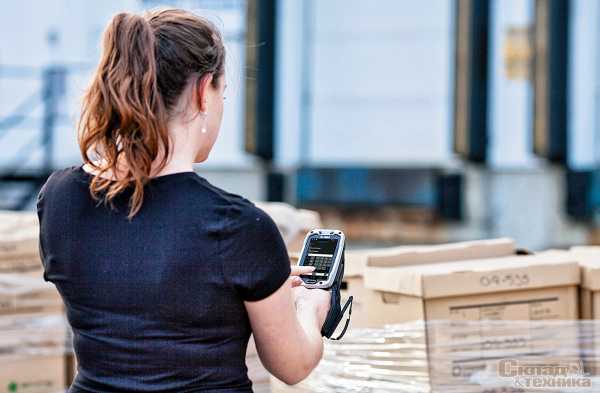
Второй путь – внедрение терминалов сбора данных (ТСД). Этот вариант, как и первый, устраняет минусы ручного выполнения задач, а также обеспечивает мобильность реализации процессов. При этом с развитием технологий стоимость терминалов сбора данных стала относительно невысокой: недорогой ТСД обойдется примерно в 25,5 тыс. руб., стоимость среднего устройства составит от 38 тыс. руб. Причем одно такое устройство мо-жет выполнять не только три перечисленные нами задачи, но и множество сопутствующих. Например, они способны работать в режиме рации, если подключить к ним гарнитуру – такую возможность предоставляют многие производители, включая Zebra, Datalogic, Honeywell. Также ТСД можно использовать как таск-менеджер, установив на них даже почтовый клиент.
Однако мало приобрести терминал сбора данных – важно оснастить его качественным программным обеспечением. Тут ритейлеры идут тремя путями.
Пишут софт для ТСД сами и под каждую задачу готовят приложения. Этот способ не всегда удобен, поскольку количество задач растет как на дрожжах. Соответственно, приходится тратить все больше времени на написание приложений.
Заказывают написание софта под свои нужды у разработчиков. Здесь также приходится столкнуться с рядом неудобств: не всегда небольшая компания способна оперативно вносить требуемые заказчику изменения. Кроме того, постоянная доработка софта может выйти в круглую сумму.
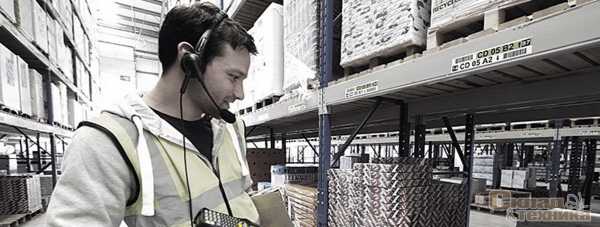
Приобретают промышленное решение. В этом случае важно учитывать, чей разработчик – российский или зарубежный, поскольку во втором случае, учитывая текущую ситуацию на рынке, сложно избежать валютных рисков. Кроме того, зарубежным разработчикам тяжело оперативно адаптировать программное обеспечение под меняющиеся требования российского законодательства. С другой стороны, не каждая отечественная компания обладает такой же экспертизой, как ее иностранные коллеги.
Но какой бы путь владелец склада ни предпочел, ему в любом случае необходимо брать в расчет следующие основные требования, предъявляемые к софту для ТСД.
ПО должно уметь работать как в онлайн-, так и в офлайн-режиме. Работа с устройством в офлайн-режиме привязывает пользователя к рабочему месту: ему придется вручную загрузить данные для приемки накладной на ТСД и уже после этого идти работать. При онлайн-режиме работы накладная поступает на устройство вне зависимости от того, где оно находится. Однако для этого требуется организовать беспроводную сеть и устой-чивый канал связи, а это не всегда возможно: например, из-за множества металлизированных поверхностей, часто присутствующих на складе.
Софт должен модернизироваться по мере развития бизнеса: владельцу склада необходима возможность дорабатывать ПО для ТСД в зависимости от растущих требований. Поэтому во многих промышленных решениях либо уже существуют многочисленные приложения «на все случаи жизни», либо включена возможность их быстрого создания. Например, в нашем «ОмниЛинке» существует «Генератор приложений» – своеобразный конструктор, при помощи которого пользователь без программирования может создать нужное ему приложение.
Программное обеспечения для ТСД должно быть снабжено инструментами интеграции с внешними системами, позволяющими ему получать оттуда данные. Чем больше инструментов интеграции – тем лучше, чем более гибкие они, тем больше возможностей будет у терминалов сбора данных.
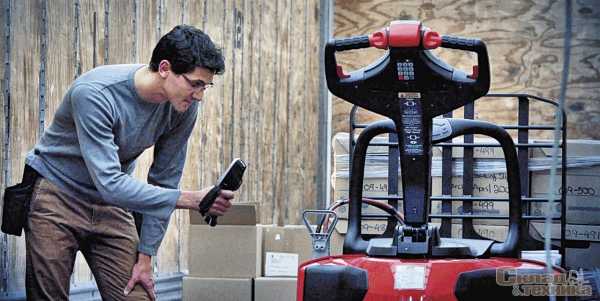
Задача № 1: приемка товаров
Первая задача, с которой неизбежно сталкивается любой склад, – это приемка товаров. В ручном режиме это работает так: сотрудник склада распечатывает накладную и по ней проверяет, какие товары и в каком количестве прибыли. С ТСД процесс выглядит иначе: на устройство выгружается накладная, а работник просто подряд сканирует штрих-коды поступившего товара. В итоге формируется список пришедшей продукции, после чего он отправляется во внешнюю систему. При этом терминал сбора данных позволяет сформировать и отправить как список фактически поступивших товаров, так и перечень расхождений с накладной. Как следствие, работнику склада не приходится искать товар и вруч-ную его пересчитывать.
Один пример из нашей практики. Процесс приемки товаров у одного из наших заказчиков после внедрения мобильного решения стал занимать в 6 раз меньше времени. Задачу, которую раньше выполняли 3 человека в течение часа, теперь реализует один сотрудник за 20 минут.
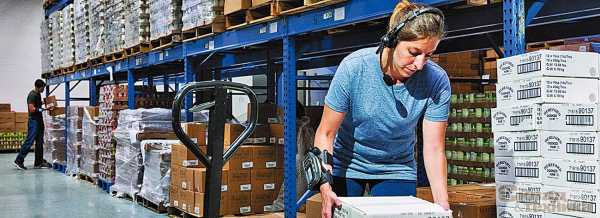
Задача № 2: инвентаризация товаров
Ручной способ инвентаризации мало чем отличается от приемки: сотрудник склада распечатывает перечень товаров, которые по данным внешней системы должны числиться на складе, и проверяет его, обходя все помещение, ища нужную продукцию и пересчитывая ее количество. Если склад небольшой и товаров на нем 10 штук, то такой путь вполне возможен. В противном случае процесс инвентаризации занимает много времени, а его реализация не обходится без операционных ошибок.
С ТСД работник просто сканирует штрих-коды всей попадающейся на глаза продукции. А его софт сам формирует список и отправляет его во внешнюю систему. При этом данные могут идти как перечислением, так и с указанием, в каком количестве представлена каждая товарная позиция.
Поскольку в некоторых случаях инвентаризации разбиваются по участкам, ТСД может сформировать и такой список, привязывая товары к местам хранения. Помимо этого, владелец склада получает данные о том, какой именно сотрудник и в какое время проводил инвентаризацию. Это нужно в том случае, если он хочет проконтролировать зону ответственности операторов.
Пример из практики. У одного из наших заказчиков при «ручном способе» процесс полной инвентаризации 30 магазинов занимал две недели. После приобретения ТСД это время сократилось до одной недели. Он купил всего два терминала сбора данных и просто перевозит устройства из магазина в магазин. Таким образом, появилась возможность за один день инвентаризировать 4 магазина. Данные из каждой точки в онлайн-режиме по-ступают во внешнюю систему. При первой полной инвентаризации с ТСД были обнаружены некоторые товары, давным-давно списанные со склада, так как они потерялись во время проведения ручных инвентаризаций.
Задача № 3: комплектация и отгрузка товаров
Эта задача наиболее актуальна для складов, связанных с интернет-магазинами. В ручном режиме при получении заказа работнику приходится распечатывать его и идти искать, где же в помещении находится нужная продукция, а затем возвращаться к рабочему месту и вносить полученные данные с систему. В результате время обработки заказа занимает приличное время.
С терминалами процесс проходит гораздо быстрее: внешняя система отправляет в ТСД перечень заказа. Устройство показывает работнику склада, где именно находится искомый товар. Тому остается просто пройти в указанное место, отсканировать штрих-код продукции и забрать ее, сформировав заказ. При этом ТСД отправляет уведомление во внешнюю систему о том, что заказ готов, а она, в свою очередь, шлет письмо заказчику, что он может приехать за покупкой.
Пример из практики. Еще один наш клиент – крупный онлайн-гипермаркет – внедрив на складе терминалы сбора данных, сократил время ожидания покупателя на стойке выдачи с 10 минут в среднем до одной–двух минут.
Помимо трех перечисленных процессов, ТСД могут решать множество необходимых задач. Например, выполнять маркировку товаров. Один из наших клиентов поставляет одну и ту же продукцию в несколько розничных сетей. Соответственно, у каждой из сетей есть свои штрих-коды, отличные от тех, которыми промаркированы товары на складе у нашего клиента. На этапе отгрузки оператор комплектует, допустим, 20 упаковок продукции, сканирует ее внутренний штрих-код и выбирает на терминале, для какой именно сети эти товары предназначены. Таким образом ТСД дает команду мобильному принтеру распечатать новые этикетки с необходимыми (правильными) штрих-кодами.
Приведем еще один из наших бизнес-кейсов с магазином автозапчастей. Часть продукции поступает в него упаковками, поэтому требуется отмаркировать ее поштучно. Для этого работник при приеме товара сканирует штрих-код общей упаковки, на основе которого ТСД формирует этикетку для каждого товара.
Работа с терминалом сбора данных значительно сокращает временные затраты на проведение складских процессов, а также сводит к нулю количество операционных ошибок, появляющихся вследствие ручного подхода. Однако важно заранее учесть, какие именно задачи будет решать ТСД, и подобрать подходящее устройство и программное обеспечение к нему.
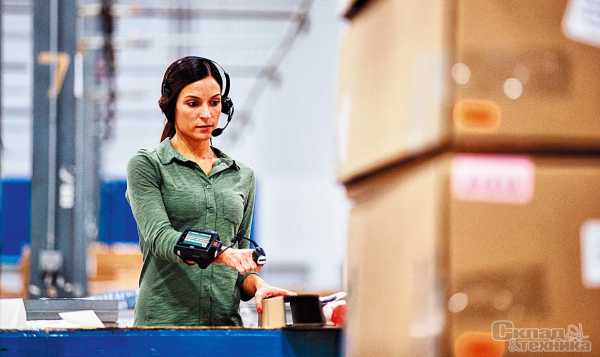
sitmag.ru
Оптимизация складских процессов на предприятиях пищевой промышленности, торговли и сферы питания
Решения по обработке и хранению грузов для различных производств пищевой промышленности от компании «Сидус»
Пищевая промышленность является перспективной и быстроразвивающейся отраслью. Сегодня производители и дистрибьюторы продуктов питания, напитков и сырья для их производства должны выпускать, правильно хранить и реализовывать обширный ассортимент товаров и продуктов. Чтобы эффективно функционировать на рынке, им необходима правильная организация производства и работы склада.
Не секрет, что грамотный подбор оборудования является залогом успешной работы любого склада или предприятия в целом, вне зависимости от его рода деятельности. Располагая обширным перечнем современного оборудования, компания «Сидус» способна предоставить решения по обработке и хранению грузов для различных производств пищевой промышленности: мясной продукции и полуфабрикатов, продуктов из рыбы и морепродуктов, молочной, кисломолочной, плодоовощной продукции и грибов, продуктов питания для отелей и ресторанов, детского питания, хлебобулочных и кондитерских изделий, алкогольных и безалкогольных напитков. Кроме того, ее решения в сфере организации хранения помогут оптимизировать складские процессы и на складах крупных дистрибьюторов или ритейлеров.
Особенности подъемно-транспортного оборудования для пищевой промышленности
Подъемно-транспортная и складская техника, применяемая на предприятиях пищевой отрасли, должна отвечать требованиям санитарно-гигиенических норм. На протяжении всего процесса изготовления и сбыта продуктов питания и напитков необходимо поддерживать чистоту и не допускать присутствия в воздухе вредных выхлопов от работающей техники, причем не только на производстве, но и на складских площадях, куда поступают ингредиенты и готовая продукция и откуда происходит их отгрузка конечным потребителям. Поэтому при организации складских операций на предприятиях пищевой промышленности, торговли и сферы питания оптимальным вариантом будет использование для работ внутри помещений техники с электрическим приводом.
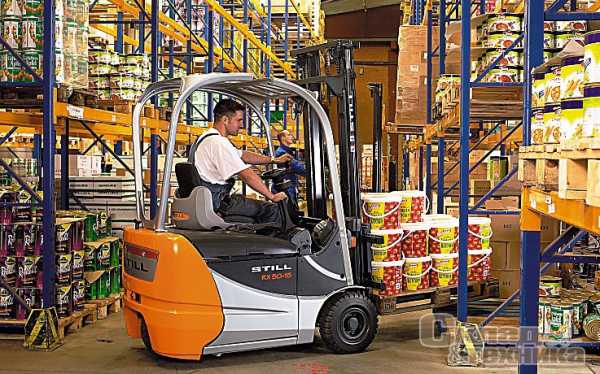
Являясь официальным дилером компании Still GmbH (Германия), ведущего мирового производителя подъемно-транспортной техники, ООО «Сидус» предлагает высококачественные вилочные электропогрузчики грузоподъемностью от 1 до 5 т. Электрические погрузчики Still экологичны, отличаются низким уровнем шума, а дополнительные опции оптимально адаптируют их для применения в пищевой промышленности. Например, оснащение необслуживаемыми гелевыми тяговыми батареями, различными видами навесного оборудования (специальные поворотные захваты для емкостей, сталкиватели для тары с сырьем и др.).
Электропогрузчики комплектуются шинами, не оставляющими следов на напольных покрытиях, а также шинами, стойкими к агрессивной среде (например, солевому раствору, применяемому на производствах мясных и рыбных полуфабрикатов).
Возможно изготовление погрузчиков Still в специальном «холодном» и взрывозащищенном исполнении. Первые применяются для работы в условиях постоянных низких температур (до –30 °С) на так называемых рефрижераторных складах. Эта техника оборудована комфортной отапливаемой кабиной, подогреваемым дисплеем, в системе гидравлики используется низкотемпературное гидравлическое масло, а для вил или другого навесного оборудования предусмотрено особое покрытие. Во взрывозащищенных погрузчиках Still, применяемых, например, в мукомольной промышленности, все узлы и агрегаты защищены от попадания в них взрывоопасных веществ и образования искры, что может привести к возгоранию.

Для электрических погрузчиков, используемых в пищевой промышленности, важен тип установленной батареи. Свинцово-кислотные аккумуляторы подойдут для транспортировки упакованной продукции там, где нет жестких санитарно-гигиенических требований. Гелевые батареи наиболее безвредны и могут быть использованы на тех производствах, где любые выхлопы и испарения могут отрицательно повлиять на качество пищевых продуктов (это также актуально для производства табачных изделий). При этом они абсолютно безопасны и не требуют обслуживания. ООО «Сидус», официальный дилер компании Exide Technologies – лидера на рынке промышленных аккумуляторов, подберет и оснастит электропогрузчик любым типом тяговых аккумуляторных батарей, зарядных станций и дополнительного оборудования к ним.
Для компаний с небольшим бюджетом «Сидус» предлагает электрические погрузчики российского производства грузоподъемностью от 1,5 до 3 т. Модели «Волжский Погрузчик» отличаются неприхотливостью, экологичностью и простотой в управлении и обслуживании. Они отлично справляются с погрузочно-разгрузочными работами на пищевых производствах и складах. За счет использования электроэнергии эти машины работают очень тихо и идеально подходят для транспортировки пищевых продуктов на производстве, а также на территории складских комплексов. Демократичный уровень цен, сжатые сроки поставки, широкий перечень навесного оборудования и дополнительных опций делает их востребованными в «среднем» сегменте рынка подъемно-транспортного оборудования.
На крупных терминалах и складах для осуществления операций погрузки/ разгрузки вне помещений могут использоваться дизельные или газовые погрузчики самой разной грузоподъемности, которые широко представлены в программе поставки компании «Сидус» брендами STILL и «Волжский Погрузчик».
Для внутрискладской транспортировки и комплектации грузов ООО «Сидус» предлагает широкий спектр складской техники STILL и Genkinger-Hubtex (Германия) с электрическим приводом: ричтраки, гидравлические и электрические тележки и штабелеры (с малой высотой подъема и высокоподъемные), электрокары, тягачи, транспортировщики паллет, ручные гидравлические тележки, узкопроходные комплектовщики-электроштабелеры и др.
Линейка подъемно-транспортного оборудования, предлагаемого компанией «Сидус», отвечает всем требованиям и стандартам, предъявляемым к технике, разрешенной к эксплуатации в пищевой промышленности, и поэтому находит широкое применение как на предприятиях пищевой промышленности и сферы питания, так и в других отраслях промышленности и торговли.
Эффективная организация хранения на пищевых производствах и продуктовых складах
Для производителей продуктов, напитков, а также тары и упаковки для них основными принципами оптимального хранения помимо чистоты, экологичности, поддержания заданного температурного режима являются возможность использования оборудования в морозильных камерах и, конечно, эффективное использование площадей.
Для грамотной организации складского пространства ООО «Сидус» рекомендует оборудование SSI Schäffer (Германия) и других зарубежных и российских производителей. Программа поставки SSI Schäffer очень обширна и включает стеллажи различных конфигураций (паллетные, полочные (в том числе наклонные), гравитационные, въездные, консольные, передвижные, мезонинные и др.), тару, контейнеры и поддоны для хранения любых грузов, логистические комплексы, динамические системы хранения и обработки тары и контейнеров и др.
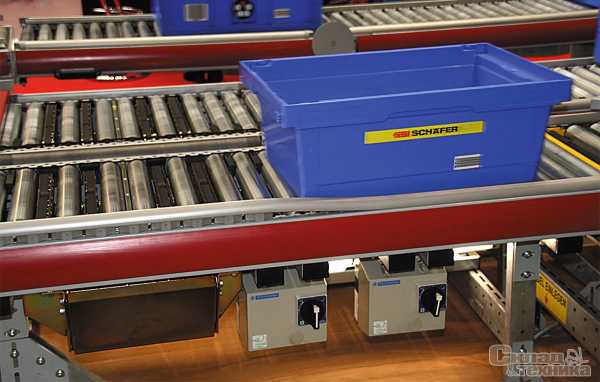
Для производств и складов, имеющих дело с товарами ограниченного срока годности (например, молочная продукция), наиболее оптимальны гравитационные стеллажи, реализующие принцип «First In – First Out» («первый пришел – первым вышел»). Особая конструкция допускает их использование в том числе в морозильных камерах. В холодильных комплексах также выгодно применять систему набивных или передвижных стеллажей, т. к. они обеспечивают эффективное использование дорогостоящих площадей.
На сегодняшний день все больше зарубежных предприятий пищевой и смежных с ней отраслей внедряют на своих производствах автоматизированные системы хранения грузов Kardex. В Германии, Швейцарии, Бельгии, Англии подобные системы функционируют на производствах консервов, напитков, пряностей, а также в крупных сетях гипермакетов и дистрибуционных центров. Их внедрение в складскую систему способствует решению ряда таких задач, как значительное сокращение площадей складирования при повышенном объеме хранения, быстрый доступ к ТМЦ за счет реализации принципа «товар к человеку», полный контроль за движением продукции, ограничение несанкционированного доступа и др.
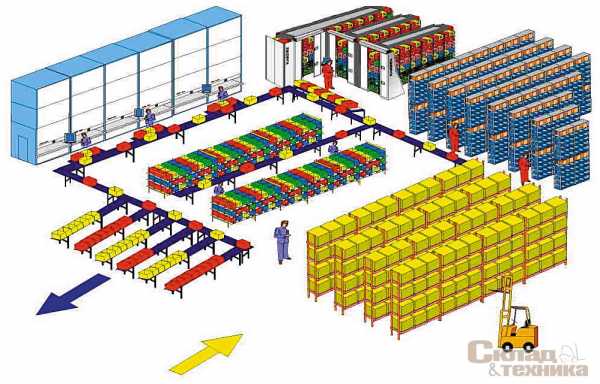
Широкий набор дополнительных опций: изготовление комплектующих из нержавеющей стали, функция поддержания заданного микроклимата, возможность применения оборудования в стерильных помещениях и в условиях низких температур, регулировка скорости работы в зависимости от характера хранимого в ней груза (стекло, фарфор и т. п.) – делает оправданным использование автоматизированных систем хранения Kardex в пищевой промышленности, сфере питания и торговле.
Для пищевых производств и складов особый интерес представляют горизонтальные карусели Kardex. Внедрение этих систем на продуктовых складах приводит к сокращению площадей, времени загрузки/ выгрузки, поиска и доставки хранимых материалов, уменьшению количества ошибок при отборе необходимых артикулов.
Эти и другие автоматизированные склады Kardex карусельного и лифтового типа применяются при хранении, распределении и комплектации продукции на предприятиях, занимающихся производством и сбытом мелкоштучной продукции (приправы, сигареты, БАД, лекарства и пр.). Кроме того, данные системы складирования могут использоваться не только для эффективной обработки готовой продукции, но и для хранения запасных частей, инструментов для обслуживания производственного оборудования. А программное обеспечение Kardex предоставляет возможность отслеживать движение всех товаров и материалов.
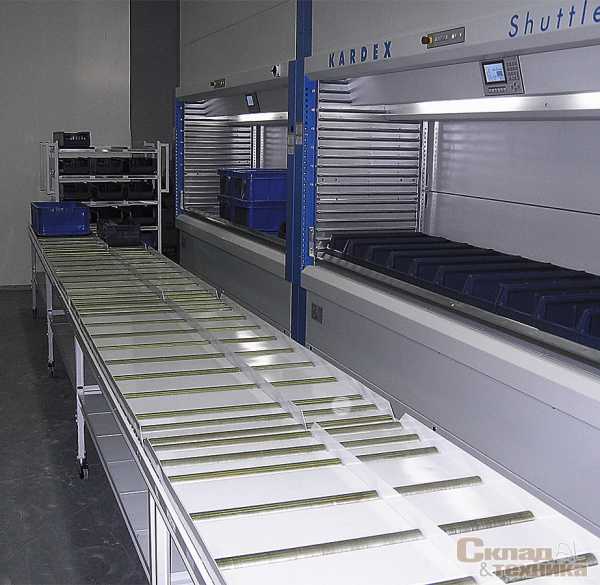
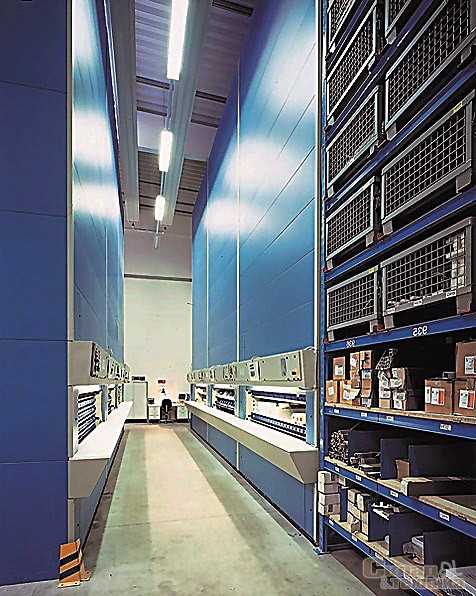
Интеграция оборудования Kardex с холодильными установками обеспечивает хранение и эффективную обработку продуктов, требовательных к температуре. А принцип «First In – First Out» и соответствующее программное обеспечение позволяют применять автоматизированные системы для хранения продуктов с ограниченным сроком годности.
Полный спектр инновационных решений в области автоматизированных систем хранения Kardex (Швейцария) и Intertex (Германия) доступен российским предприятиям и представлен в программе поставки ООО «Сидус» на основании официальных полномочий заводов-изготовителей. Подобные системы способны организовать бережное и эффективное хранение абсолютно любых грузов – от мелких и средних по весу и размерам до крупногабаритных материалов.
Автоматизированные системы Kardex и Intertex позволяют поднять продуктивность, а с ней и конкурентоспособность предприятия в современных условиях за счет повышения скорости обработки грузов при высоком уровне безопасности сотрудников предприятия, занятых на операциях загрузки/ выгрузки, снижения количества повреждений и дефектов грузов, затрат на хранение и оборот грузов или документов. Преимущества от внедрения автоматизированных систем – порядок, чистота, экономия площадей и денежных средств, снижение затрат и влияния человеческого фактора – очевидны.
Компания «Сидус» – эксклюзивный дилер Intertex и Kranwerke, официальный дистрибьютор Kardex, официальный дилер Still, Baumann Rosso, Genkinger-Hubtex, «Волжский Погрузчик», SSI Schäffer, а также партнер Hubtex, располагая широчайшей гаммой современной техники для транспортировки и обработки грузов, предлагает логистам и техническим специалистам предприятий готовые решения по оптимизации и автоматизации складской и производственной логистики в любой сфере деятельности. Комплексные прямые поставки складского оборудования из одних рук – залог высокого уровня интеграции и реального повышения эффективности ваших бизнес-процессов. Полный спектр сервисных услуг от монтажа и гарантийного обслуживания до регулярного ТО и поставок оригинальных запасных частей осуществляется высокопрофессиональной командой опытных специалистов компании.
sitmag.ru
Складские операции: оптимизация процесса комплектации
Ваш консультант: Андрей Хвостиков +7 495 785 7228 Задать вопросЗадать вопрос эксперту
Складские операции: оптимизация процесса комплектации
Для эффективной оптимизации процесса комплектации менеджеру склада необходимо разработать оптимальную стратегию автоматизации, учитывающую тип обрабатываемой продукции (паллеты, короба, штучный товар и т.п.).
19.06.2018
19.06.2018
АНТ Технолоджис
Системный интегратор в области разработки и внедрения WMS системы Logistics Vision Suite
127422
Россия
Млсква
ул. Тимирязевская, дом 1, стр. 2, офис 2148-2150
+7 (495) 785-72-28
Оптимизация складских процессов требует многостороннего подхода. При оптимизации процесса комплектования необходимо учитывать две составляющие. Во-первых, ни одна стратегия или технология не является универсальной и подходящей для каждого конкретного случая. Во-вторых, для эффективной оптимизации складских операций необходимо сочетать несколько инструментариев, включающих сбор данных, усовершенствование процессов, современные технологии.Практический опыт показывает, что процессу автоматизации склада и внедрению складских технологий должен предшествовать подготовительный процесс, который включает в себя проведение АВС-анализа, правильное документирование и анализ текущих процессов с целью выявления некачественных и дальнейшего совершенствования складских операций.
Для эффективной оптимизации процесса комплектации менеджеру склада необходимо разработать оптимальную стратегию автоматизации, учитывающую тип обрабатываемой продукции (паллеты, короба, штучный товар и т.п.).
Рассмотрим действия, необходимые для оптимизации процесса комплектации на складе:
АВС-анализ
Первым рекомендуемым шагом для оценки эффективности управления запасами является сбор данных. Одним из лучших способов сделать это – провести АВС-анализ ассортимента продукции.
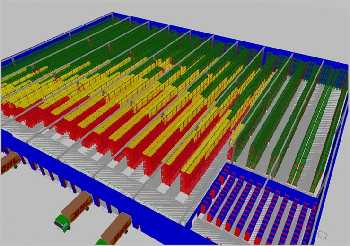
АВС-анализ позволяет классифицировать груз на три категории в соответствии с объемами и частотой заказов. Задача заключается в необходимости распределения запасов согласно скорости оборота, т.е. товар с высокой скоростью оборота (А) размещается ближе к зоне отгрузки, товар с низкой скоростью (С) – дальше от зоны отгрузки. В результате меньше времени тратится на передвижение работника и сокращается рабочее время на сборку товара.
После проведенного анализа высокооборачиваемый товар (красная зона) был перемещен в более доступные зоны, хранение менее востребованного товара (зеленая зона) организовано в глубине склада.
Выбор правильной методологии комплектации
Когда мы выбираем метод оптимизации комплектации, то сталкиваемся с необходимостью организации наиболее оптимального способа организации процесса. В то время как для выполнения большинства операций используется подход «отбор по заказу» (один из самых неэффективных способов), существуют методики, внедрение которых значительно повышают эффективность выполнения отбора товара на складе.
Основная задача в этом случае заключается в организации процесса таким образом, чтобы сократить маршрут комплектовщика при обходе мест хранения товара и исключить лишнее перемещение.
Существует две схемы комплектации — “человек к товару” и “товар к человеку”. Система “товар к человеку” рентабельна только при полной автоматизации процессов укладки и отбора товаров. В схеме “человек к товару” половина времени комплектовщика расходуется на перемещение между адресами отбора, 20% времени — вынужденный простой (ожидание), 20% — работа с документами, 10% — изъятие товара с места отбора. Оптимизация комплектации направлена на сокращение времени простоя и перемещений.
В зависимости от организации процесса период перемещения комплектовщика между зонами сборки может занимать до 50% от всего времени сборки товара
Схема «человек к товару» основана на том, что комплектовщик на основании заказа (или части заказа) перемещается по складу и собирает необходимые позиции. По завершении сборки необходимого товара заказ доставляется в зону упаковки и отгрузки.
Рассмотрим наиболее популярные методы реализации схемы «человек к товару», применяемые сегодня на складах:
Отбор по заказу / Индивидуальный отбор

При индивидуальном отборе комплектовщик ответственен за сборку всех позиций заказа. С детальным списком необходимого для сборки товара работник перемещается по складу и полностью собирает заказ.
Этот подход будет эффективен только для заказов, состоящих из небольшого для отбора списка товаров. Заказы обрабатываются по очереди, точность сборки достаточно велика, необходимость обработки товаров минимальна, отобранный товар сразу поступает с места хранения в зону отгрузки.
Недостатком этого метода является низкая эффективность и точность сборки для заказов, состоящих из большого количества позиций. При увеличении наименований в заказе количество ошибок возрастает.
Комплексный отбор
Эффективность комплексного отбора выше, чем индивидуального, так как в этом случае одновременно группой комплектовщиков собирается несколько заказов.
ИТ-система формирует для сборщика комплектовочный лист, где указывается наиболее оптимальный маршрут для одновременного отбора нескольких заказов.
Если нужно какие-либо заказы собрать в первую очередь, то WMS-система, поддерживающая функцию комплексного отбора, укажет приоритет сборки определенных позиций.
Зоновая комплектации
При зоновой комплектации склад делится на несколько зон, каждая из которых закреплена за отдельным сборщиком.
Во время комплектации заказы могут передаваться из одной зоны в другую в коробках, тележках, паллетах, конвейерах и т.п. Если заказ формируется из некоторого количества товарных позиций разных зон, то для каждой зоны формируется лист комплектации, который назначается для отбора закрепленному за зоной сборщику.
Разделение сборщиков по зонам и их знания о месторасположении товара в сочетании с возможностью одновременной сборки нескольких заказов позволяют значительно увеличить скорость и эффективность процесса комплектации.
Зоновую комплектацию рекомендуется применять на складах и распределительных центрах где обрабатывается большое количество товарных позиций и заказов.
Волновая комплектация
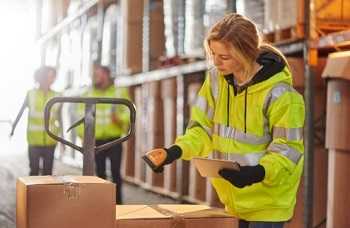
При волновом способе комплектации заказы группируются и передаются сборщикам в планируемое время, зависящее от длительности сборки заказов и специфики работы склада.
Волновая комплектация наиболее эффективна при управлении складом WMS-системой. WMS-система рассчитывает и запускает последовательные волны, зависящие от специфических критериев их формирования.
Одним из преимуществ волновой сборки является возможность сокращения рабочей нагрузки на каждого сборщика, что позволяет ему сосредоточится на специфических задачах (операциях) комплектации каждой волны.
Внедрение технологий: Мы рассмотрели основные варианты оптимизации процесса комплектации, теперь рассмотрим технологические аспекты
Сканеры штрих-кодов
Внедрение методологии штрихкодирования и использование в работе сканеров штрихового кодирования является один из самых простых и эффективных вариантов для улучшения складских операций. Благодаря использованию штрихкодирования мы можем более эффективно идентифицировать продукцию и ее местоположение.
Сочетая использование сканера штрих-кодов и комплектовочного листа сборщик может подтвердить безошибочный отбор позиций товара для каждого заказа. Применение штрихкодирования на складе позволяет работникам выполнять операции быстрее с минимальными ошибками.
Переносные компьютеры
Переносные компьютеры – это еще одна технология, позволяющая достигнуть значительных результатов в оптимизации складских процессов.
Переносные компьютеры оборудованы небольшим экраном и клавиатурой, с помощью которых пользователи взаимодействуют с WMS-системой в режиме реального времени из любой точки на складе.
Ношение устройства на запястье оставляет руки отборщика свободными для выполнения необходимых операций.
Доступность внедрения этой технологии должно поддерживаться функциональными возможностями работающей на складе WMS-системой.
Голосовой отбор
Использование голосового отбора в процессе комплектации повышает эффективность отбора. Отборщик, оснащенный головной гарнитурой с микрофоном, подключается к WMS-системе по беспроводному соединению.
Выполняя комплектацию, оператор, с помощью голосовых команд, взаимодействует с системой управления складом, программа, в свою очередь, передает звуковую информацию о месте, количестве необходимого для отбора товара.
Основные преимущества:
- Повышение точности сбора и производительности
- Сокращение ошибок ввода данных
- Многоязычность
И в заключение, важно понимать, что главный фактор оптимизации складских процессов складывается из возможности сбора и анализа данных, улучшения текущих процессов, внедрения правильных технологий в «слабых» местах.
Полезная информация- Logistics Vision Suite - WMS-система, ориентированная для управления складом средних и крупных предприятий. Возможность гибкой настройки инструментария и высокие компетенции команды внедрения гарантируют сжатые сроки внедрения и успешность всего проекта в целом. Узнать больше
- Видео реализованных проектов. Смотреть
Если Вам необходима дополнительная информация об улучшении складских процессов, пожалуйста, обращайтесь к нашим специалистам по телефону 8(495) 785-7228 или e-mail [email protected]
www.ant-tech.ru
Оптимизация складских процессов - Складская Логистика
Проектирование складских технологических процессов – это необходимое условие для достижения очень важной цели, такой как оптимизация деятельности склада.
При создании подобного проекта специалисты ООО «Складская Логистика» выполняют следующие работы:
- Выбор и систематизация функций и целей складской системы.
- Определение требований, предъявляемых к аппаратно-программным продуктам.
- Анализ грузопотоков и товарной номенклатуры с учетом возможности их изменения.
- Выбор параметров склада с перспективой расширения.
- Составление схемы хранения товарных групп по номенклатуре.
- Разработка оптимальных маршрутов для транспортировки товаров.
- Определение мер по увеличению эффективности использования людских ресурсов.
Результатом вышеперечисленных работ является проект оптимизации, опираясь на который, наши клиенты получают такие результаты, как:
- Эффективное управление всеми операциями и процессами на складе.
- Увеличение пропускной способности склада.
- Минимализация затрат на рабочие ресурсы.
- Оптимизация планировки склада.
- Снижение товарных остатков.
- Сокращение времени на обработку (распределение и сборку) товарных заказов, а также на другие операции.
- Повышение уровня обслуживания клиентов.
Сотрудничество с нашей компанией – это гарантия достижения отличных результатов в логистическом бизнесе!
Вопросы, наиболее часто задаваемые нашими клиентами:
Вопрос: «Каким образом оптимизировать складские процессы?»
Ответ: «Необходимо проанализировать и оценить каждую операцию и ее влияние на работу склада. И тогда, опираясь на полученные данные, можно разработать новую систему управления или усовершенствовать старую».
Вопрос: «К кому можно обратиться для проведения аудита нашего склада? Возможно ли сделать сравнение нашей работы с работой аналогичных логистических организаций?»
Ответ: «ООО «Складская Логистика» проводит аудиторские работы любой сложности. Мы выявляем достоинства и недостатки в деятельности склада, а затем, используя результаты анализа, даем рекомендации, выполняя которые, Ваша компания займет лидирующие позиции в логистическом бизнесе».
Вопрос: «Как лучше организовать работу складских сотрудников?»
Ответ: «Мы анализируем работу склада в целом и каждый процесс отдельно. На основании полученной информации мы определяем потребность в рабочей силе, количество рабочих смен и интенсивность работы, а также даем конкретные рекомендации по оптимизации того или иного процесса».
Вопрос: «Возможно ли рассчитать максимальную продуктивность склада?»
Ответ: «Да, возможно. Разрабатывая проект оптимизации, сотрудники нашей компании делают расчеты, позволяющие предусмотреть возможное расширение склада и увеличение пропускной способности, чтобы добиться выхода на максимальную рабочую мощность. Также мы прогнозируем наступление времени, когда будет необходимо модернизировать Ваш склад».
brambling.ru
Кейс по оптимизации склада, пример оптимизации склада
В этом примере представлено типичное "ручное управление": руководитель работает в роли диспетчера, раздавая поручения в ответ на меняющуюся ситуацию. Все действия - это реакция на события внешней среды, нет действий по формированию желательных событий во внешней среде. Мы рассмотрели переход к управляемости от этого традиционного хаоса.
Проблемы состояния "как было":
Что у нас нового?Машины приезжают без графика, кто когда хочет, кроме своих. Начальник склада даёт задания работникам склада в режиме ручного управления "вы грузите эту, а вы — эту машину". Какие машины грузить и в какой очерёдности, сколько грузчиков и где работают — определяет начальник склада каждый раз в ручном режиме на ближайшее время. Сотрудники работают по факту — «что сказали, то и делают», и не знают, что будут делать, например, через два часа. Начальник склада выступает в роли незаменимого сотрудника и постоянно занят.
Лишь малая часть заказов собирается заранее (до приезда машины). При возможности, если есть не занятый рабочим процессом персонал, заранее начинается сбор завтрашней отгрузки для собственной доставки. В основном собирают заказы, где много «мелочёвки», так как на складе нет зоны отгрузки (места для хранения скомплектованных заказов) и собранные заказы хранят до утра в проходах. Кроме того, всякая сборка «заранее» — это не на ту машину, что приедет через час, а на ту, что приедет завтра.
Отсюда — невозможно предсказать, когда будет погружена та или иная машина. А часто нельзя сказать и когда машина будет поставлена под погрузку, ведь часто получаются "пики" и "провалы" в нагрузке.
Цель проекта оптимизации процессов на складе
• Сделать управляемым процесс погрузки, для дальнейшего его совершенствования.• Иметь возможность назвать клиенту время, когда он должен приехать под погрузку.• Сократить время нахождения машины под погрузкой или на территории склада (время простоя без погрузки).
Результаты проекта оптимизации склада:
1. Управляемость: каждый клиент знает, во сколько его поставят на погрузку и во сколько он уедет.2. Повышение скорости работы (уменьшено время полного обслуживания от въезда машины до выезда).3. Сформирована понятная система приоритетов между заказами.4. Сделано описание бизнес-процессов работы склада, должностные инструкции и чеклисты.5. Снижение рекламаций (недостача, пересорт, недогруз, брак).6. Высвобождение времени начальника склада от ручного управления.
Что было сделано:
1
Вычислен оптимальный размер зоны хранения скомплектованных заказов (она не должна быть излишне большой, неправильно собирать сегодня всё на завтра – потребуется слишком большая площадь). Лучше собирать несколько ближайших машин (которые скоро приедут). И соответственно этому разработан порядок комплектации. Выявили возможность выделить место.
2
Сформирован «костяк» графика погрузок из своих машин и согласованных с клиентом сроков заезда клиентских машин. На него уже «навешиваются» все внезапно появляющиеся машины. Из графика автоматически формируются сменные задания. (Теперь это решается в начале смены на всю смену).
Что получилось
Основная масса бригад теперь работает в плановом режиме, по сменному заданию. Теперь не ставят разовые задачи комплектовщикам и грузчикам (основной части из них), т.е. меньше суеты.Существует график погрузок и комплектаций, таким образом, клиенту может быть назначено время, когда встать под погрузку (время может быть назначено по телефонному звонку на следующий день или даже в текущий день, а если клиент не предупредил о прибытии – то ему в момент приезда назначаем время, в которое сможем приступить к его погрузке)
Все, кто приехал вовремя - не простаивают в ожидании (максимум минут 10, пока доделывают предыдущую машину, если был какой-то форс-мажор). Сократилось время простоя машин без погрузок (кроме случаев, когда машина опоздала или приехала без звонка).
Сократилось время простоя грузчиков и комплектовщиков, минимизирована необходимость постоянного оперативного управления ими. С учетом объёма заказов на следующий день определяется количество грузчиков (не выводим лишних грузчиков).
3
Выделено две "резервных" бригады, которые работают с несрочными заказами и прерываются при появлении срочных заказов или указаний начальника склада. Таким образом, в любой момент есть люди для срочной работы, и при этом они не простаивают (На складе есть "избыток" ворот, т.е. погрузочных ворот больше, чем бригад).
4
Разработан регламент процесса «Управление потоком заказов на складе» в варианте «Как надо» с учётом выполненного физического изменения рабочих процессов. Вся эта работа по управлению, которую делает начальник склада в новом процессе, теперь описана, таким образом чтобы и другой человек мог ее освоить и выполнять. Плюс высвободилось время начальника склада, который сможет больше времени уделять совершенствованию работы склада.
5
Разработана методика для расчета нормативного времени комплектации и погрузки. Сделана разбивка товаров на группы, проведение оценки нормативного времени для каждой выделенной группы. Теперь по накладной можно посчитать, сколько времен займёт сборка (комплектация) заказа. Это необходимо для определения времени обслуживания машин. В дальнейшем оценку можно будет встроить в 1С. В дальнейшем по нашей методике пересчитываются нормативы при изменении ассортимента или размещения товаров на складе.
spb-progressor.ru
Оптимизация складских операций. Практические рекомендации Клуба логистов.
Эффективность складских операций является ключом к успеху любой компании, которая обрабатывает заказы. Когда эффективность отстает от необходимых объемов и скоростей обработки, товары не могут прибыть в пункты назначения клиентов в срок, заказы могут заблудиться, а низкие уровни запасов могут привести к их истощению. Вот несколько советов по оптимизации складских операций от Клуба логистов.
1 . Сведите к минимуму количество касаний.
Ручные операции замедляют движение через склад и могут привести к ошибкам. Автоматизация сбора, упаковки, и транспортных процессов на складе, минимизируют количество передачи партии товара от человека к человеку и, следственно, снижается риск потерь и замедления процесса обработки грузов. Так же это позволит снизить затраты на человеческий труд.
2. Перераспределите часть процессов WMS на Warehouse Control System (WCS).
WCS – система управления складом, основная функция которой заключается в координации работы всех элементов автоматического склада между собою. Система координирует работу отдельных участков складского комплекса в соответствии с заданными стратегиями управления и заданиями, полученными от WMS. Это позволит организовать максимально пропускную способность системы и производительность, а также обеспечить видимость для потенциальных «узких мест».
3. Интуиция тоже важна
При размещении грузов используйте логические последовательности (пример Клуба – запчасти ходовой системы автомобиля, детали двигателей и т.д.), которые будут понятны всем работникам. Размещайте грузы так, чтобы интуитивно будут искать их.
4 . Соберите данные в режиме реального времени о протекании складских процессов.
Постоянно изменяющиеся требования клиентов диктуют требования к гибкости существующих складов. Для поддержки постоянного улучшения процессов склада, и обеспечения выполнения бизнес-целей, собирайте и анализируйте данные в реальном времени от выполнения заказов. Бенчмаркинг производительности и анализ собранных данных может способствовать более обоснованным решениям о том, как реагировать на меняющиеся требования клиентов и бизнес-целей .
5. Проводите обновление склада выборочно.
Дополнительная операция или смена бизнес-процесса по всему складу, введенная Вами одновременно на всех участках склада может замедлить работу склада, сбить с толку персонал, а также сгенерировать часть ненужной работы, которая так же замедлит работу склада. Поэтому проводите реформы поэтапно на каждом из участков.
6. Планируйте движение грузов по всему складу – от зоны приемки и до зоны отгрузки, включая транспортные внутренние операции.
Во многих организациях руководители цепочки поставок и внутри складские операции планируются отдельно, что часто негативно влияет на корпоративные цели. Планирование должно происходить совместно для того, чтобы координировать все зоны склада с целями и общими стратегиями.
7. Совместите складские операции с ключевыми бизнес-целями.
Даже если под давлением клиентов вносить изменения, не игнорируйте свои общие цели бизнеса. Сосредоточьтесь на действиях, которые отвечают стратегии .
8. Установите гибкость и ловкость на складе.
При выборе WMS позаботьтесь о том, чтобы она легко интегрировалась с ERP системой, чтобы иметь возможность вносить изменения быстро, когда вы сталкиваетесь с конкурентным давлением.
9. Установите ключевые показатели эффективности.
Измерьте результаты, и внести изменения, чтобы улучшить эффективность вашего бизнеса.
Клуб логистов
При копировании материала ссылка на сайт http://www.logists.by/ обязательна!
www.logists.by