4.Оптимизация раскроя древесностружечных плит на заготовки. Оптимизация линейного раскроя
Линейный раскрой в Excel : Блог Александра Воробьева
Опубликовано 02 Дек 2015Рубрика: Справочник Excel | 24 комментария
Экономичный линейный раскрой материалов (раскрой погонажа) актуален для многих отраслей производства и в строительстве. Это — распил бревен и досок в деревообработке, резка прутков, арматурных стержней, уголков, швеллеров, труб, двутавров на заготовки...
...в производстве металлоконструкций и машиностроении, поперечный раскрой рулонов с бумагой и тканью в целлюлозной и легкой промышленности.
Не смотря на кажущуюся простоту, решение задач линейного раскроя является весьма не легким, но стоящим делом. Внедрение научного подхода к раскрою погонажных материалов позволяет снизить расходы на них иногда более чем на 10%! Дочитайте статью до конца и убедитесь в правоте этих слов.
Рассматриваемая тема относится к задачам линейного программирования. Для решения таких задач ученые в последние 70 лет придумали несколько различных методов.
Метод индексов Л.В. Канторовича и В.А. Залгаллера при определенном навыке позволяет «вручную» без использования вычислительной техники эффектно выполнять линейный раскрой. Любопытным читателям рекомендую с этим методом ознакомиться, прочитав книгу вышеназванных авторов «Рациональный раскрой промышленных материалов».
Симплекс-метод, основанный на идеях Л.В. Канторовича, был описан и детально разработан рядом ученых из США в середине 20 века. Надстройка MS Excel «Поиск решения» (Solver) использует этот алгоритм. Именно с помощью этого метода и Excel мы будем в этой статье решать задачу линейного раскроя.
Позже появились и получили развитие генетический, жадный и муравьиный алгоритмы. Однако, ограничимся их перечислением и перейдем к делу, не забираясь в дебри теорий (хотя там, «в дебрях», очень интересно).
Включим Excel и на простом примере порезки металлических стержней на детали познакомимся с одним из способов решения практических задач линейного раскроя. Часто математики эту задачу называют «задачей о распиле».
Исходные данные для примера я не стал придумывать, а взял из статьи Покровского М.А. «Минимизация неизбежных потерь материалов в промышленном производстве при их раскрое на штучные заготовки» опубликованной в №5 (май 2015) электронного научно-технического журнала «Инженерный вестник» издаваемого ФГБОУ ВПО «МГТУ им. Н.Э. Баумана» (ссылка: engbul.bmstu.ru/doc/775784.html).
Цель, которую я преследовал – сравнить полученные результаты решения задачи.
Пример решения задачи линейного раскроя в MS Excel.
Договоримся, что:
1. Заготовки – это исходный материал в виде прутков, полос, стержней и т.д. одинаковой длины.
2. Детали – это элементы, которые необходимо получить, разрезав исходные заготовки на части.
3. Ширина пила, реза, руба принята равной нулю.
Условие задачи:
Для комплектации одного из заказов заготовительный участок должен порубить на комбинированных ножницах из одинаковых прутков-заготовок длиной 1500 мм три типоразмера деталей:
151 штуку длиной 330 мм
206 штук длиной 270 мм
163 штуки длиной 190 мм
Требуется найти оптимальный план раскроя, использующий минимальное количество материала и дающий, соответственно, минимальное количество отходов.
Исходные данные:
1. Длину исходных заготовок Lз в миллиметрах записываем в объединенную ячейку
D3E3F3: 1500
2. Присваиваем номера i всем типоразмерам деталей, начиная от самой длинной и заканчивая самой короткой в ячейках
D4; E4; F4: 1; 2; 3
3. Длины деталей Lдi в миллиметрах пишем в
D5; E5; F5: 330; 270; 190
4. Количество деталей Nдi в штуках заносим в
D6; E6; F6: 151; 206; 163
5.Приступаем к очень важному этапу – заполнению вариантов раскроев.
Необходимо запомнить и понять 2 принципа выполнения этой работы.
1. Длины отходов должны быть меньше самой маленькой детали (0<Loj<Lдmin).
2. «Укладку» деталей в заготовку начинаем с самых больших деталей и с самого большого их количества, последовательно двигаясь в сторону уменьшения.
Если какого-нибудь типоразмера деталей в варианте раскроя нет, то ячейку оставляем пустой, ноль писать не будем для облегчения визуального восприятия таблицы.
Вариант раскроя №1:
Попытка выкроить из одной заготовки 5 деталей №1 невозможна, поэтому пишем в ячейку
D7: 4
Добавить в раскрой деталь №2 или деталь №3 также невозможно, поэтому оставляем пустыми ячейки
E7 и F7:
Вариант раскроя №2:
Уменьшаем на 1 от предыдущего варианта количество деталей №1 и записываем в
D8: 3
Пробуем добавить 2 детали №2 – не получается, поэтому дополняем в
E8: 1
Остается возможность дополнить раскрой деталью №3. Заносим в
F8: 1
Придерживаясь озвученных принципов, заполняем по аналогии все возможные в данном случае 18 вариантов раскроев.
Сделав пару-тройку таблиц вариантов раскроев самостоятельно, вы уясните логику действий и будете тратить считанные минуты на эту работу.
Если при раскрое не выполняется первый принцип, то ячейка с длиной отхода автоматически окрашивается в красный цвет. Условное форматирование, примененное к ячейкам G7…G24, наглядно поможет вам в этой работе.
В ячейках H7…h34 ничего не пишем! Они используются для вывода результата решения!
Прошу уважающих труд автора скачать файл с примером после подписки на анонсы статей. Подписные окна расположены в конце статьи и наверху страницы.
Ссылка на скачивание файла с примером: lineynyy-raskroy-v-excel (xls 38,5KB).
Подготовка к решению:
* В ячейках G7…G24 вычисляются длины отходов (обрезков), остающиеся в результате выполнения раскроев, по формуле
Loj=Lз— Σ(Lдi*Nдij)
6. Количество деталей каждого типоразмера, изготовленных по всем примененным вариантам раскроя, будут подсчитываться в ячейках D26, E26 и F26 по формуле
Nдiрасч=Σ(Nдij*Nзj)
Количество деталей в найденном в конце решения плане раскроя должно полностью соответствовать заданному количеству деталей!
7. Необходимое число заготовок для выполнения оптимального плана раскроя будет определяться в объединенной ячейке D27E27F27 по формуле
Nзрасч=ΣNзj
8. Общая длина всех заготовок, необходимых чтобы выполнить линейный раскрой всех деталей будет подсчитываться в объединенной ячейке D28E28F28 по формуле
LзΣ= Lз*Nзрасч
9. Общая длина всех отходов, получаемых при выполнении найденного плана раскроя, будет считаться в объединенной ячейке D29E29F29 по формуле
LоΣ= Σ(Lоj*Nзj)
10. Доля отходов, полученных при выполнении оптимального плана линейного раскроя от общего количества использованного материала, будет вычисляться в объединенной ячейке D30E30F30 по формуле
Ωo= LоΣ/LзΣ
Решение:
Подготовка завершена, определены 18 вариантов наиболее оптимальных раскроев одной заготовки на детали и вписаны все необходимые формулы. Теперь предстоит решить главную задачу: определить оптимальный план раскроя – сколько заготовок, и по каким вариантам раскроев резать, чтобы в итоге получить все необходимые детали в нужном количестве при минимуме отходов.
1. Выбираем в главном меню «Сервис» - «Поиск решения…».
2. В появившемся одноименном окне «Поиск решения» производим настройки.
2.1. Назначаем целевой функцией общую длину отходов LоΣ и вводим ссылку в окно целевой ячейки.
2.2. Устанавливаем переключатель «Равной:» в положение «минимальному значению».
2.3. Указываем ячейки с переменными Nзj в окне «Изменяя ячейки».
2.4. Вводим ограничения в одноименное окно. В качестве условий указываем необходимость равенства заданного Nдi и расчетного Nдiрасч количества деталей, а так же на переменные Nзj – расчетное количество заготовок по вариантам раскроев – накладываем ограничение: это должны быть целые числа.
3. Нажимаем кнопку «Параметры» и в выпавшем окне «Параметры поиска решения» выполняем настройки так, как показано на следующем скриншоте. Закрываем окно кнопкой «ОК».
4. В окне «Поиск решения» нажимаем кнопку «Выполнить» и ждем, пока Excel найдет решение. Это может длиться несколько минут.
5. После сохранения найденного решения кнопкой «ОК», результаты отобразятся в ячейках H7...h34 на листе Excel.
На следующей картинке показан найденный оптимальный линейный раскройный план.
Что в итоге?
Линейный раскрой в Excel заготовок для задач подобных рассмотренной в этой статье выполняется описанным выше методом за 10-15 минут! «Вручную», не зная метод индексов Канторовича, за такое время решения не найдешь.
Запустив «Поиск решения» несколько раз при разных параметрах поиска, удалось найти 5 различных планов рубки заготовок. Все 5 планов требуют одинаковое число заготовок – 93 и дают отходов всего 2,21%!!! Эти планы почти на 6% лучше, чем план, рассчитанный Покровским и более чем на 10% экономичнее «Традиционного» плана (смотри ссылку на первоисточник в первой части статьи). Очень достойный результат достигнут быстро и без применения дорогостоящих программ.
Следует заметить, что надстройка Excel Solver («Поиск решения»), использующая симплекс-метод при решении задач линейного программирования, может работать не более чем с 200 переменными. В приложении к рассмотренной нами задаче линейного раскроя это означает, что количество раскроев не может превышать 200 вариантов. Для простых задач этого достаточно. Для более сложных задач следует попробовать применить «смесь» «жадного» алгоритма и симплексного метода Solver, отобрав из полного списка раскроев не более 200 самых экономичных. Далее запасаемся терпением и добиваемся результатов. Можно попытаться разбить сложную задачу на несколько простых, но «уровень оптимальности» найденного решения будет при этом, скорее всего, ниже.
Может быть, рассмотренный вариант решения вопросов линейного раскроя и не «высший пилотаж», но однозначно шаг вперед по сравнению с «традиционным» подходом на многих производствах.
Использование надстройки MS Excel «Поиск решения» (Solver) было на блоге уже однажды рассмотрено в статье «Бак для воды? «Поиск решения» в Excel!». Думаю, что этот замечательный инструмент достоин пристального внимания и еще не раз поможет изящно и быстро решить ряд новых нетривиальных задач.
P.S. Ссылки на лучшие из бесплатных программ линейного раскроя, найденных мной в Сети:
http://stroymaterial-buy.ru/raschet/70-raskroy-lineynih-izdeliy.html
http://forum-okna.ru/index.php?app=core&module=attach§ion=attach &attach_id=7508
Программы по первым двум ссылкам решают рассмотренную задачу, используя 94 заготовки. Первая программа на других тестах показала чуть лучшие результаты, чем вторая.
http://forum.dwg.ru/attachment.php?attachmentid=114501&d=13823277 74
http://www.planetcalc.ru/917/
Программы по последним двум ссылкам реализуют жадные эвристики и выполняют линейный раскрой в задаче из статьи, используя аж целых 103 заготовки. Применение жадных алгоритмов оправдано в случаях необходимости снижения общего времени операции резки при слишком большом количестве вариантов раскроев в более оптимальных планах.
Ниже статьи в блоке «Отзывы» можете написать свои комментарии, уважаемые читатели.
Другие статьи автора блога
На главную
Статьи с близкой тематикой
Отзывы
al-vo.ru
Линейная оптимизация раскроя (порезки) материала
Форум: "Прочее";Поиск по всему сайту: www.delphimaster.net;Текущий архив: 2006.11.26;Скачать: [xml.tar.bz2];Вниз
Линейная оптимизация раскроя (порезки) материала
PEAKTOP © (2006-11-04 12:49) [0]Доброе время суток ! Ув. Мастера, подскажите пожалуйста идеи линейной оптимизации раскроя материала.Внедряем ERP систему на FireBird v2.0, дошло вот до оптимизации заказов.Заказ - документ вроде расходной накладной, где несколько позиций из изделий. Изделие - сложный объект базы данных, который состоит из узлов и операционного времени сборки; узлы из: узлов, деталей и операционного времени сборки; детали из: деталей, заготовок и операционного времени сборки и т.д. Есть документ, "производственная программа" (или задание в цех на смену, если угодно), детальными позициями которого являются заказы. Требуется выбрать из всех заказов заготовки и сформировать задание на раскрой линейного материала. Есть хранимая процедура, которая по ID документа "производственная программа" возвращает список заготовок на смену в виде: ID_ZAG INTEGER, LENGTH_ NUMERIC(15,6) (мм)Материал линейный, длина исходного материала 10 000 мм (10 метров). Длина заготовок колеблеться строго от 200 до 2500 мм, обрезки выбрасываются. Надо сделать оптимальный раскрой, при котором отход будет минимальный. Проблема в том, что база "двусторонняя", т.е. работа с ней идет не только с клиентского ПО в административном офисе, но и через ВЭБ-интерфейс, т.е. оптимизацию надо будет делать только на SQL с помощью хранимых процедур.
Если кто сталкивался, подскажите пожалуйста идею, хотя бы с чего начать ? или хотя бы просто хотелось услышать свежие мысли по этому поводу.
PEAKTOP © (2006-11-04 13:03) [1]По условию задачи вполне допустимо ЗАКАЗЧИКОМ, что оптимизация - это сложная процедура, которая будет колбасится минут 5-10. Средние статистические данные: 3000 - 5000 заготовок в одной производственной программе.На текущий момент идея пока такая.Создать таблицы-регистры изCREATE TABLE RASKROY_VARIANTS( ID_DOC INTEGER, -- код документа производственной программы ID INTEGER -- Код варианта раскроя)CREATE TABLE RASKROY_PALKI( ID_VAR INTEGER NOT NULL FOREIGN KEY REFRENCES RASKROY_VARIANTS(ID) -- Код варианта раскроя ID INTEGER -- Код палки, которую будем резать на заготовки)CREATE TABLE RASKROY_PALKI_ZAG( ID_PALKA INTEGER NOT NULL FOREIGN KEY REFRENCES RASKROY_PALKI(ID) -- Код палки, которую будем резать на заготовки ID_ZAG INTEGER -- Код заготовки)В общем идея пока такая: перебрать в хранимой процедуре все варианты раскроя и заполнить регистры. А потом выбрать из всех вариантов тот, где потери будут минимальные.
Но сразу видно, что идея даст офигенный прирост базы, чего в общем-то не хотелось бы. Правда, вычислительные мощности сервака ЗАКАЗЧИКА позволяют сделать это (четыре двухядерных проца, 1ТБ ЖД). Но что-то подсказывает, что потом будут проблемы :)))
TUser © (2006-11-04 13:06) [2]Какая-то смесь всего - БД, ERP и оптимизация. Вопрос алгоритмический? Какая тогда разница, как там что-то в БД хранится? Или вопрос про БД и прочие технологии? Какое тогда отношение сюда имеет какая-то оптимизация?
Alexis © (2006-11-04 13:09) [3]Мастера, подскажите пожалуйста идеи линейной оптимизации раскроя материалаПосмотри в Интернете по ключевым словам 2D bin packing problemrectangle packing in two dimensionstwo dimensional bin packing problem NP-hard problems
PEAKTOP © (2006-11-04 13:11) [4]> Посмотри в Интернете по ключевым словам> 2D bin packing problemСкорее, это даже 1D.
Ученик чародея © (2006-11-04 13:32) [5]> PEAKTOP © (04.11.06 13:11) [4]> > > > Посмотри в Интернете по ключевым словам> > 2D bin packing problem> > Скорее, это даже 1D.
Тогда "жадный алгоритм"? Выбираем максимальный элемент не более куска ткани, потом максимальный который не более отреза и так до минимально возможного - самый простой алгоритм.
Если сложнее, то там уже эвристика.
PEAKTOP © (2006-11-04 13:43) [6]> Тогда "жадный алгоритм"? Выбираем максимальный элемент не > более куска ткани, потом максимальный который не более отреза > и так до минимально возможногоНу, в приципе, так и устроена хранимая процедура заполнения регистров.Проблема в том, что максимальная длина заготовки (2500) намного меньше исходной длины материала (10000), следовательно - очень много вариантов вставки туда остальных заготовок.Думаю, необходимо так называемо Лагранжево ослабление, когда "отсекаются" заведомо плохие решения и похожие решения. Скажем, отличие в потрях в вариантах раскроя на всей производственной программе на десятую процента не инетерсуют. А вот хотя бы процент - это уже интересует.Спасибо Alexis © (04.11.06 13:09) [3] за подсказку, где у буржуев почитать.
Alexis © (2006-11-04 15:04) [7]> PEAKTOP © (04.11.06 13:11) [4]
> Скорее, это даже 1D.Так что, то есть все детали (или узлы, как вы их там называете) по ширине равны?
PEAKTOP © (2006-11-04 15:27) [8]Ну, насколько я сейчас в состоянии понимать правльно задачу (с обеда уже 1б коньяка), то она сводится в оптимальном расположении линейных отрезков заготовок на линейных отрезках материала, т.е. 1D2D следовательно в оптимальном расположение фигур заготовок на листах материала.3D в оптимальном распложения заготовок памятников в кусках материала гранита. :))))
Форум: "Прочее";Поиск по всему сайту: www.delphimaster.net;Текущий архив: 2006.11.26;Скачать: [xml.tar.bz2];Наверх
Память: 0.75 MBВремя: 0.144 c
www.delphimaster.net
Практические приемы оптимизации раскроя с применением системы Базис. Глава 5. - Proderevo.net
При использовании плит определенного размера могут сформироваться карты раскроя, имеющие неудовлетворительное значение КИМ, или низкую технологичность. В том случае, если есть возможность закупать плиты других размеров, имеет смысл раскроить тот же список панелей, но при другом типоразмере плиты. Возможно, качество карт раскроя станет выше. Причем совсем необязательно, что на больших по площади плитах карты раскроя будут более качественными.
После выполнения раскроя обязательно надо проанализировать полученные карты. Во-первых, необходимо оценить размеры получившихся обрезков с точки зрения того, на какую величину размеры обрезков отличаются от ближайших по размеру панелей изделия. Может быть, есть возможность изменить размеры каких-нибудь деталей или всего изделия для получения более качественных карт раскроя.
Приведем простой пример. Пусть есть плита размером 2000х1000 мм. Ширина реза 0 мм. Необходимо раскроить 12 деталей размером 1001х501 мм. Очевидно, что на одну плиту помещается только одна панель, т.е для выполнения заказа необходимо 12 плит, а значение КИМ — около 25%. Но, если размеры панели уменьшить всего на 1 мм, то панелей с размерами 1000х500 мм на плите 2000х1000 мм разместится четыре штуки, а значение КИМ при этом будет равно 100%. При всей условности примера он наглядно иллюстрирует, как можно изменив размеры панелей на величину, которая, как правило, не критична для функциональности и эстетических показателей мебельных изделий, получить значительный выигрыш по всем основным показателям: стоимости, трудоемкости и времени изготовления изделия.
В том случае, когда размеры панелей изменить невозможно, можно попытаться варьировать толщиной облицовки. Рассмотрим пример. Панели в изделии облицованы материалом толщиной 0,5 мм со всех сторон, при этом облицовка нанесена с подрезанием контура панели. Это означает, что распиловочные размеры панелей уменьшаются на две толщины кромки по каждому измерению — длине и ширине, то есть на 1 мм. Формируем и анализируем карты раскроя. Допустим, они не устраивают по качеству. Возвращаемся к модели изделия в модулях БАЗИС-Мебельщик или БАЗИС-Шкаф и выполняем команду групповой замены облицовочного материала на новый толщиной 2,0 мм (или команду замену облицовочного материала на отдельных кромках панелей). В этом случае распиловочные размеры панели уменьшатся уже на 4 мм, но размеры готовой панели останутся прежними. Выполняем повторный раскрой и анализируем результаты. Вполне может оказаться, что значение КИМ возрастет очень резко, поскольку именно этих миллиметров и не хватало для получения качественного раскроя. Конечно, новый облицовочный материал стоит дороже, то есть при новом раскрое проигрываем в стоимости облицовочного материала, но экономим на стоимости ДСтП, что может «перекрыть» полученное удорожание. Получается парадоксальная ситуация: более дорогая мебель (за счет дорогой облицовки) оказывается в производстве более дешевой за счет экономии материала. Отметим, что все расчеты затрат на изделие выполняются автоматически и практически мгновенно в модуле БАЗИС-Смета.
Еще одно пояснение. В алгоритмах раскроя плитных материалов для мебельной промышленности заложена идеология раскроя гильотинными резами, то есть прямыми сквозными резами, разрезающими текущую полосу на две части. Одним из требований технологичности раскроя является точность размеров деталей с учетом допусков и посадок. Соответственно, алгоритмы формирования карт раскроя должны работать таким образом, чтобы получать панели с максимально точными размерами.
Рассмотрим фрагмент карты раскроя, приведенный на рис. 5.1.
Последнюю полосу, содержащую одиннадцать панелей с размерами 200х120 мм можно кроить разными способами. Допустим, что упоры устанавливаются с точностью ±0,5 мм, что является обычной точностью при распиловке панелей. Ширина реза - 5 мм. Выполняем раскрой. Вначале выполняем торцевание плиты, затем отрезаем полосу с этими панелями, то есть выполняем «горизонтальный» рез. После этого можно сделать рез на расстоянии 200*11+5*10 = 2250 мм для того, чтобы отпилить отход. Но этот размер может быть установлен на 0,5 мм меньше (точность установки упоров), то есть 2249,5 мм. Выполняем рез и устанавливаем размер по ширине на 120 мм, который реально из-за точности установки может оказаться равным 120-0,5=119,5 мм. Затем устанавливаем размер 200 мм, который реально может оказаться равным 200+0,5=200,5 мм. Отрезаем десять панелей, при этом размеры последней панели образуются автоматически. Измеряем ее длину и обнаруживаем, что она равна 194,5 мм, то есть на 5,5 мм меньше, чем нужно. Как это получилось, если все размеры были установлены с точностью 0,5 мм? Однако это легко доказать: 2249,5 - 200,5*10 - 5*10 = 194,5 мм. Реальный размер последней панели оказался равным 194,5х119,5 мм, а это уже неисправимый брак. Этот пример иллюстрирует, как влияет очередность раскроя на реальные размеры деталей.
Никогда не следует забывать о том, что технологический документ (в данном случае карта раскроя) - это инструкция для рабочего, заключающая в себе всю технологию изготовления и контрольные размеры, а не просто геометрический рисунок. На серьезном производстве рабочий не должен ничего складывать или прикидывать. Он должен точно следовать предписаниям в соответствии с документацией технологического процесса изготовления изделия.
Анализ оптимальности, технологичности и исполнимости карт раскроя
В данном разделе приведены примеры некоторых карт раскроя, полученных в различных программах, с анализом тех проблем и неудобств, которые могут возникнуть при их реализации на раскройном оборудовании. Это позволит читателю получить более полное представление о таких важных параметрах карт раскроя, как их технологичность и исполнимость. Ряд примеров карт раскроя и комментарии к ним с согласия автора взяты из статьи [27], часть — с профессионального мебельного форума htpp://mebelsoft.net.
Будем считать, что технологическая операция торцевания кромок плиты с двух сторон для обеспечения измерительной базы (кромки, от которой ведется отсчет) выполнена, поэтому она не рассматривается при описании последовательности действий по раскрою. Для упрощения анализа будем считать, что ширина реза равна нулю.
Проанализируем карту раскроя, показанную на рис. 5.2. С точки зрения КИМ данная карта вполне хорошая. Рассмотрим процесс ее исполнения на круглопильном станке: выполняем последовательно горизонтальный рез 1 и вертикальный рез 2.
Для раскроя оставшейся части листа единственными базами являются левая и верхняя кромки. Чтобы выполнить следующий рез, например, горизонтальный рез 3, необходимо сложить ширину полос (480+394+394 мм). Это означает, что на этом шаге ни один точный размер выставить невозможно — произошла потеря базы.
На первый взгляд кажется, что ничего страшного не произошло. Однако, где гарантия, что рабочий не ошибется и часть листа просто не уйдет в брак? Второй, более серьезный момент. Ни одна операция не может быть выполнена точно, поскольку в технике не существует размеров без допусков. Они обеспечиваются точностью станка, системой линеек и упоров, точностью измерительных приборов и т.д. На первом и втором шаге размер полосы выставлялся точно от базы, поэтому погрешность размеров минимальна. При отрезе полос на оставшейся части листа (горизонтальный рез 3) размер отрезаемой полосы будет выставлен с погрешностью 0,5 мм. Cоответственно, можно выставить размер 480+394+394=1268-0,5 мм=1267,5 мм.
Вертикальные резы 4, 5 и 6 выполняем с удовлетворительной точностью. Далее берем полосу 509х1267,5 мм и разрезаем ее горизонтальными резами. Для выполнения реза 7 при установке размера 480 мм с точностью 0,5 мм реально установили размер 480,5 мм, а при выполнении реза 8 при установке размера 394 мм с точностью 0,5 мм реально установили размер 394,5 мм.
Последняя деталь получилась с размером 392,5 мм, меньше номинала на 1,5 мм. Это для серьезного производства уже неисправимый брак, поскольку заданная точность исполнения 0,5 мм.
Для карты, показанной на рис. 5.3 даже для первого реза невозможно выставить точный размер. Первый рез (вертикальный рез 1) должен производиться на расстоянии 6*363 мм. Для дальнейшего раскроя установим размер 363 мм с точностью 0,5 мм, то есть первые пять полос будут отрезаться в размер 363,5 мм. Нетрудно подсчитать, что размер последней полосы будет равным 360 мм, а это уже неисправимый брак четырех деталей. Конечно, мы можем получить пять полос размером 362,5 мм, а последнюю полосу - размером 366 мм. Это уже исправимый брак, но для его исправления придется делать дополнительный рез.
Рассмотрим карту, приведенную на рис. 5.4. Как видно, укладка панелей на ней довольно плотная, но сама карта является неисполнимой, то есть выполнить раскрой в соответствии с ней просто невозможно. Рассмотрим возможную последовательность действий:
▼ выполнение вертикального реза 1 в размер 872 мм;▼ выполнение горизонтального реза 2 в размер 868 мм;▼ выполнение горизонтального реза 3 в размер 550+90 мм.
Дальше ни одного сквозного реза, например, горизонтальные резы 4, 6, или вертикальный рез 5, выполнить невозможно. Хорошо, если рабочий перед выполнением раскроя заметит это. В противном случае один или несколько листов материала уйдут в брак.
Карта, показанная на рис. 5.5, исполнима и имеет неплохое значение КИМ. Последовательность ее распила следующая: вертикальный рез 1, опиливание кромки, поворот, горизонтальный рез 2, опиливание кромки, поворот, вертикальный рез 3 и т.д. Другими словами, практически после каждого реза плиту придется поворачивать, а, значит, трудоемкость раскроя существенно возрастает.
Карту на рис. 5.6 на первый взгляд улучшить невозможно: и КИМ максимальный, и технологичность обеспечена. Рассмотрим последовательность распила. Вначале опиливаем правую сторону (вертикальный рез 1), а затем, развернув плиту на 90°, нарезаем полосы. Неудобство кроется в необходимости разворота практически целой плиты, поскольку, например, средний вес плиты ДСтП 2750х1830 мм толщиной 16 мм около 60 кг. Значительно легче было бы вначале нарезать полосы, а уж потом у каждой из них опилить кромку.
Рассмотрим последовательность распила карты, показанной на рис. 5.7. Выполняем вертикальный рез 1 в размер 2000 мм. Далее ее необходимо распилить на горизонтальные полосы, первая из которых имеет размер 1999х50 мм. Из-за наличия внутренних напряжений в плите, такую узкую и длинную полосу с большой вероятностью изогнет, и ее, возможно, придется списать в брак. Тоже самое может случиться и с крайней правой вертикальной полосой (вертикальный рез N) шириной 100 мм.
Карта раскроя, показанная на рис. 5.8, решает проблему возможного изгиба узкой полосы шириной 50 мм, расположив ее посередине листа. Такой эффект получен при помощи выбора метода сортировки, при котором узкие полосы располагаются внутри. Однако это существенно «ухудшило» технологичность остальных полос: попеременная установка упоров на уменьшение и увеличение размеров отрезаемых полос второго и выше уровней способствует понижению точности размеров. Это произошло в силу того, что выбранный метод сортировки действует на полосы всех уровней.
Решить эту проблему возможно включением опции Узкие полосы первого уровня располагаются внутри, который расположен на вкладке Критерии выбора в диалоге задания параметров раскроя. В этом случае, как видно из рис. 5.9, полоса шириной 50 мм по-прежнему располагается в середине плиты, но при этом в каждой получаемой полосе панели сортируются по установленному методу, например, от максимального размера к минимальному размеру.
Карту раскроя, показанную на рис. 5.10, вообще невозможно реализовать, поскольку в выделенном фрагменте отсутствуют прямые сквозные резы.
Таким образом, анализ карт раскроя, полученных автоматизированным способом в различных программах раскроя, показывает, что отсутствие учета технологических факторов оптимизации в лучшем случае приводит к получению трудоемких в реализации карт раскроя, а в худшем случае — к неисправимому браку. Традиционные алгоритмы оптимизации раскроя по максимальному значению КИМ по этим причинам далеко не всегда обеспечивают его.
Уменьшение трудоемкости раскроя
Задача уменьшения трудоемкости операции раскроя является актуальной для любого мебельного предприятия. Рассмотрим возможные варианты ее решения. Будем считать, что на предприятии используются пильные центры, на которых можно выполнять пакетный раскрой, и обычные круглопильные станки. Информацию для построения наименее трудоемкой стратегии раскроя будем получать из выдаваемой модулем БАЗИС-Раскрой статистической информации.
Допустим, выполнен раскрой некоторого задания, содержащего примерно пятьдесят типоразмеров панелей общим количеством не менее 150 штук, а количество панелей порядка 3000 штук. Вариант фрагмента статистических данных, формируемых модулем БАЗИС-Раскрой, приведен в табл. 5.1.
Качественные показатели выполненного раскроя достаточно хорошие. Поскольку используемое оборудование позволяет одновременно раскраивать до шести плит в пакете, в таблице приведены характеристики всех возможных вариантов пакетного раскроя. Рассмотрим их.
Общее количество используемых плит — 162 штуки. Если выполнять раскрой только на круглопильном станке по одной плите за цикл, то количество циклов будет равно количеству плит — 162 цикла.
При выполнении раскроя по две плиты в пакете количество циклов будет равно 84. При переходе к раскрою по три плиты, количество циклов уменьшается незначительно, до 83. Другие характеристики тоже улучшаются, но незначительно. Зато при переходе к раскрою по четыре плиты все значения резко улучшаются, почти в два раза. Например, количество циклов равно уже 45.
Дальнейшее увеличение количества плит в пакете совершенно не изменяет характеристики раскроя. На первый взгляд это не логично. Тем не менее, объяснение достаточно простое: в данном варианте набор панелей таков, что для его раскроя невозможно сформировать пакеты по пять плит. Оптимальным вариантом будет раскрой по четыре плиты в пакете.
Такое резкое улучшение характеристик пакетного раскроя происходит далеко не всегда. Рассмотрим еще один пример, информация по которому приведена в табл. 5.2. Резкое уменьшение количества циклов произошло только при переходе к пакетному раскрою, а в дальнейшем оно носит плавный характер.
Поясним, как рассчитывается количество циклов. Пусть надо раскроить по некоторой карте раскроя 12 плит. При четырех плитах в пакете необходимо три цикла (12:4=3), а при пяти плитах —два пакета по пять плит и один пакет из двух плит, то есть те же самые три цикла.
От количества циклов зависит общая длина резов, а от нее — износ пилы. Пиление тупым инструментом увеличивает потребление электроэнергии, ухудшает качества продукции и может служить причиной поломки пил. Вернемся к первому примеру. При раскрое по одной плите длина резов равна 4654,266 м, а при раскрое по четыре плиты она меньше — 1302,112 м. С другой стороны общая толщина «прорезаемой» плиты в первом случае меньше (одна плита), а во втором — больше (четыре плиты). Следовательно, износ пилы будет практически одинаковым.
Однако это не совсем так. Известно, что износ режущего инструмента зависит от множества факторов: скорости подачи, технического состояния станка и т.д., в том числе, от количества ударов зубьев о поверхность материала и количества распиленного материала. При прочих равных условиях на удар приходится примерно одна треть износа, а собственно на пиление — примерно две трети. Легко догадаться, что количество ударов при раскрое по одной плите будет значительно большим, что приведет к большему износу пилы. Вывод: раскрой предпочтительнее вести пакетами с максимально возможным количеством плит. Это не только экономит время и уменьшает трудоемкость, но и продлевает срок службы режущего инструмента.
Практика штабелирования панелей
Как отмечалось выше, решение задачи оптимального раскроя материалов имеет не только экономические и технологические, но и организационные аспекты, позволяющие повысить производительность работы, как самого раскройного участка, так и многих связанных с ним участков. Проанализируем карты раскроя некоторого заказа, показанные на рис. 5.11 и рис. 5.12.
Общая информация по раскрою (в модуле БАЗИС-Раскрой она выводится перед первой картой) приведена в табл. 5.3.
С точки зрения значения КИМ и технологичности их можно считать оптимальными. Рассмотрим последовательность выполнения раскроя. Карты условно будем нумеровать слева направо и сверху вниз вначале на рис. 5.11 с продолжением на рис. 5.12. Аналогичным образом нумеруем карты на рис. 5.13 с продолжением на рис. 5.14.
После распила первой карты на участке образуются штабели из 40 панелей 800х350 мм (позиция 3), 48 панелей размером 600х290 мм (позиция 1) и 192 панелей размером 500х146 мм (позиция 2). Последние панели можно отправлять на дальнейшую обработку, поскольку они выпилены в полном объеме. Остальные панели остаются на участке. После распила второй карты штабель панелей 800х350 мм (позиция 3) увеличивается еще на 30 панелей, но он попрежнему остается на участке. Только выполнив распил четвертой карты, можно передать панели 800х350 мм (позиция 3) на последующую обработку, но панели 600х290 мм (позиция 1) остаются на участке. Кроме того, появляется штабель панелей 480х352 мм (позиция 4) в количестве 20 штук. Только после распила третьей карты на участке остается единственный штабель панелей 480х352 мм (позиция 4). Таким образом, на раскройном участке во время выполнения заказа постоянно находится значительное количество штабелей панелей разных типоразмеров, которые ждут отправки на дальнейшую обработку. И это, как показывает практика, далеко не самый крупный заказ. Подобная ситуация чревата как минимум двумя отрицательными последствиями:
▼ при близких значениях размеров панелей в разных штабелях велика вероятность субъективной ошибки рабочего, который может просто перепутать панели и положить не в тот штабель;▼ простой других участков предприятия (облицовочный, фрезерно-присадочный и т.д.) в ожидании панелей.
Выполним раскрой того же задания при неизменных настройках критериев и параметров, но с учетом технологии оптимального штабелирования. Для этого в диалоге настройки параметрах раскроя на вкладке Критерии выбора установим режим штабелирования по площади. Результат показан на рис. 5.13 и 5.14, а общая информация по результатам нового раскроя приведена в табл. 5.4.
Проанализируем результаты раскроя. Значение КИМ уменьшилось на 5,48%, но КИМ с учетом обрезков практически не изменился. Увеличились количество и площадь обрезков, а также количество карт раскроя — на две штуки. Для распила заказа потребовалась одна дополнительная плита материала. Количество и общая длина резов практически не изменились.
В качестве положительного момента отметим двукратное уменьшение количества установок размеров. Рассмотрим последовательность распила листов. После распила первой карты на участке формируется единственный штабель панелей 800х350 мм (позиция 3), который после распила четвертой карты может быть отправлен на следующие этапы обработки. Вместо него образуется штабель панелей 600х290 мм (позиция 1). Последовательно распиливаем шестую и вторую карты, после чего отправляем эти панели дальше. На участке по+прежнему один штабель панелей — теперь размером 480х352 мм (позиция 4). После распиливания седьмой карты они также отправляются на последующие этапы обработки. Последняя (третья) карта содержит только панели 500х146 мм (позиция 2). Таким образом, в любой момент времени на раскройном участке находится не более двух штабелей разных по размеру панелей, один из которых уже полностью подготовлен к передаче на другие участки.
Как видим, оба варианта раскроя имеют и свои достоинства, и свои недостатки. Выбор, как всегда, определяется конкретной производственной ситуацией. Главное в том, что технология оптимального штабелирования дает специалистам мебельного производства дополнительные возможности для организации равномерной загрузки оборудования всех технологических участков. Применять ее или нет — зависит от многих факторов, основной из которых — умение проанализировать и оценить все издержки, возникающие при реализации того или иного заказа.
proderevo.net
Оптимизация линейного раскроя, программа раскроя линейных материалов
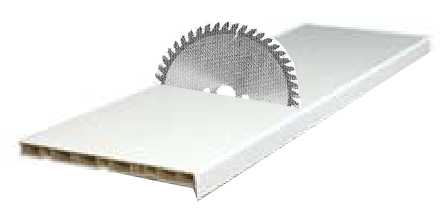
Назначение программы:
Оптимизация раскроя длинномерных материалов: подоконника, профиля, трубы, бруса/доски, рулонных материалов и др.Основные преимущества программы:
Видеоматериалы
Варианты приобретения модуля
- Возможность обращаться к нашим специалистам
- Доступ ко всем обновлениям модуля Раскроя
- работы по установке и внедрению
- полгода технической поддержки.
Расчет экономической эффективности на примере материала подоконник (ПДК)
Например, вы закупили 500 м2 ПДК на сумму 240 000 руб. (стоимость м2 ПДК с учетом доставки 480 руб.). Мы сокращаем обрезь на 5% или на 12 000 рублей в денежном выражении. За год эта сумма составит 144 000 руб! Средний срок окупаемости программы чуть более 2-х месяцев! Программа же даёт больший эффект, чем 5%! Думайте, считайте, принимайте решение!
prostor35.ru
4.Оптимизация раскроя древесностружечных плит на заготовки. Оптимизация процессов деревообработки на моделях линейного и нелинейного программирования
Похожие главы из других работ:
Проект цеха по производству древесностружечных плит
4. Пооперационный расчет перерабатываемого материала в производстве древесностружечных плит
Для определения количества единиц технологического оборудования необходимо знать, сколько материала перерабатывается на каждой технологической операции...
Проект цеха по производству трехслойных древесностружечных плит
1 ВЫБОР И ОБОСНОВАНИЕ ТЕХНОЛОГИЧЕСКОЙ СХЕМЫ ПРОИЗВОДСТВА ДРЕВЕСНОСТРУЖЕЧНЫХ ПЛИТ
...
Проект цеха по производству трехслойных древесностружечных плит
1.1 Общие сведения о производстве древесностружечных плит
...
Проект цеха по производству трехслойных древесностружечных плит
1.1.1 Классификация и виды древесностружечных плит
Древесностружечные плиты изготовляют из древесины (иногда недревес-ных частиц) различными методами и для различных целей (потребителей). Этим объясняется большое разнообразие плит. Чаще всего их классифицируют по следующим основным признакам...
Проект цеха по производству трехслойных древесностружечных плит
1.2 Выбор способа производства древесностружечных плит
...
Проект цеха производства древесностружечных плит
7. Описание технологического процесса производства древесностружечных плит
Организация производства однослойной ДСтП предусматривает создание одного потоков подготовки стружки. Сырьем для производства ДСтП в данном случае служит технологическое сырье...
Разработка конструкции и технологического процесса производства кровати в условиях ОАО "Ирбитская мебельная фабрика"
3.2 Раскрой плит на заготовки изделия
Раскрой ДСтП и ДВП производится по заранее разработанным картам раскроя. Карта раскроя представляет собой эскиз плит раскроя, вычерченный в масштабе 1:20...
Разработка технологического процесса изготовления детали методом холодной листовой штамповки
2.3 Выбор варианта раскроя
Раскрой листового материала должен обеспечить минимальный расход материала, высокую производительность штампа, качество штампуемых деталей и стойкость штампа...
Разработка технологического процесса изготовления трёхслойной втулки
5. Карта раскроя
а) б) Рисунок 5 - Карта раскроя: а - Для АМг6 и МА20, б - Для АД1 После получения основных материалов в заготовительном отделении цеха металлы подвергают предварительной обработке: правке...
Расчет технологического процесса производства древесностружечных плит
Описание технологического процесса производства древесностружечных плит
Технологическая щепа и отходы лесопиления поступают в цех, где происходит измельчение в рубительной машине МРНП- 30 в технологическую щепу. Полученную на рубительных машинах щепу сортируют, так как наряду с нормальной щепой...
Современные материалы меховой промышленности. Новые технологии производства и использования пушных полуфабрикатов. Шкурка соболя
5.1 Способы раскроя шкурок
Способы раскроя шкурок разнообразны. Их можно разделить на простые (обычные типовые приемы, которые повторяются при раскрое большинства шкурок) и сложные, применяемые специально для изменения формы шкурки, состояния ее волосяного покрова...
Составление плана раскроя пиловочника сырья
9. Схема раскроя сырья
При составлении схемы раскроя пиловочного сырья из спецификации пиломатериалов выделяют доски ведущих размеров, которые составляют обычно 70…75 % от общего объема пиломатериалов. К ним относятся все доски толщиной 32 мм и более...
Технологии и оборудования композиционных материалов и древесных плит
2. Основные свойства древесностружечных плит
Среди основных свойств ДСП следует выделить следующие: Плотность -- 0,5--1,0 г/смі, Плотность -- скалярная физическая величина, определяемая как отношение массы тела к занимаемому этим телом объёму или площади Набухание в воде -- 5--30 %...
Технологический процесс механической обработки шестерни ведущей конечной передачи
3. Оптимизация метода получения заготовки
Метод получения заготовок деталей машин определяется назначением и конструкцией детали, материалом, техническими требованиями, объёмом выпуска продукции и типом производства, а также экономичностью изготовления...
Технология и оборудование древесных плит и пластиков
1.2 Санитарно-гигиенические свойства древесностружечных плит
В настоящее время в нашей стране и за рубежом большое внимание уделяется санитарно-гигиеническим свойствам ДСтП. Древесностружечные плиты выделяют в окружающую среду формальдегид. Принимая во внимание высокую токсичность формальдегида...
prod.bobrodobro.ru
Оптимизация раскроя материала
Оптимизация раскроя материала - очень узкая тема с точки зрения общего производственного цикла, в то же время она имеет серьезную проблематику и различные варианты реализации. Вероятнее всего, Вы уже занимаетесь каким-либо производством или тесно с ним связаны, раз заглянули на эту страничку. На сегодняшний день на рынке существуют разные программы раскроя: простые и сложные, обособленные и в составе крупного программного комплекса. Наша компания специализируется на решениях для небольших производств, где оптимизация раскроя материала является одним из приоритетных направлений. Мы постарались структурировать те виды производств, для которых будет актуальна наша разработка, и обратить внимание на основные отличия этого решения от аналогов.
Отличия нашей разработки оптимизации распила материала от других:
1. Программа реализована на платформе 1С.
Подойдет любая типовая конфигурация на базе 1С 8: управление торговлей, управление небольшой фирмой, бухгалтерия, УПП и другие. Для одних компаний это может оказаться минусом, для других же наоборот существенным плюсом. Что же даёт реализация на 1С? - самое главное, что Вашим сотрудникам не придется дважды вбивать информацию о заказе; - процесс занесения заказа от клиента останется прежним; - никак не мешает типовым обновлениям.2. Программа работает в динамике.
Мы все за то, чтобы работа проходила быстро и без промедления, но тут вступает в дело пресловутый человеческий фактор. Рассмотрим типовой пример работы: менеджер вбивает размеры, запускает программу раскроя, делает распечатку карты раскроя, отдает ее пильщику, ответственный сотрудник производит распил. В этот момент он может столкнуться с различными ситуациями: брак, отсутствие материала, собственная ошибка. Дальнейшие действия - согласовать новую карту раскроя у менеджера или "кроить на глаз". В случае работы "в динамике" - все эти действия можно сделать прямо по ходу работы.3. Умеет меняться.
Все знают про способность 1С подстраиваться под клиента. Хотите "кнопочку вот тут" - это возможно! Мы поможем сделать доработку интерфейса специально под Ваши потребности.4. Работает по Вашим настройкам.
Решение построено таким образом, что Вы можете указать множество различных настроек, например: - допустимая обрезь; - минимально допустимые размеры; - популярные размеры; - другие индивидуальные характеристики.5. Полный учет материала.
С нашей программой у Вас есть возможность вести учет как в общих единицах измерения (квадратные или погонные метры), так и в штуках по каждому куску. Благодаря этому менеджер по закупу "под лупой" может рассмотреть все "свои квадратные метры" или куски материала и понять, чего в данный момент действительно не хватает. Кроме того, точный учет позволяет исключить любую возможность хищения.6. Программа создана на базе реального производства.
Большим преимуществом является то, что группа разработчиков территориально находиться на реальной производственной базе, где все наработки проходят первую практическую обкатку. Это не выдуманные интерфейсы и алгоритмы, это то, что требуется производству в настоящее время. Программа успешно внедрена и работает уже более чем в 10 городах по всей России.Виды оптимизаций раскроя материала:
1. Программа оптимизации линейного раскроя.
С точки зрения математики - это самая простая оптимизация. Ее можно сравнить с бытовым примером: нарезка колбасы в магазине. А если коснуться производств, то в эту группу можно отнести следующие типы раскроя: подоконников, бревен, трубы, профиля и др.2. Программа оптимизации листового раскроя.
Данный вид оптимизации намного более сложен, нежели линейный раскрой. Касаясь примера с колбасой, это именно тот момент, когда Вы режете кусок на ломтики...А если серьезно, применяется данная разработка в следующих типах производств: - раскрой стекла; - раскрой ДСП, ЛДСП; - раскрой сэндвич-панелей; - раскрой металла; - множество других материалов.
3. Оптимизация раскроя двухкапиносных ПДК.
Для многих сфер деятельности данный вид оптимизации будет совершенно непонятен, однако, для предприятий, которые занимаются распилом подоконников: Crystallit, Danke, Meller, проблема раскроя данного вида материала является одной из ключевых. У нас есть специализированное решение для данного случая. Подробнееprostor35.ru
Оптимизация раскроя
Для получения оптимального, с точки зрения вашего производства, раскроя в bCUT нужно настроить алгоритм раскладки, а дальше — действовать линейно или, применяя те или иные приёмы оптимизации улучшать раскладку каждого отдельного материала. Выбор тогой или иного подхода зависит от приоритетов производства. Приемы оптимизации можно комбинировать и, конечно, можно разработать свои приёмы работы. Стоит отметить, что пока программа выполняет раскладку для одних материалов, можно вводить данные для другого.
Настройка алгоритма
В первую очередь, оптимизацию раскроя обеспечивает алгоритм раскладки заготовок. Алгоритм настраиваемый и обеспечивает несколько методов с различными приоритетами. Настройки находятся на диалоге «Оптимизация», который вызывают в зоне раскроя главного окна программы. Выбор тех или иных настроек зависит от масштабов производства и оборудования.
Например:
- Максимальная экономия материала получится когда метод Экономичный , флаг Полосовой раскрой снят и направление первого реза Авто.
- Наименьшую трудоемкость для форматного раскройного станка будет если метод Длинные резы, флаг Полосовой раскрой установлен и направление первого реза Вдоль.
- Наименьшую трудоемкость для станка с программным управлением, при возможности раскроя пакета листов получится при методе Технологичный, снятом флаге Полосовой раскрой и направлении первого реза Авто.
На результаты раскроя также влияет станок и режим реза станка, поскольку в разных режимах может быть разная ширина пила. Станок и режим для него задают в банке данных, а во время работы выбирают в зоне раскроя. Обратите на это особое внимание, если на предприятии имеется несколько станков или на станке меняют пилы.
Команды для оптимизации
Приемы оптимизации базируются на нескольких командах. Чтобы эффективно оптимизировать раскрой нужно изучить их и использовать:
- Различные варианты команды «Раскроить». Они позволяют докраивать оставшиеся детали и перекраивать имеющиеся карты с новыми настройками.
- Способы удалить отдельные карты или все сразу. Они позволят удалить неудовлетворительные результаты раскроя, чтобы, затем, выполнить раскладку с другими настройками.
- «Перенос деталей», ограничение количества листов и перенос не раскроенных деталей на новый материал. Это позволит выполнить раскладку части деталей на листах другого размера.
- Ручное редактирование отдельных карт. Позволяет отредактировать результаты раскроя - выполнить раскладку деталей вручную.
Знание команд позволит придумать методики работы наиболее эффективные для своего предприятия.
Просмотр результатов по материалу
Сводные сведения о результатах раскроя по каждому материалу приведены в рамке материал зоны раскроя. Чтобы просмотреть сведения по всем материалам, просто переключайтесь по всем закладкам зоны деталей.
Просмотр результатов по картам
Программа выводит на экран графическое изображение карты и сводные сведения о ней.
Перебирать карты удобно кнопками и панели карт раскроя. Также можно изменять номер просматриваемой карты в рамке «Карта». Кнопками или просто водить номер с клавиатуры.
Удобно смотреть карту, когда её графическое изображение большого размера. Двойной щелчок мыши на изображении карты раскроя «распахивает» её, а повторный двойной щелчок восстанавливает размер. Можно использовать кнопки: «Распахнуть» / «Восстановить» панели карты раскроя, а также «Только карты» и «Обе» панели инструментов главного окна.
Совет. Если сведений о детали на изображении карты не хватает, например, виден только номер детали, а её размеров нет, то просто щёлкните мышкой по этой детали на карте. Список в таблице деталей прокрутится и остановится именно на этой детали, по которой щёлкнули. Можно будет уточнить её размеры, кромление, название и т.д. — все, что есть про неё в таблице.
Приёмы оптимизации
Далее, приведены несколько приёмов по оптимизации раскроя.
Линейная оптимизация
Когда нужно быстро получить результат, быстро выяснить расход материала или отправить заказ в работу, то действуют в следующем порядке:
- Вводят в таблицу или импортируют сведения о деталях.
- Устанавливают для каждого материала принятые на предприятии настройки алгоритма раскладки.
- Нажимают кнопку Раскроить все на панели задания главного окна и ждут результата
Всё. Раскрой закончен. Задание утверждают и переходят к следующему.
Подбор вариантов
Когда есть немного времени, чтобы потратить его на уменьшение расхода материала или снижения трудоемкости, то можно последовательно подбирать настройки алгоритма раскладки для каждого материала.
- Вводят в таблицу или импортируют сведения о деталях.
- Переключаются на один из материалов и устанавливают для него обычные настройки алгоритма раскладки.
- Выполняют раскладку кнопкой Раскроить, которая находится в зоне раскроя . При этом, раскрой выполняется только для выбранного материала.
- Смотрят на результаты раскроя, просматривают карты кнопками и панели карт раскроя.
- Устанавливают другие настройки оптимизации и перекраивают материал. Смотрят на результаты и сравнивают их с предыдущими.
Проделывают п.5 с различными вариантами настроем и окончательно раскраивают с наилучшими. При приобретении опыта работы с программой, как правило, выявляется две-три настройки, которые дают результаты, которые имеет смысл проверять.
Комбинация вариантов
Если позволяет время, то можно разложить детали комбинируя несколько настроек алгоритмов, используя лучшие результаты раскладки от каждой. При этом качество карты оценивает человек. Можно просто на глаз, можно по статистике карты.
Примерный порядок следующий:
- Устанавливают настройки алгоритма.
- Выполняют раскладку командой «раскроить неразмещенные детали» (кнопка в рамке Раскрой»)
- Просматривают карты и удаляют те, которые не нравятся командой «Удалить карту».
Действия повторяют до получения результата. С приобретением опыта, число проходов сокращается.
www.propro.ru