Управление запасами деталей на складах запасных частей. Оптимизация склада запасных частей
Тема 4.2. Организация хранения запасных частей и управление их запасами
Вопросы темы:
1. Определение номенклатуры и объемов хранения деталей на складах
2. Управление запасами на складах
3. Организация складского хозяйства и учета расхода запасных частей и материалов на предприятиях
4.2.1. Определение номенклатуры и объемов хранения деталей на складах
Очевидно, что хранить все выпускаемые в качестве запасных частей детали у дилера, и тем более на АТП, не рационально. Это приведет к значительному увеличению запасов, росту складских площадей и, самое главное, к неэффективному использованию запасов - большая их часть останется лежать "мертвым грузом". С другой стороны, поскольку выход деталей из строя носит случайный характер, то теоретически в любой момент может понадобиться любая из запасных частей.
Рис. 20.1. Определение оптимального размера и момента заказа запасных частей 1 - затраты на закупку, 2 - на хранение, 3 – суммарные
Изучение отечественного и зарубежного опыта организации МТО показало что решается эта сложная задача путем применения складской формы продвижения продукции от изготовителей к потребителям, заключающейся в централизации различных по номенклатуре и объему запасов на складах различных уровней.
По мере необходимости детали нужной номенклатуры со склада высшей уровня передаются на склад низшего уровня, поддерживая тем самым необходимы для удовлетворения спроса запас на каждом из них.
Определение номенклатуры запасных частей и объемов хранения на складах разного уровня осуществляется различными методами. В основу наиболее распространенного положено деление всей номенклатуры запасных частей для каждой модели автомобиля по частоте спроса на группы А, В и С (см. рис. 3.6).
Первая группа (детали высокого спроса) включает около 20% общей номенклатуры запасных частей. Ими удовлетворяется около 85% заказов потребителей, а стоимость составляет 65% стоимости всей потребляемой номенклатуры. Именно эти детали чаще всего выходят из строя, и заменой их у дилеров, на СТО и АТП устраняют большую часть неисправностей и отказов.
Вторая группа (детали среднего спроса) включает около 20% общей номенклатуры, но ими удовлетворяется только 10% спроса на запасные части, а стоимость составляет около 30%.
Третья группа (детали редкого спроса) включает более 60% общей номенклатуры. Ими удовлетворяется 5% спроса на запасные части, стоимость составляет около 5%.
Детали, относящиеся к той или иной группе, определяют на основе анализ: продаж за предыдущие периоды и перераспределяют с учетом текущей информации о спросе и движении запасных частей в системе.
Для определения объема хранения каждой детали и момента заказа очередной партии для пополнения запаса применяются различные методы - от простейших таблиц спроса до сложных экономико-математических расчетов. С их помощью определяют размер заказа и количество заказов в году, при которых суммарные затраты на закупку и хранение одной детали минимальны (рис. 20.1).
Если одновременно заказать всю годовую потребность в деталях, то затрать на закупку (подготовка заказа, получение и доставка, контроль и др.) будут т единицу заказа минимальными, а затраты, связанные с хранением, - максимальными. Например, при годовой потребности в 300 деталей и единовременном их заказе запас в течение года будет изменяться от максимального, равного 300, до минимального, равного нулю. При этом расходы на хранение будут определяться средним по году уровнем запаса, равным 150 деталям.
Если размер заказа сократить в 10 раз (до 30 деталей), то расходы на хранение будут определяться новым средним уровнем запаса, равным 15 деталям, т.е. сократятся, а затраты на закупку увеличатся (вместо одного - 10 заказов).
Оптимальный размер заказа Q по критерию минимизации совокупных затрат на хранение запаса и повторение заказа рассчитывается по формуле Вильсона:
где А - затраты на закупку единицы заказа, руб.; S - годовой расход данной детали, шт.; С - затраты на хранение единицы заказа, руб.
4.2.2. Управление запасами на складах
Формирование и контроль запасов - основные составляющие, от которых зависит своевременное устранение дефицита или затоваривания. Они предусматривают поддержание такого соотношения деталей частого и нерегулярного спроса, которое обеспечивает высокую оборачиваемость запасов, при удовлетворительном обеспечении покупателей, и оптимальные расходы на их содержание.
Эта цель достигается решением следующих задач:
• учет текущего уровня запаса на складах различных уровней;
• определение размера минимального (страхового) уровня запаса;
• расчет размера заказа;
• определение интервала времени между заказами.
Для удовлетворения спроса в любой момент, независимо от задержек в поставках или от скачка заказов, применяют систему, предусматривающую наличие страхового запаса (рис. 20.2). Из графика видно, что наличие страхового запаса, например в 50 деталей, позволило обеспечить продажи в одном случае в период запаздывания поставки, а в другом - при непредвиденном увеличении спроса выше расчетного.
Рис. 20.2. Упрощенная схема движения запасов на складе
1 - страховой, 2 - средний текущий, 3 - максимальный запас
Установление рационального уровня страховых запасов крайне важно, так как отклонения от оптимума приводят к снижению сбыта и потере клиентуры либо к дополнительным расходам по содержанию лишних запасов.
Средний текущий запас также является важным показателем, так как определяет среднюю величину средств, вложенных в запасы и среднюю стоимость их содержания.
Оптимальный размер запасов каждой детали определяется с учетом разделения номенклатуры по частоте спроса. Для деталей группы А в общий размер запаса включается наибольший страховой запас, чем обеспечивается покрытие любых скачков спроса. Для деталей постоянного спроса (группа В) в размер запаса включается средний страховой запас, а для деталей группы С - низкий или нулевой страховой запас. Периодичность контроля наличных запасов на складе также разная: группы А - частый контроль, например раз в неделю; группы В - раз в месяц; группы С - раз в квартал.
Для управления запасами на складах запасных частей с целью обеспечения оптимального их уровня применяют два метода; метод с постоянной периодичностью поставок (рис. 20.3,а) и метод с постоянным объемом поставок (рис, 20.3,б).
Сущность 1-го метода: запасные части заказываются и поступают на региональный склад или склад дилера через равные промежутки времени (t1 = t2 = t3 ), а регулирование размера запаса осуществляется путем изменения объема партии поставки (W1 ≠ W2 ≠ W3 ). Поставка осуществляется несколько раз в месяц (например, 10, 20 и 30 числа), а заказ на склад высшего уровня направляется за несколько дней до поставки (например, 8, 18 и 28 числа) (τ1 = τ2 = τ3)- Управление складскими запасами заключается в том, что в момент заказа (ТЗ) по фактическим данным о наличии деталей данного наименования на складе устанавливается вероятный размер их запаса Звер.1 в момент поставки и заказывается партия, равная разности между максимальным запасом Зmax и вероятным Звер.1= (Зmax - Звер.1). Тем самым обеспечивается гарантированное наличие на складе требуемого количества деталей, достаточного для полного удовлетворения спроса.
Достоинство этого метода в простоте. Однако он применяется только в случае, когда запасные части расходуются достаточно равномерно.
Сущность 2-го метода заключается в фиксированном размере заказа. Поступление запасных частей происходит равными, заранее определенными партиями (W1 = W2 =W3), но интервалы между поставками различны (t1 ≠ t2 ≠ t3). Очередной заказ производится, когда запас снижается до определенного, так называемого порогового, уровня. Он рассчитывается таким образом, чтобы поступление очередной партии произошло в момент, когда фактический запас деталей на складе достигнет Зmin.
При этом методе достигается поступление партий поставок одинакового размера, снижаются затраты на доставку и содержание запаса, но требуется систематический и непрерывный контроль запасов.
4.2.3. Организация складского хозяйства и учета расхода запасных частей и материалов на предприятиях
Номенклатура материальных ценностей, хранящихся на среднем АТП, может достигать 3-4 тыс. наименований и подразделяется на
• агрегаты, узлы и запасные части,
• эксплуатационные материалы,
• материалы общего назначения,
• малоценные и быстроизнашивающиеся материалы.
Для облегчения учета всю хранимую номенклатуру кодируют с помощью многоразрядного логического кода. Для этого агрегаты, узлы и детали для ТО и ТР, по аналогии с кодированием, используемым в каталогах запасных частей, делят на группы и подгруппы. Номер группы определяет агрегат, номер подгруппы - узел, а порядковый номер подгруппы - деталь.
Материалы общего назначения обычно разбивают на 10 групп: металлы, инструменты и приспособления, электротехнические устройства и материалы, хозяйственные товары, химикаты, ремонтно-строительные материалы, вспомогательные материалы, спецодежда, станки и прочие материалы. Каждая из групп также делится на 10 подгрупп по признаку однородности материалов и получает свой второй номенклатурный номер. Каждую подгруппу, в свою очередь, подразделяют на 10 частей, из которых каждая получает свой номенклатурный номер и т.д. Таким образом, каждый материал, хранящийся на складе, имеет определенный трех- или четырехзначный номер, который полностью его характеризует.
Изделия и материалы располагают на специальных стеллажах, позволяющих быстро отыскивать то, что необходимо для производства.
Запасные части обычно хранят на многоярусных стеллажах. Агрегаты автомобиля устанавливают на специальных подставках.
Металлы в прутках хранят на многоярусных стеллажах в горизонтальном положении. Листовые металлы - в кипах или в вертикальном положении в клетках стеллажей.
Легковоспламеняющиеся материалы и кислоты хранят в огнестойком изолированном помещении. Бутыли с кислотой располагают отдельно, в отгороженном помещении в специальной мягкой таре.
Моторные, трансмиссионные и другие смазочные материалы хранят на специальных складах. На этих же складах хранят технические жидкости и пластичные смазки.
Монтажный, режущий, контрольно-измерительный инструмент и приспособления хранят в инструментально-раздаточной кладовой в многоярусных клеточных стеллажах, с тем чтобы каждый номенклатурный номер имел свою отдельную ячейку.
В такелажной кладовой хранят и выдают погрузочный инвентарь (брезенты, веревки, цепи и т.п.), а также выполняют его просушку, ремонт, учет и пополнение. Для хранения такелажа применяют полочные многоярусные стеллажи.
Склад утиля оборудуется специальной тарой. Он принимает от производства негодное имущество и отработанные материалы и сдает их соответствующим организациям для вторичного использования или утилизации.
Шины и другие резинотехнические изделия и материалы хранят на специальных складах, желательно в подвальных или полуподвальных помещениях, температура в которых не должна превышать +20°С, а относительная влажность 50-60%. Кроме того, помещения для хранения шин должны быть защищены от дневного света. На складах для хранения резиновых материалов не допускается хранение материалов, отрицательно действующих на резину: керосина, бензина и т.п.
Покрышки хранятся на деревянных или металлических стеллажах в вертикальном положении и располагаются на расстоянии не менее 1 м от отопительных приборов. При долгосрочном хранении их необходимо периодически (раз в квартал) поворачивать, меняя точку опоры. Складывать покрышки в штабеля, укладывая друг на друга, не допускается. Камеры хранятся на специальных вешалках с полукруглой полкой слегка накачанными, припудренными тальком или вложенными в новые покрышки. Периодически (через 1-2 мес.) камеры также поворачивают, меняя точки опоры.
Сырую резину, применяемую при ремонте, хранят в рулонах на полках стеллажей. Клей для ремонта - в закрытой стеклянной посуде.
Таким образом, на АТП должны функционировать основной материальный склад (запасные части, материалы, имущество), специализированный склад для приема, хранения и выдачи ТСМ; склад утиля. Основной склад должен иметь в своем составе секции для шин, лакокрасочных материалов и химикатов.
Учет материальных ценностей, поступающих на склад, а также выданных производству и возвращенных обратно, осуществляется с использованием типовой первичной документации, утвержденной Министерством финансов РФ: приходного ордера (формы М-3 и М-4), акта о приемке материалов (формы М-10 и М-11), накладной на внутреннее перемещение материалов (формы М-12 и М-13), накладной на отпуск материалов "на сторону" (формы М-14 и М-15), карточки складского учета (форма М-17), ведомости учета остатков материалов на складе (форма М-20), справки об отклонениях фактического остатка от установленных норм запаса (форма М-34).
При поступлении на склад новых запасных частей и материалов оформляется приходный ордер. Поступление материалов от подразделений АТП (сдача запасных частей собственного изготовления, возвращение неиспользованных материалов, сдача на склад отходов и т.п.) оформляется накладной в двух экземплярах. Таким же образом оформляется перемещение материалов со склада на склад.
Запасные части и материалы отпускают производству на основании требования, подписанного руководителем ИТС. Для оперативного контроля за использованием установленного лимита вносится соответствующая запись в карту учета использования лимита. На средних и крупных АТП широко используется отпуск материалов производству по лимитно-заборным картам (формы М-8 и М-9), оформляемым срокам на 2 мес. Один ее экземпляр находится на складе, другой - у потребителя. Отпуск материалов "на сторону" оформляется специальной накладной, которая выписывается в трех экземплярах.
Общий учет материальных ценностей на АТП обычно ведется по сальдовому методу: на складах осуществляется количественный учет, а в бухгалтерии - стоимостный. Данные первичных документов по приходу и расходу на складе заносятся в карточки складского учета, в которых указывается остаток запасных частей, материалов и быстроизнашивающихся изделий в натуральном выражении. В бухгалтерии на основе этих же документов составляются оборотные ведомости. В конце каждого месяца остатки с карточек складского учета переносятся в сальдовые книги, подсчитывается их общая стоимость, и итоги сравниваются с оборотными ведомостями.
При поступлении материальных ценностей их оценка и учет производятся по фактической себестоимости приобретения (стоимость, уплаченная поставщику, плюс транспортно-заготовительные расходы). При отпуске ценностей производству в документацию вносится та же оценка.
Контрльные вопросы темы:
1. Объясните определение номенклатуры и объемов хранения запчастей по частоте спроса.
2.Объясните определение оптимального заказа по критерию минимизации совокупных затрат по хранению запаса и повторение запаса.
3. Решением каких задач достигается формирование и контроль запасов?
4.Как устанавливается рациональный уровень страхового запаса?
5. Объясните управление запасами на складах методом с постоянной периодичностью поставок.
6. Объясните управление запасами на складах методом с постоянным объемом поставок.
7.По какому принципу производится организация складского хозяйства на АТП?
8. Как обеспечивается учет хранимой номенклатуры запчастей на складах.
9.Какой метод учета ведется на складах, в бухгалтерии?
10.Как должны хранится шины и другие резинотехнические изделия?
11.Как хранятся легковоспламеняющиеся изделия?
12.Какие документы, используемые на складах, относятся к типовым, первичным.
studfiles.net
Экономия в деталях
Снижение темпов производства, вызванное глобальным экономическим кризисом, незамедлительно сказалось на загрузке упаковочных линий. В свою очередь, многие запасные части, закупленные ранее для поддержки оборудования, оказались невостребованными и хранятся на складах заказчиков. Конечно, у любого производителя возникает вполне естественное желание снизить такие запасы. Однако простым росчерком пера в финансовых документах здесь не обойтись: вместо ожидаемой экономической выгоды такое сокращение может обернуться остановками оборудования из-за нехватки деталей. Как же совместить экономию на запчастях с бесперебойным выпуском продукции?
Избежать неприятных неожиданностей от подобной «экономии» поможет услуга Тетра Пак «Эффективная логистика запасных частей», которая позволяет оптимизировать складские запасы, уменьшив их на 10-15 % без ущерба для технологического процесса. Программа оптимизации склада запчастей, эффективность которой подтверждена на опыте нескольких лет у целого ряда заказчиков, ориентирована на специфику каждого конкретного предприятия и включает несколько этапов. Первый этап (длительностью 4–6 месяцев, в зависимости от особенностей оборудования) предполагает тщательный анализ состояния склада, складских процедур, эффективности планирования и работы персонала.
Мониторинг в тесном контакте с заказчиком осуществляется с помощью специального программного обеспечения. После изучения показателей специалистами Тетра Пак даются рекомендации и внедряется план мероприятий, которые позволяют предприятию уменьшить объемы запчастей на складе и оптимизировать его наполнение. В оптимизированной структуре склада запасных частей 70-80 % составляют «ходовые» детали, которые заменяются довольно часто. 20-30 % приходится на детали «страхового запаса», представляющие собой обычно сложные узлы и электронные устройства, которые реже выходят из строя, но играют ключевую роль в работе оборудования. Найти правильный баланс двух этих категорий и есть цель «Эффективной логистики».
На втором, более длительном этапе (до полутора лет), осуществляется надзор за соблюдением рекомендаций, оценивается их эффективность, выявляются и устраняются проблемы. Только такой подход обеспечивает закрепление полученных результатов и долговременную эффективную работу. Одним из важных аспектов оптимизации является налаживание информационного потока. От точности статистических данных зависит как наличие нужных деталей на складе, так и дальнейшее планирование закупок. Тетра Пак предлагает установить программу e-PIMS (Parts Inventory Management System), которая используется для эффективного управления складскими запасами. Поддержку ее работы компания обеспечивает на глобальном уровне.
При этом заказчик, имея полную статистику по расходу, также видит, сколько и каких деталей уходит на конкретную производственную линию. А в случае наличия нескольких производственных площадок – и состояние складов на каждой из них. С помощью услуги «Эффективная логистика запасных частей», разработанной на основе зарубежного и российского опыта, Тетра Пак помогает своим партнерам не только оптимизировать расходы на запасные части, но также обеспечить эффективное функционирование логистических и складских систем в долгосрочной перспективе. Более подробно программа описана на сайте www.tetrapak.su в разделе «Технический сервис. Услуги по повышению эффективности».
www.upakovano.ru
бизнес план, подбор стеллажей, выбор помещения
Правильно организованный склад является одним из наиболее важных и сильных звеньев в цепи работы бизнеса, связанного с автомобилями, будь-то автомагазин, СТО или оптовая база. Можно рассматривать склад автозапчастей и как отдельный бизнес, в основном он позволяет уменьшить издержки на хранение, обслуживание и другие статьи расхода более крупной структуры.
За счет быстрого перемещения товаров склад дает возможность ускорить оборот капиталовложений. Ключевым моментом в организации склада является движение товаров, а не их хранение – этот принцип крайне важен при планировании и определяет общую эффективность склада.
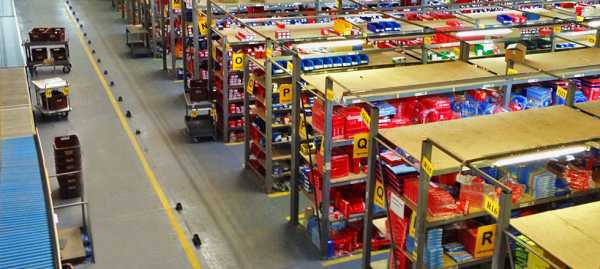
современный склад автозапчастей класса А
Нет однозначной классификации складов запчастей автомобилей, но возможно выделить основные группы, что дает возможность точнее подойти к задаче:
- Склады центральных представительств;
- Склады официальных дилеров и неофициальных представительств;
- Склады сетей, реализующих автозапчасти;
- Склады магазинов автозапчастей;
- Склады запчастей для ремонтных мастерских (СТО)
Понимание того, к какой из этих категорий относится склад, является одним из основных моментов во всем создании склада.
Выбор размера и расположения склада запчастей
Размер будущего склада определяется видом деятельности и планируемым товарооборотом. Для малого бизнеса в сфере розничной торговли автозапчастями, складов при станциях техобслуживания и ремонтных мастерских не требуется огромных помещений, поэтому оптимальным решением станут небольшие быстровозводимые склады из ЛСТК. Такие склады могут возводится как в «теплом» так и в «холодном» исполнении.
Для обшивки используются два основных материала — SIP-панель и профилированный стальной лист. Панели хороши для складов «теплого» типа, в которых зимой поддерживается нужная температура. Профнастил подходит для складов без обогрева.
Для небольшого склада удачным готовым решением может быть мини-склада площадью 112 м2.
Для более крупных проектов, под склады торговых дилерских сетей или официальных представительств также можно воспользоваться готовыми решениями, например:
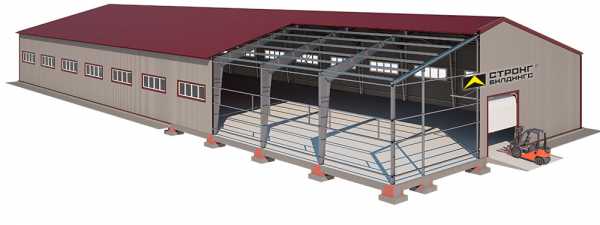
пример типового решения склада из ЛМК
Элементы здания выполнены в промышленных условиях из стальных листовых материалов, что обеспечивает высокую точность. Конструкция отличается значительной прочностью и стойкостью к огню, ветровым и сейсмическим нагрузкам. При этом элементы конструкции занимают минимальную площадь, что позволяет увеличить полезную площадь здания. В некоторых случаях используемая площадь расширяется на 20%, что упрощает вопрос, как оборудовать склад запчастей.
Главное преимущество подобных конструкций — цена. Средняя стоимость 1 м2 склада составляет от 2500 рублей.
Организация зоны погрузки — разгрузки
Площадь склада состоит из трех основных зон: приемки, хранения и выдачи. Чтобы максимально оптимизировать работу склада запчастей, требуется правильно задать входящий и исходящий поток грузов. Для входящего потока склад должен быть оборудован удобными подъездными путями, складскими воротами и платформами для удобной погрузки-разгрузки товаров.
Важно! Как выбрать правильные ворота для складского помещения
Неправильным подходом является организация входящего потока со смежного со складом участка при нахождении склада в составе более крупной станции. Если склад находится не на первом этаже, то рекомендуется установить грузовой лифт.
Для удобной и оперативной приемки товара, необходимо обеспечить «мост» для сообщения пола склада и бортом грузовика, который подвозит продукцию на склад. Для этого используются специальные перегрузочные мосты или «доквеллеры»:
Как выбрать доквеллер на склад
В случае, когда склад входит в комплекс городского или регионального представительства бренда, то исходящий поток должен разделяться на 2 части – выход в зону ремонта и обслуживания, и выдачу в клиентскую зону, где выполняются прямые продажи. В центральном представительстве отсутствует розница, а все акценты склада смещены.
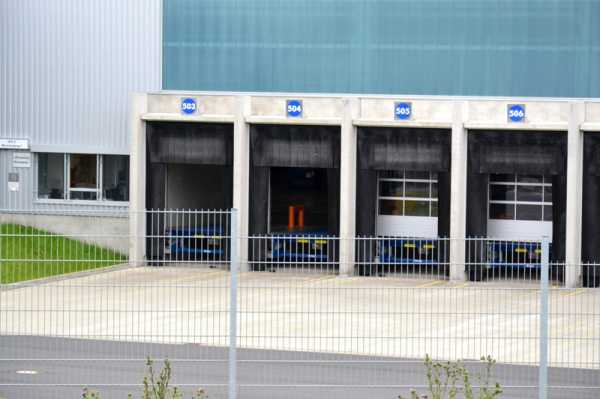
пример оборудования зоны разгрузки на складе запчастей VW
Анализируя эти потоки, можно подобрать наиболее удобное место для склада на территории станции. После этого определяются размеры склада. Для этого учитывается требуемый объем склада, частота и объем пополнения, скорость внутренней обработки товаров. Есть и более глубокие составляющие – ассортимент, сезонность и т. д.
Проектирование размещения товаров на складе
При планировании склада необходимо руководствоваться следующими принципами:
- Максимально удобное размещение запчастей;
- Уменьшение времени получения продукции с места хранения;
- Уменьшение времени приемки товаров и их размещения на складе.
При учете этих принципов в решении вопроса, как складировать запчасти на складе, частой возникают ситуации, что хорошая идея для одной задачи противоречит другой. Приведем пример удачно спроектированной зоны для хранения товаров на складе автозапчастей:
Схема правильного размещения стеллажей на складе автозапчастей (источник forma-com.ru )
Зону хранения можно разделить на такие части в зависимости от групп складской номенклатуры:
Кузовные детали
В эту группу входят капоты, крылья, двери, бампера и пр. Для их хранения используются вертикальные стеллажи для склада запчастей с переставляемыми разделителями. Одна деталь в среднем занимает 20 см от ширины стеллажа. Некоторые детали можно вкладывать друг в друга, такие как пластиковые крылья и бампера. При выборе размера этой части склада следует ориентироваться на общее направление работы станции.
К примеру, у дилеров работа направлена на простой и быстрый ремонт, поэтому количество хранимых деталей кузова невелико. Если стоит вопрос, как открыть склад кузовных автозапчастей, то эта часть склада будет занимать большое пространство.
Шины и колеса
Этой группе продукции требуются особые условия. Во многих автоцентрах эти условия не соблюдаются – резиновые изделия хранятся штабелем или складываются «елочкой». При длительном хранении это приводит к деформации резины в местах контакта с поддерживающими конструкциями. Рекомендуется хранить шины на специальных стеллажах на основе траверс.
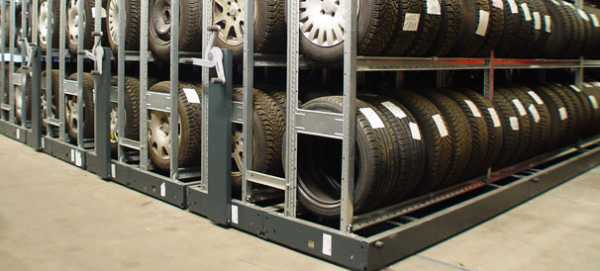
специальные стеллажные системы для хранения шин и колес
Для удобства хранения стеллажи можно комплектовать дополнительными элементами, в первую очередь разделителями. Это позволяет на одном стеллаже разместить не только шины, а и другие автозапчасти. Количество колес значительно различается в зависимости от типа склада. В региональных представительствах бренда может находиться одновременно до 500 комплектов.
Горюче-смазочные жидкости
Особенность их хранения является требования в отдельном месте хранения. На практике просто устанавливается перегородка, которая показывает отдельную комнату. Жидкости расфасованы в бочки объемом 200 и 60 л, а также меньшие емкости. Если работа ведется с грузовым автотранспортом, то требуемое количество бочек вырастает на порядок. Для хранения рекомендуется использовать стеллажи с колосниковыми решетками, это упрощает удаление подтеков.
Внимание. Если на складе планируется хранения легко воспламеняющихся жидкостей, обязательным этапом обустройства склада станет установка систем пожаротушения для складов ГСМ
Запчасти средних и малых габаритов
Они расфасованы в коробках, и в вопросе, как хранят запчасти на складе, проблем с ними не наблюдается. В среднем центре находится 2-3 тысячи наименований запчастей малых габаритов. Достаточно удобно использовать для них контейнеры с внутренними разделителями.
Чтобы упростить поиск изделий, рекомендуется использовать системы маркировки для стеллажей. Они могут представлять собой наклейки или магнитные кармашки, в которых размещаются указатели.
Автоматизация склада запчастей
Этот этап бизнес плана касается крупных складов оптовых дилеров и крупных представителей с площадью помещений от нескольких тысяч квадратных метров. Однако и малому бизнесу, который планирует расширяться, будет интересно знать о новых технологиях применяемых для автоматизации логистических процессов на складах автозапчастей.
Наиболее важным средством автоматизации является система управления складом. Она определяет оптимальные маршруты и места для размещения продукции. Эффективность такой системы лучше всего заметна при работе с большим количеством номенклатуры . Система управления позволяет снижать до минимума издержки, связанные с обработкой товаров, количество сотрудников склада, свести до минимума ошибки, связанные с человеческим фактором и максимально ускорить процесс обработки заказа.
Как сэкономить пространство на складе при хранении автозапчастей?
- Если оборот на вашем складе увеличился и количество наименований продукции значительно выросло
- Если ваши сотрудники тратят много времени на отбор заказа
- Надо расширять склад, но хочется сэкономить и не вкладываться в строительство новых площадей
Рассмотрите пример автоматизации склада с применением систем хранения лифтового типа, которые позволили сократить площадь хранения на складе на 75% (с 2000 до 500 кв.м.)
По вопросам строительства и проектирования складских помещений обращайтесь через форму обратной связи
skladovoy.ru
Управление запасами деталей на складах запасных частей
⇐ ПредыдущаяСтр 4 из 7Следующая ⇒Определение номенклатуры и объемов хранения деталей на складах
Очевидно, что хранить все выпускающиеся в качестве запасных частей детали и узлы на СТОА нерационально. Это приведет к значительному увеличению запасов, росту складских площадей и, самое главное, к неэффективному использованию запасов: большая их часть останется лежать «мертвым» грузом. С другой стороны, поскольку выход деталей из строя носит случайный характер, то в любой момент времени может понадобиться любая из выпускающихся запасных частей.
Изучение отечественного и зарубежного опыта организации МТО показало, что решается эта сложная задача применением складского способа продвижения продукции производственно-технического назначения от изготовителей к потребителям, заключающегося в централизации различных по номенклатуре и объему запасов на складах различных уровней. На складах дилеров и на СТОА хранят только самые «ходовые» детали, и запасы их при этом минимальные. На складах следующего уровня (региональный склад или логистический центр) хранимая номенклатура шире, а запасы по каждому наименованию больше. Наконец, вся номенклатура запасных частей и самые большие запасы по каждому наименованию деталей хранятся на центральном складе завода-изготовителя.
Между складами устанавливается оперативная связь, и по мере необходимости детали нужной номенклатуры со склада высшего уровня передаются на склад низшего уровня, тем самым поддерживается минимально необходимый для удовлетворения спроса запас на каждом из них. Преимуществом складской формы является то, что она создает все необходимые предпосылки для достижения комплектности материально-технического обеспечения.
Во-первых, СТОА и ремонтные мастерские в этом случае получают большую часть необходимых деталей не от нескольких поставщиков, а от одного, что позволяет точно согласовать сроки их поставки. Во-вторых, получение тех или иных видов материальных ценностей относительно независимо от сроков их изготовления заводом-изготовителем, что дает возможность планировать завоз деталей на склады в строгом соответствии с потребностью.
Определение номенклатуры запасных частей и объемов хранения на складах разного уровня осуществляется различными методами. В основу наиболее распространенного метода положено разделение всей номенклатуры запасных частей для каждой модели автомобиля по частоте спроса на группы А, В и С.
Группа А (детали высокого спроса) включает в себя 10... 15 % от общей номенклатуры запасных частей. Ими удовлетворяется примерно 85 % заказов потребителей, а их стоимость составляет 65... 70 % от стоимости всей потребляемой номенклатуры. Именно эти детали чаще всего выходят из строя, и заменой их на СТОА устраняют большую часть неисправностей и отказов.
Группа В (детали среднего спроса) включает в себя 15...20% от общей номенклатуры запасных частей, но ими удовлетворяется только 10 % спроса, а их стоимость составляет 25 % от стоимости всей номенклатуры.
Группа С (детали редкого спроса) включает в себя более 60 % от общей номенклатуры запасных частей, но ими удовлетворяется всего 5 % спроса, а их стоимость составляет 5... 10 % от стоимости всей номенклатуры.
Немногочисленные, но важные по расходу и стоимости детали (группа А) и детали, которые следует отнести к группам В и С, определяются на основе анализа продаж за предыдущие периоды и корректируются на основе обработки текущей информации о спросе и движении запасных частей в системе.
Из рис. 9.3 видно, что если на горизонтальной оси разместить в порядке уменьшения товарооборота запчасти, реализованные в прошедшем периоде, то можно легко определить те запчасти, которые имеют наибольшую стоимость при реализации (участок кривой до точки А). Эти детали относят к группе А. Наименования деталей, соответствующих участку АВ относят к группе В, а соответствующих участку ВС — к группе С.
Для определения объема хранения каждой детали и момента ее заказа для пополнения запаса на складе применяются различные методы: от простейших таблиц спроса до сложных экономико- математических расчетов.
Эти методы основаны на определении оптимальных размеров и периодичности заказа, при которых стоимость получения и хранения одной детали является минимальной (рис. 9.4).
Если одновременно заказать всю годовую потребность в деталях, то расходы на закупку и доставку заказа будут на единицу заказа минимальными, а затраты, связанные с хранением, максимальными. Например, при годовой потребности в 300 деталей и единовременном их заказе в течение года запас будет изменяться от максимального, равного 300, до минимального, равного нулю. При этом расходы на хранение будут определяться средним уровнем запаса, равного 150 деталям.
Рис. 9.3. Взаимосвязь номенклатуры и стоимости реализуемых запасных частей
Если размер заказа сократить до 30 деталей, то расходы на хранение будут определяться новым средним уровнем запаса — 15 деталей, т. е. сократятся, а затраты, связанные с закупкой и доставкой заказа, увеличатся (вместо одного придется сделать 10 заказов).
Рис. 9.4. График для определения оптимального размера заказа запчастей
Входными данными для определения размера и периодичности заказа служат годовая потребность в деталях S, затраты А, связанные с оформлением и получением заказа, и затраты / по содержанию единицы запаса.
Сбытовая сеть строится таким образом, чтобы гарантировать получение клиентами деталей, относящихся к группе А, в течение суток, а к группам В и С — через двое-трое суток после получения заказа.
В связи с этим объемы хранения деталей во всех звеньях сбытовой сети регулируются таким образом, чтобы на складах дилеров хранились одно-, двухмесячные запасы деталей высокого спроса, а на региональных — одно-, полуторамесячные запасы деталей высокого и среднего спроса.
Читайте также:
- АЛ для обработки корпусных деталей
- Анализ потребления и инвестиций как составных частей совокупного спроса
- Вопрос №3: Управление запасами в логистике (цель, функции, основные системы управления запасами): (нормативные величины, как рассчитываются) точка запаса, плюсы и минусы, прочие системы).
- Выполнение чертежей деталей, имеющих сопряжения
- Глава 1. Гидроизоляция. Защита заглубленных частей строящихся зданий от подземных вод и сырости
- Глава 11.0. Устройство, работа модули УПН и ее составных частей
- Деление окружности на три, шесть и двенадцать равных частей
- Дефектация деталей. Виды дефектов, методы контроля
- Для расчета деталей механизма продольной подачи токарного станка используют
- Допустимые расстояния до токоведущих частей, находящихся под напряжением
- Если фигура состоит из двух частей, то ее площадь равна сумме площадей этих частей.
- Заказ на 110 деталей первый рабочий выполняет на 1 час быстрее, чем второй. Сколько деталей в час делает второй рабочий, если известно, что первый за час делает на 1 деталь больше?
lektsia.com
Управление складом запчастей – Основные средства
В.Волгин
При выборе тактики управления запасами следует учитывать, что:
• каждая запасная часть – это отдельный товар;
• запасные части, не имеющие истории сбыта, требуют особого контроля, даже если анализ установит, что спрос не случаен;
• для новых моделей следует готовить заказы, выполняя тщательную инженерную проработку с учетом местных условий. уже в первый год эксплуатации половина машин потребует запчастей – для гарантийных и аварийных случаев, техобслуживания. для автомобилей следует сразу завозить детали оперения, фонари и т.д.;
Оптимальный запас деталей постоянного спроса для надежного удовлетворения заявок собственных дилеров поддерживают при помощи распределения запасов при обработке заявок потребителей. Для этого необходимо:
• каждому заказчику присвоить код важности: собственные дилеры – 1, оптовые заказчики (магазины и торговые фирмы) – 2, независимые ремонтники – 3, розничные покупатели – 4;
• обработку заказов собственных дилеров вести по всему наличию, а других заказчиков – по половине или другой доле, остальное – резерв для дилеров;
• специальный контроль и признаки распределения запаса для каждой детали – обработка по всему наличию, по половине наличия, по четверти наличия, не разрешена при минимальном запасе и т.д.
• ориентировать оптовиков (магазины) и независимых ремонтников системой специальных скидок на закупки запчастей у официальных дилеров для разгрузки склада от мелких заказов и создания постоянной сбытовой сети у каждого дилера.
Поставщикам удобнее получать крупные заказы с длительными сроками поставок и регулярно.
Дилерам удобнее не иметь запасов и получать запасные части по мере необходимости. Эти противоречивые устремления примиряют установлением высоких скидок на крупные заказы с квартальным и месячным сроками поставок и заметно меньших скидок – на срочные заказы.
Для обеспечения равномерной загрузки персонала заявки подразделяются на два вида – несрочные, которые не должны быть мелкими, и срочные, которые не должны быть крупными.
Срочные заявки принимаются до 11 или 12 часов утра с поставкой в тот же день. Поступившие заказы немедленно обрабатывают по наличию на складе. Отгрузка запасных частей по срочным готовым и несрочным заявкам, как правило, выполняется во второй половине дня.
Заявки, поступившие после 11–12 часов, выполняются на следующий день. Крупные склады практикуют круглосуточный прием срочных заявок, но срок отгрузки фиксируется точно так же. При этом в обоих случаях скидка остается в размере, установленном для срочных заявок.
В современном менеджменте расчет и контроль следующих параметров следует поручить компьютерной системе.
Продажи:
• продажи дилерам, оптовым заказчикам, сервисным предприятиям, торговцам и в розницу – отдельно по этим группам;
• динамика продаж по месяцам;
• сравнение их с планом-заданием и прошлым годом.
Объем заказов на пополнение склада:
• объем направленных заказов;
• объем просроченных заказов;
• количество позиций в невыполненных заказах;
• динамика состояния невыполненных заказов;
• степень удовлетворения заказов по номенклатуре;
• динамика степени удовлетворения спроса по месяцам;
• сравнение этих данных с прошлым годом.
Объем заявок клиентов:
• объем полученных заявок;
• объем просроченных заявок;
• количество позиций в невыполненных заявках;
• динамика состояния невыполненных заявок;
• степень удовлетворения спроса по номенклатуре;
• динамика удовлетворения спроса по месяцам;
• сравнение этих данных с планом–заданием и прошлым годом.
Объем запасов в целом:
• количество позиций на складе;
• оборачиваемость;
• динамика оборачиваемости по месяцам;
• сравнение этих данных с планом-заданием и прошлым годом.
Объем запасов:
• количество позиций;
• оборачиваемость;
• динамика оборачиваемости по месяцам;
* сравнение этих данных с планом-заданием и прошлым годом.
Неликвиды:
• количество неликвидов по номенклатуре;
• стоимость неликвидов;
• динамика состояния с ликвидацией неликвидов;
• сравнение этих данных с планом-заданием и прошлым годом.
Рентабельность:
• процент валового дохода службы запчастей;
• процент валового дохода на 1 служащего в месяц;
• доля службы запчастей в прибыли и убытках всей компании;
• сравнение этих данных с планом-заданием и прошлым годом.
Загрузка персонала:
• ежедневное количество и стоимость полученных позиций;
• ежедневное количество и стоимость отгруженных позиций ;
• ежедневное количество и стоимость позиций, отгруженных дилерам;
• количество и стоимость возвращенных позиций;
• количество и стоимость поврежденных и несоответствующих позиций;
• ход выполнения инвентаризации;
• количество и стоимость полученных и отгруженных позиций на 1 рабочего в день – загрузка;
• динамика загрузки по месяцам;
• сравнение этих данных с планом-заданием и прошлым годом.
os1.ru
Функции склада запасных частей | Требования к подразделениям | Структура автотехцентра | Читать онлайн, без регистрации
Функции склада запасных частей
Складская обработка – разгрузка, приемка, размещение, учет, комплектация для выдачи потребителям, упаковка, отгрузка. Приемка поступивших товаров, проверка количества и качества. Подготовка претензий на поврежденные запасные части и неудовлетворительное исполнение отгрузок поставщиками. Размещение товаров для хранения. Обеспечение сохранности товаров от повреждений и хищений. Соблюдение системы хранения и организации запасов во избежание пересортицы, размещение товаров наиболее экономичным способом. Своевременная корректировка базы данных при изменении адресов хранения деталей. Подбор, упаковка и выдача товаров по заказам клиентов. Ведение оперативного и финансового учета движения товаров. Контроль изменений номенклатуры запасных частей поставщиками. Предотвращение накопления неликвидов. Перманентная инвентаризация запасов, выборочная проверка соответствия фактического наличия данным компьютерного учета, установление фактов хищений и порчи товаров. Экспедирование получаемых и отгружаемых партий товаров. Обеспечение жизнедеятельности склада (ремонт помещений, тепло-, водо– и энергоснабжение и т. д.). Обеспечение эффективного планирования, адекватного имеющимся мощностям и рабочей силе. Обеспечение безопасности сотрудников, клиентов, машин, оборудования и собственности фирмы мерами по технике безопасности и контролем их исполнения.
Анализ результатов деятельности склада по установленным критериям. Эффективное использование объема склада, оптимизация оборудования склада, минимизация расходов, сокращение непродуктивных затрат времени. Разработка мер по повышению конкурентоспособности предприятия. Подготовка аналитических материалов и прогнозов для выработки решений по управлению деятельностью предприятия. Постановка задач для применения современных компьютерных технологий в деятельности склада и предприятия. Повышение квалификации персонала.
Эффективное использование объема склада, оптимизация оборудования. Соблюдение системы хранения во избежание пересортицы, размещение товаров наиболее экономичным способом. Своевременная корректировка базы данных при изменении адресов хранения деталей. Обеспечение сохранности товаров от повреждений и хищений. Учет и контроль движения товаров. Перманентная инвентаризация запасов товаров и материалов, выборочная проверка соответствия фактического наличия данным компьютерного учета, установление фактов хищений и порчи товаров. Контроль изменений номенклатуры запасных частей поставщиками. Предотвращение накопления неликвидов. Экспедирование получаемых и отгружаемых партий товаров. Оформление счетов и товаро-сопроводительных документов. Контроль поступления платежей. Регистрация упущенных продаж и анализ причин. Рассмотрение претензий по качеству запасных частей и сопутствующих товаров.
velib.com
Как оптимизировать пользование складами: примеры удачных решений | Склады
Как оптимизировать пользование складами: примеры удачных решений
Александр Перфильев, директор департамента складской и индустриальной недвижимости ILM
Я наблюдаю за складской недвижимостью уже в течение 10 лет, и на моей памяти это уже второй экономический кризис. В период стагнации многие компании вынуждены выживать. Они сокращают издержки, штат и проводят различные мероприятия по повышению эффективности своего бизнеса.
Тема оптимизации всегда актуальна в логистике. Большинство компаний рассматривают экономию на складе как обязательную статью снижения издержек.
Существует как минимум четыре основных способа оптимизации расходов на склад: управление запасами, изменение технологии хранения, изменение площади склада, а также экономия за счет улучшения коммерческих условий. Первые два способа оптимизации относятся к логистике, а два последних - к сфере недвижимости.
В логистике есть термин: затраты по хранению на единицу продукции. Именно на этот показатель ориентируются директора по логистике и предпринимают усилия по снижению затрат.
При изменении технологий хранения компания проектирует увеличение емкости склада за счет размещения большего количества паллето-мест. Например, можно перейти с широкопроходной технологии расстановки стеллажей на узкопроходную. Возможен и другой вариант, когда на одной из частей склада размещаются глубинные стеллажи или шатловая система. Так, на стандартном складе класса А средний коэффициент утилизации составляет 1,2-1,5. Это означает, что на 1000 кв. м склада можно хранить 1200-1500 европаллет (размер европаллета составляет 1,2*0,8 м). Там, где применяется узкопроходная технология, можно приблизиться к коэффициенту 1,8, а при использовании глубинных стеллажей на 1000 кв. м склада можно разместить 2000 и более паллет. Новые стеллажи, техника для их обслуживания, а также новые технологии размещения, как правило, требуют инвестиции.
Каждый логист умеет проводить ABC анализ. В его основе лежит принцип Парето - 20% всех товаров обеспечивают 80% оборота. Согласно этому принципу, от товара, на который отсутствует спрос, следует избавляться. Иногда дешевле утилизировать, чем годами платить за хранение такого груза.
Существуют и исключения, когда есть необходимость в таком хранении. Например, склады запасных частей, которые обязаны хранить детали под замену. Но в большинстве случаев после анализа часть склада высвобождается.
Помимо этого, проводится анализ эффективности размещения товаров на складе. Довольно часто коробка небольших размеров занимает место, где можно разместить груз размером с холодильник. Существуют методики, которые позволяют оптимизировать размещения и высвободить дополнительные площади. Программа WMS – это система управления складом, позволяющая организовывать размещение более эффективно.
Если часть склада не используется либо компании удалось высвободить площади путем оптимизации, то необходимо предпринять попытку возврата излишних помещений арендодателю. Если же возможности возврата нет либо склад является собственностью компании, то свободные площади сдаются в субаренду(аренду), либо в этой части склада оказываются услуги ответственного хранения. В случае субаренды компания может предлагать потенциальным арендаторам ставки ниже рынка, потому что в данном случае ее основная задача не заработать, а снизить свои затраты на владение складом.
Вариант переезда в новый склад меньшей площади также может быть рассмотрен как один из путей снижения издержек. Следуя этому пути, помимо уменьшения площади есть возможность получить лучшие коммерческие условия и дополнительные арендные каникулы. Это существенным образом влияет на суммарные затраты на новый склад. Иногда, воспользовавшись всеми этими преференциями, компании почти в 3 раза снижают свои затраты на аренду склада. Мне известны случаи, когда были арендованы склады площадью 20 000 кв. м при фактических потребностях на уровне 10 000 кв. м. Такое могло произойти по разным причинам, но, как правило, история у всех почти всегда одинаковая: перед кризисом взяли площади немного с запасом, с учетом расширения, а бизнес и товарооборот сократился. При ставке в 6 000 руб. в год за 1 кв м такая компания тратит 120 млн руб. в год. Если они переедут на склад вдвое меньшей площади и получат ставку 5 000 руб. в год (на 15% ниже), их затраты уменьшатся до 51 млн. Можно только представить, что нужно предпринять отделу продаж, чтобы получить дополнительную чистую прибыть в размере 50 млн руб.!
Что касается улучшения коммерческих условий, то ни в 2008-2009 гг., ни сейчас я не встречал ни одну компанию арендатора, которая бы не обратилась к арендодателю с просьбой о дополнительной скидке и преференциях сверх того, что оговорено в долгосрочном договоре аренды. С таким предложением обращались все компании, независимо от их статуса, размера арендованных площадей, сферы деятельности или страны происхождения. Скидку просили и небольшие российские компании, и транснациональные гиганты. Большинство собственников помещений в той или иной мере шли на уступки.
Если год назад самым распространенным было обращение о переводе из долларовых контрактов в рублевые либо фиксация курса, а также скидка в случае рублевых контрактов, то трендом этого года является выход с предложением о заморозке ежегодной индексации. Сразу хочу заметить, что на повторные уступки арендодатели идут неохотно. Ведь владельцам недвижимости и девелоперам в кризис также приходится не сладко. Их давят кредиты, снижение денежного потока, вызванное теми самыми скидками, и пустые помещения, которые в это непростое время сдаются с большим трудом. Однако и здесь собственники подходят к вопросу уступок избирательно и каждый случай рассматривают индивидуально.
Подводя итог, могу сказать, что самым лучшим рецептом оптимизировать затраты на склад является использование всех этих методик. Сейчас, несмотря на кризис, все больше компаний прибегает к услугам профессиональных консультантов. Это относится как к изменениям в логистических технологиях, так и к вопросам, касающимся склада как недвижимости. Наблюдается четкая тенденция - собственники бизнеса чаще обращаются к консультантам, чем нанятые ими профессионалы. Последние не всегда могут обосновать необходимость внешнего консалтинга и часто боятся показаться перед собственником некомпетентными в этих вопросах. На самом деле собственные специалисты по логистике и топ-менеджмент могут проводить оптимизацию самостоятельно. Но, как правило, на это уходит больше времени, выше риск ошибок, достигается меньшая эффективность, а на внедрение тратится больше людских и финансовых средств. Консультант, который выполнил десятки подобных проектов, столкнулся на своем пути со множеством ошибок, быстро предлагает наиболее эффективное решение в каждом конкретном случае. Профессиональный консультант знает рынок, ограниченные по времени специальные предложения, имеет отличные навыки переговорщика и возможность выбрать лучший склад из всего рынка предложений.
Источник: CRE.ru
ekbrealty.ru