Оптимизация операций на производстве. Оптимизация на производстве
инженер поможет - Оптимизация производства
Существуют руководящие принципы, обеспечивающие успех в долгосрочной перспективе развития производства, независимо от различий между странами и ассортиментом деталей. Я собрал 10 принципов и поделился ими здесь. Надеюсь, этот список пбудет обсуждаться на нашем сайте.
1. Ищите сходства, а не различия.
Когда пришло время стандартизировать, внедрять бережливые производственные технологии, разрабатывать новые компоненты, разрабатывать приборы или писать программы с ЧПУ, пришло время переключать передачи и находить сходства между всей конструторской документацией. Зачем разрабатывать новый компонент, если он уже существует, который будет соответствовать требованиям?
Когда детали на 80 процентов похожи, воспользуйтесь этими признаками, чтобы использовать существующие стакни, инструменты, процессы, программы, метрологию и т. д., а затем обращайтесь к остальным 20 процентам. Разница между инженером, который хочет создать что-то новое и необычное, и инженером, который использует существующий процесс неизмерима.
2. Вы управляете спринтом и марафоном.
Сотрудники стремятся достичь удовлетворенности клиентов и оптимизировать показатели, но кто планирует долгосрочные результаты? Кто определяет будущие потребности клиентов и развивает людей, оборудование, программное обеспечение и процессы для удовлетворения этих потребностей перед конкуренцией? Многие организации так сосредоточены на краткосрочной перспективе, что через несколько лет они просыпаются, обнаруживая, что их оборудование и процессы устарели и непродуктивны.
3. Качество - это производительность.
Низкое качество потребляет ресурсы и снижает производительность. Надежные процессы в сочетании с качеством позволяют операторам оптимизировать свое время и, таким образом, возможно работать с несколькими станками.
4. Идите прямо, прежде чем идти быстро.
Это полезно иметь чувство неотложности. Однако, когда есть новый процесс, новый компьютер, новая программа или просто новая настройка, вещи должны быть «правильными», прежде чем они могут быть быстрыми. Станки и люди делают плохие детали так же быстро, как и хорошие детали. Сделать их в два раза намного медленнее и дороже, чем сначала убедиться, что вы правы. Стандартные работы и проверки - это инструменты, которые позволяют это. 5. Учитесь и тренируйтесь. Фирмы, которые учатся быстрее, чем их конкуренция, в конечном итоге превзойдут свою конкуренцию. Поезд, поезда и поезд немного больше. Независимо от того, является ли человек оператором, инженером или руководителем, передача знаний одновременно является инвестиционным и страховым полисом.
6. Достичь прогресса, а не совершенства.
Когда ожидание состоит в том, что новая станок или новый процесс немедленно дадут максимальные результаты, тогда производство станет не склонным к риску, а не инновационным.
7. Измерение должно быть быстрым и точным.
Измерение не должно давать погрешности при измерении или погрешности приборов. Измерение также должно быть быстрым, не только для производительности, но и для того, чтобы метролог мог проверить больше деталей и собрать больше данных. Дополнительные данные с использованием большего количества деталей позволяют лучше контролировать входные сигналы и улучшать измерения в зоне допуска.
8. Если у Вас нет цели, вы не зарабатываете деньги.
Будь то шлифовка, EDM, токарная обработка или другой тип обработки, конкретная цель всей организации - от администратора до инженера - поддерживать операции, чтобы станки производили детали. Это простая концепция, но иногда люди в организации теряют перспективу в задачах, которые действительно приносят доход.
9. Работайте на нескольких станках.
Настройте ожидания инженеров, программистов и операторов, чтобы автоматизировать и внедрить требования к рабочему, инструментальному и метрологическому обеспечению, чтобы обеспечить непрерывную механическую обработку как можно дольше. Это позволит использовать несколько станков одним оператором. Это необходимо для победы над конкурентами в странах с более низкими затратами на рабочую силу.
10. Направить решения на самый низкий уровень.
Этот совет многогранен. Чтобы работники развивались, им необходимо принимать решения. Будут ли они ошибаться? Конечно. Но их ошибки будут менее дорогостоящими, чем апатия и задержка, вызванная ожиданием от старшего менеджера решения. Когда сотрудники должны добиваться утверждения на каждом шагу, они не могут действовать со скоростью и, скорее всего, не будут действовать вообще. Непрерывное улучшение требует культуры и осведомленности сотрудников о том, что успех - это больше, чем выполнение рутинных задач, используя тот же процесс, что и вчера. Обсуждение этих 10 руководящих принципов на производстве является хорошим первым шагом.
engcrafts.com
от программного обеспечения до производства / Статьи и обзоры / Элек.ру
Составляющие эффективной работы в сети Интернет от Владимира Рощина, коммерческого директора ООО «ЛайтЭлектроСнаб» (г. Москва):
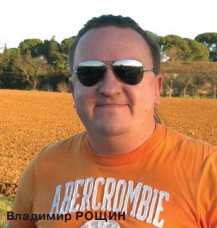
1. Хороший провайдер и скоростная выделенная линия. Уже на протяжении пяти лет нашим «поставщиком» интернета и телефонии является компания «Вымпелком», более известная как Beeline. Дорого, скажут некоторые. Есть масса Noname-net компаний, который обещают за три рубля в год обеспечить вашу компанию бесперебойной связью. Может, так и есть, но когда к сети подключается больше одного компьютера, то сразу становится понятна причина подобной дешевизны. Да, дорого! Но мы знаем, за что платим. За последние несколько лет ни одного перебоя в работе и отличная скорость при огромном объеме трафика, притом, что на одной линии работает не один десяток компьютеров. 2. Собственно сами компьютеры. Господа! Не экономьте на «железе» — это ваше время, а стало быть — деньги. В «ЛайтЭлектроСнаб» не найти ни одной рабочей машины, которая оснащена меньше чем двухъядерным процессором, благодаря постоянному плановому апгрейду техники. Также вы не увидите и мониторов-ящичков образца 90-х годов, которые, что греха таить, еще встречаются у некоторых на рабочих местах. 3. Специалисты, которые поддерживают жизнедеятельность всего этого хозяйства. Мы давно отказались от собственного «сисадмина» и ушли под «надежное крыло» IT-аутсорсин-говой компании, которая уже на протяжении трех лет контролирует IT-структуру компании на всех уровнях и этапах, и делает это профессионально и оперативно. 4. Ну, и конечно, правильное программное обеспечение плюс современные скоростные браузеры.
В Советском Союзе уделялось много внимания вопросам производительности труда. «Стахановское движение» было мощным толчком для ее повышения. Страна ежедневно получала рекорды. Рекорды количественные, достигнутые, зачастую, путем нечеловеческих усилий, следствием которых была неспособность дотянуть до обычной нормы уже на следующий день. О какой-то системности говорить не приходилось. Лишь иногда на общем фоне возросшие показатели выработки угля или молочных надоев являлись результатом грамотного процесса оптимизации производства. Именно она и является главным предметом нашего сегодняшнего разговора. Как сегодня снижаются затраты предприятия? Какими методами оптимизируются бизнес-процессы? Может ли оптимизация быть завершенной?
Об этом впереди, а пока определимся с самим термином. Что же такое «оптимизация производственных процессов», и какой круг вопросов она охватывает? За ответами обратимся к Сергею Смирнову, кандидату педагогических наук и эксперту по вопросам повышения производительности труда:
— За основу возьмем такое определение: «Оптимизация» — модификация системы для улучшения ее эффективности». Хотя я в своей практике использую словосочетание «улучшение производственной системы». Производственная система — это совокупность человека, средства производства и предмета труда. Взаимодействие их вовремени организует производственный процесс или процесс добавления ценности. Думаю, круг вопросов определяется кругом проблем. Практически для всех предприятий они общие. Это простои, недостаточная квалификация персонала, текучка кадров, низкое качество продукции, сокращение продаж, увеличение себестоимости, несоблюдение сроков исполнения заказа, нерациональное использование рабочего времени, неэффективное использование оборудования, задержка оплаты и т.д., и т.п. Главное, что все они взаимосвязаны, поэтому и оптимизировать необходимо всю систему и все влияющие факторы.
— На тему оптимизации достаточно сложно говорить в общем. Во-первых, нет одинаковых правил для всех типов производств: практически каждая отрасль имеет свою специфику и требует различных подходов. Если говорить о машиностроении, то эта отрасль наиболее требовательна к постоянной модернизации. Конкурентоспособность машиностроительного предприятия напрямую зависит от эффективности производства. Стремясь снизить затраты, компании постоянно совершенствуют машины и оборудование, системы управления производством, внутреннюю логистику. Например, один из крупнейших заводов в мире по производству дизельных двигателей компании Volvo Penta. На сегодняшний день является самым современным заводом такого типа в мире. Несмотря на это там полным ходом идет модернизация литейного производства, что позволит снизить себестоимость литья на 5–10%, повысить стандарты экологичности и чистоты производства. Кроме того, во всем мире постоянно растут требования к охране труда и окружающей среды. Эти внешние факторы заставляют компании осуществлять дорогостоящую модернизацию. В России эти факторы также имеют место, но основным движущим фактором является повышение эффективности производства. Производительность труда в России в среднем в два с половиной три раза ниже, чем в Европе, и ключевым фактором как преодолению этого разрыва является как раз модернизация.
Что касается «ПСМ», оптимизация производственных процессов у нас происходит постоянно. Причем, это касается всех этапов: в прошлом году внедрили систему 1С, сейчас оптимизируем складскую логистику, отдельные производственные этапы. Строим завод металлоконструкций и модернизируем основой завод по производству дизель-генераторов: ремонтируем цеха, закупаем новое оборудование. Мы уверены, это позволит снизить производственные затраты и повысить качество, а значит, и конкурентноспособность нашей продукции. Мы и впредь будем продолжать оптимизацию. А в целом, мне кажется, что если модернизация машиностроительных производств когда-то остановится, это будет означать конец прогресса человечества. Из комментария становится ясно, что оптимизация является единым проектом всех служб предприятия, а не только лишь производства. Но давайте озадачимся одним вопросом: для чего все это собственникам и владельцам компаний? Безусловно, чтобы достичь одной, главной цели — увеличения прибыли! Прибыль — вот смысловой тренд любого бизнеса. Не значит ли это, что и обсуждаемый нами круг вопросов тоже лишь некая мода сегодняшнего дня? За ответом и комментариями по оптимизации бизнес-процессов в отдельно взятой компании мы обратились к Евгению Ойстачеру, главе Правления EKF Group (г. Москва):
— Нет, оптимизация — это не тренд последних посткризиных лет. Это постоянный процесс поиска более совершенных и эффективных решений, способов производства, схем логистики и сбыта. Сколько существует предпринимательство, столько, мне кажется, люди стараются оптимизировать свою работу: снизить издержки, повысить результативность и прибыль. EKF — не исключение.
Сегодня проблема неэкономичного расходования и неравномерного распределения ресурсов звучит еще острее. В 2010 году мы развернули в EKF целую программу по внедрению стандартов и философии lean (бережливое производство), пригласили экспертов и опытных менеджеров на свои производства в Балакирево и Подмосковье (предприятия по производству электрощитового оборудования и кабельных лотков, входящие в Группу компаний EKF — прим. редакции). На внедрение lean нас вдохновила книга Джеффри Лайкера «Дао Toyota». Нам в EKF импонирует этот подход по двум причинам: во-первых, проверено временем, он работает, во-вторых, дао Тоyota основано на обучении и развитии персонала. Развитие — это одна из базовых ценностей EKF.
За эти два года нам удалось организовать непрерывный поток на производствах, распределить нагрузку работников и оборудования, что снизило расходы на ремонт и обслуживание станкового парка. Прежде всего, это обеспечивается слаженной работой между подразделениями сбыта — логистикой и продажами — и самими производственными площадками, а также заимствованием передовых подходов с других рынков. Топ-менеджеры производств, объединенных в Группу компаний EKF, разработали внутреннюю систему стандартизации и регламентов, которая позволила сократить время цикла производства, повысить качество за счет самоконтроля, увеличить производительность.
Важным шагом в оптимизации наших производств стало обновление технических мощностей: автоматизации, введения нового современного оборудования с компьютерным управлением, автоматизация большинства процессов производства и упаковки. И мы постоянно ищем, что можно еще автоматизировать, задаем себе вопрос, что это может дать в далекой перспективе. Почему делаю упор на слове «далекая»? — потому что не все меры по оптимизации и автоматизации производств окупаются быстро, нужно быть готовым к этому.
Джеффри Лайкер и Тойота вдохновили нас и на оптимизацию бизнес-процессов в торговой компании EKF Electrotechnica. В частности преобразовали процессы согласования бюджета и согласования выделения средств в рамках бюджетных статей. Мы перевели документооборот в электронный формат. Благодаря Сервису IMS компании EKF теперь первичную документацию партнеры получают автоматически, автоматизированы процессы информирования покупателей о дебиторской задолженности. Сейчас мы налаживаем обмен информацией с партнерами о динамике их продаж по марке EKF и информацией о состоянии наших складских запасов. Уверены, что это повысит оперативность нашей работы, уровень сервиса, поможет нашим партнерам предоставлять своим клиентам оборудование марки EKF точно в срок. Мы отлично понимаем, что EKF — крупная и продолжающая рост и расширение компания. И полное отсутствие бюрократии в компаниях нашего масштаба невозможно. Но благодаря оптимизации бизнес-процессов и внедрению Сервиса IMS компании EKF мы достигли баланса между структурированностью и гибкостью, мощностью бизнеса и легкостью коммуникации.
Не все меры по оптимизации и автоматизации производств окупаются быстро, нужно быть готовым к этому.
Сейчас мы сами в каком-то смысле выступаем драйверами автоматизации процессов и предлагаем Партнерам работать через Сервис IMS компании EKF: совершать закупки и проводить заявки, получать информацию о поступлениях и наличии на складах EKF и складах Дистрибьюторов в своем регионе, привлекать клиентов и находить подрядчиков, участвовать в проектах.
В свете вышеупомянутой книги Джеффри Лайкера «Дао Toyota» нельзя не сказать о Японии. Ярчайший пример страны с высокой культурой производства. К каким же мерам прибегают там, чтобы максимально снизить потери? За ответом обратимся к Сергею Жишкеви-чу, главному редактору портала www.up-pro.ru, который побеседовал с Норицугу Уэмурой, генеральным директором Mitsubishi Electric Europe B.V (г. Москва):
— В Mitsubishi Electric Europe ис-пользуетя термин «эффективное производство», а не «бережливое производство», так как он в большей степени соответствует стратегии компании. Стоит отметить, что оптимизация производственных и бизнес-процессов в настоящее время как никогда актуальна, особенно для Японии, поскольку в стране природные ресурсы в значительной степени ограничены. Кроме того, за счет оптимизации достигается, в том числе, и конкурентоспособность продукции на внешних рынках, ведь в конечном итоге удается снизить ее стоимость и повысить качество.
С целью повышения эффективности производства и минимизации производственных издержек используется традиционный японский метод «Kaizen» (концепция постепенного, непрерывного улучшения), а также методика «Just-in-time» («точно в срок») (полная синхронизация поставок с процессами производства и реализации). В рамках этих методов постоянно модернизируются процессы, происходящие в компании, в том числе процесс производства. Компания использует собственные современные разработки, а также производственный инжиниринг для сокращения затрат электроэнергии, воды и материалов. Кроме того, «Мицубиси Электрик» пропагандирует и реализует концепцию безотходного производства, которая подразумевает переработку и повторное использование полученных в результате производства и использования продукции компании отходов, таких как пластик.
Успешным опытом оптимизации делится Владимир Млынчик, генеральный директор Quadro Electric (г. Санкт-Петербург):
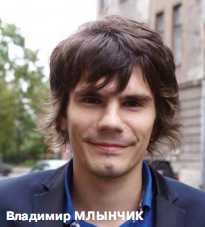
— Для оптимизации деятельности компании мы применяем множество разных систем. Но я остановлюсь на самых, на мой взгляд, интересных.
Во-первых, это эффективное техническое оснащение персонала. Сотрудники всех подразделений обеспечиваются смартфонами, а так же планшетными компьютерами, что позволяет экономить время и делает их работу на всех уровнях более продуктивной. Мы заключили партнерское соглашение с компанией, производящей умную технику, и она бесплатно обеспечивает наших сотрудников гаджетами.
Во-вторых, мы используем сетевые системы планирования и документооборота, благодаря которым любой сотрудник, где бы он не находился, может быть погружен в рабочий процесс и обмениваться информацией с остальными. Так, монтажник, сидящий, на краю бетонной плиты на объекте, может совместно с менеджером, так же сидящим, но за столом в офисе, редактировать любой файл.
Постоянное следование новейшим технологиям и тенденциям, делает нашу работу быстрой, эффективной и качественной. Нам удивляются.
Что тут сказать! Япония — страна не только высокой производственной культуры, но и высоких технологий! Кстати, о них. Но не на производстве, где без роботизированных станков или автоматизированных линий с ЧПУ выпуск конкурентноспособной продукции просто немыслим, а, скажем, в компании, занимающейся энергоаудитом. В питерской Quadro Electric сотрудники вооружены высокотехнологичными гаджетами.
Но, может быть, никто и не задумывался над оптимизацией затрат? На самом деле и тут все налажено, говорит Николай Алексеев, финансовый директор компании Quadro Electric (г.Санкт-Петербурге):
— Для оптимизации своих затрат мы применяем многоуровневую систему бюджетирования. Причем, для более детального анализа и планирования затрат привлекаются сотрудники всех подразделений. В управлении компанией опираемся на принципы концепции LEAN. Эта концепция менеджмента основана на неуклонном стремлении к устранению всех видов потерь. Она предполагает вовлечение в процесс оптимизации бизнеса каждого сотрудника и максимальную ориентацию на потребителя. Сегодня ее успешно используют тысячи компаний во всем мире, и Quadro Electric не стала исключением. Это позволяет нам оперативно выявлять и устранять все точки необоснованных затрат как в офисе, так и в производстве.
Обратите внимание — «затрат»! В сегодняшнем посткризисном мире это едва ли не приоритетная составляющая процесса оптимизации. Но бывает ли их сокращение неэффективным и как этого избежать? Разъяснения по этим вопросам у Елены Куренной, главного бухгалтера ООО «СЗПМ»:
— Экономия затрат всегда была основной задачей для любого бизнеса. Экономят, или лучше сказать, оптимизируют компании обычно все подряд: от заработной платы сотрудников до мелких офисных расходов. Для того, чтобы избежать панического неэффективного сокращения затрат, необходимо создать целую систему управления ими, которая включает в себя и повышение координации деятельности различных структурных подразделений, и обеспечение финансовой дисциплины, и установление лимитов затрат и нормативов по отдельным видам товаров и услуг, видам бизнеса и структурным подразделениям.
Одной из стратегических задач управления хозяйственной деятельностью такого промышленного предприятия, как наше, является снижение издержек. Для достижения результатов ведется работа по нескольким направлениям, в число которых входят снижение уровня производственного брака, экономия материальных ресурсов, энергоэффективность при эксплуатации производственного оборудования.
Важную роль играет оптимизация процесса закупок, ведь цены закупаемых комплектующих и услуг во многом определяют себестоимость продукции нашего предприятия. От своевременности поступления необходимых ресурсов зависят выполнение производственного плана, соблюдение сроков отгрузки продукции потребителям, и как следствие, размер выручки предприятия. От соответствия объемов закупаемых материалов текущей потребности зависит величина денежных средств, замораживаемых в форме запасов.
Кадры, простои, издержки, затраты, сроки… Бесконечный круг вопросов, которые возникают снова и снова. Тогда может ли, в принципе, оптимизация производства быть закончена или это постоянно продолжающийся процесс? Узнаем, мнения представителей компаний «Русский Трансформатор» и RS Group.
Алексей Зубарьков, заместитель генерального директора ЭТК «Русский Трансформатор»:
— Думаю, большинство со мной согласится, что оптимизация любого процесса (в т.ч. производства) не может быть закончена. Недаром говорят — «нет предела совершенству». Любой руководитель должен понимать, что если остановиться на достигнутом результате, то очень скоро можно оказаться в аутсайдерах. Технологии не стоят на месте, и каждый день мы читаем в новостях о все новых и новых достижениях, способных кардинально изменить наш мир через несколько лет.
Например, всего 20–30 лет назад о компьютерах многие даже не слышали. Именно с компьютерами связан один из основных способов оптимизации — автоматизация. Автоматизация — это не просто покупка станков с ЧПУ. Зачастую, автоматизация процесса продаж и управленческих вопросов может принести гораздо больше пользы. Я считаю, что именно на автоматизацию всех процессов стоит обратить внимание в первую очередь.
Безусловно, есть еще множество направлений для оптимизации, как то: энергоэффективность, логистика, аутсорсинг и прочее. Но, даже максимально оптимизированное на сегодня производство, уже завтра будет в чем-то не совершенным. Оптимизация — это непрерывный процесс, и именно он привел наше общество от эпохи каменного топора к эпохе космических кораблей.
Роман Земцов, директор по маркетингу компании RS Group (г. Москва):
— Основываясь на своем трехлетнем опыте работы директором по маркетингу и сбыту трансформаторного завода и нынешней деятельности, отвечу, что процесс этот непрерывный. Предприятию необходимо идти путем постоянного улучшения собственных процессов. Иначе будет крайне тяжело выдержать конкуренцию в современных рыночных реалиях. Особенно на фоне вступления России в ВТО.
Безусловно, формат оптимизации зависит от масштаба предприятия, отрасли, экономической ситуации и пр. Но потенциал для улучшений есть всегда. При этом, под «производством» я бы подразумевал не только фактический выпуск продукции, но также логистику, маркетинг, коммерцию, ФЭД, службу HR, НИ-ОКР, департамент IT. Все подразделения должны работать как единый слаженный механизм. А достичь такого взаимодействия не так просто. При этом оптимизация напоминает гонку за горизонтом. На смену одним технологиям приходят другие, более эффективные. Время жизненного цикла продуктов стремительно уменьшается. Маркетинговые инвестиции на продвижение продукции растут. На смену одним поставщикам приходят другие. Повышение квалификации персонала есть осознанная необходимость. И те предприятия, на которых менеджмент сможет вовлечь всех сотрудников в непрерывный процесс оптимизации производства, получат дополнительные конкурентные преимущества.
Вот так обстоят сегодня дела в компаниях отрасли. Среди них есть гиганты с многотысячными коллективами, а есть и совсем небольшие. Однако везде задумываются над тем, как сделать работу более эффективной, выбирая при этом свой путь. Тем не менее, существует и общее правило: оптимизация производственных процессов должна охватывать всех — от директора, до рабочего. И одним из первичных условий для повышения производительности труда является материальный стимул, т.е. достойная и своевременная плата за проделанную работу. Может быть тогда, сталинское «жить стало лучше, жить стало веселее», без доли иронии снова вернется в народ.
Тимур ЖЕМЛИХАНОВ
www.elec.ru
Оптимизация производства. Программа управления работой по изготовлению продукции и повышению объема ассортимента поставок
По мнению 362 организаций рейтинг: 4.9Поддержка стран: Все Операционная система: Windows Семейство: Универсальная Система УчетаНазначение: Автоматизация бизнеса
Основные возможности программы:
Вы можете изготавливать любую продукцию, используя при этом любые материалы или полуфабрикаты
Учет продукции
По каждой продукции можно составить калькуляцию, чтобы программа автоматически рассчитывала количество необходимого сырья
Калькуляция
Есть возможность посмотреть себестоимость каждой выпускаемой продукции
Себестоимость
Отдел снабжения может приходовать сырье, передавать в производственный отдел и списывать
Снабжение
Программа может работать с любым количеством складов и подразделений
Склады
У Вас сформируется единая база клиентов со всеми необходимыми контактными данными
База клиентов
Все заказы будут храниться в базе данных, по их количеству можно будет планировать объем производства
Заказы
Заказы можно компоновать по маршрутам следования, которые будут распечатываться водителям
Маршруты
Каждый день можно приходовать произведенную продукцию на склад готовой продукции, сравнивая планируемое потребление сырья с фактическим
Производство
Договора, бланки, спецификации заказов и многое другое может формироваться автоматически
Заполнение бланков
К каждому заказу можно прикреплять любые файлы, например, с макетом заказа
Вложенные файлы
Каждую услугу можно разделить на определенные работы и этапы и легко их контролировать
Этапы производства
Вы сможете отслеживать исполнение работ по вашим сотрудникам и контролировать их эффективность
Контроль работ
Все отделы будут взаимодействовать между собой как единый успешный механизм
Связь отделов
Программа умеет по средним производственным показателям показывать на сколько дней беспрерывной работы хватит имеющегося на складе сырья
Прогнозирование
Вы сможете вести полноценный финансовый учет: проводить доходы, любые расходы, видеть прибыль и смотреть различные аналитические отчеты
Учет финансов
Интеграция с новейшими технологиями позволит вам эпатировать клиентов и заслуженно получить репутацию самой современной компании
Эксклюзивность
Ультра-современная функция связи с АТС позволит видеть данные звонящего, эпатировать клиента, сразу обращаясь к нему по имени, не тратить ни секунды на поиск информации
Телефония
Нужные данные могут загружаться на ваш сайт для контроля статуса заказа, отображения стоимости продукции - возможностей множество!
Интеграция с сайтом
Вы можете заказать, чтобы на отдельном большом экране отображались сводки со всех ваших торговых точек. Чтобы Вы в режиме реального времени контролировали: свои доходы, исполнение заданий сотрудниками или процесс производства
Вывод на экран
Связь с платежными терминалами, чтобы клиенты могли оплачивать свои заказы в ближайшем терминале. Такие оплаты автоматически будут отображаться в программе
Платежные терминалы
Если у Вас заполняются договора и прочие документы, мы можем настроить их автоматическое заполнение, чтобы один ваш сотрудник с помощью программы выполнял такой же объем работы, как несколько других сотрудников вручную
Заполнение документов
Система планирования позволяет настроить расписание резервного копирования, получения важных отчетов строго в определенное время и задать любые другие действия программы
Планировщик
Специальная программа сохранит по расписанию копию всех ваших данных в программе без необходимости останавливать работу в системе, автоматически заархивирует и уведомит о готовности
Резервное копирование
Вы сможете быстро внести первоначальные данные, необходимые для работы программы. Для этого используется удобный ручной ввод или импорт данных
Быстрый старт
Мы добавили множество красивейших шаблонов, чтобы работа в нашей программе приносила еще большее удовольствие
Красивый дизайн
Интерфейс программы настолько легок, что в ней может быстро разобраться даже ребенок
Легкая программа
Автоматизация бизнеса нами выполнена для множества организаций:
Язык базовой версии программы: РУССКИЙ Также Вы можете заказать международную версию программы, в которую сможете вносить информацию на ЛЮБОМ ЯЗЫКЕ мира. Даже интерфейс сможете легко перевести самостоятельно, так как все названия будут вынесены в отдельный текстовый файл.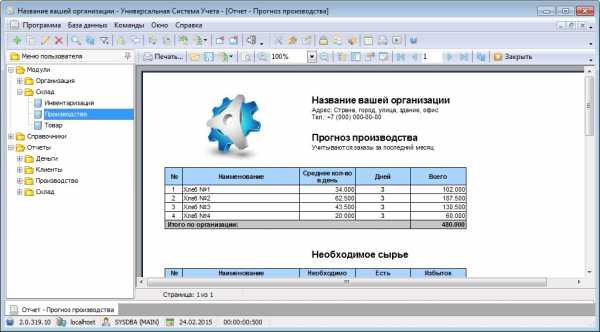
Оптимизация производства – очень важный процесс, который должен производиться на каждом производстве. Без оптимизации производства предприятие будет тратить часть своих мощностей на ненужные процедуры, и как следствие терять прибыль. Процесс оптимизации производства может отнимать очень много трудовых и финансовых ресурсов. Для облегчения этого процесса необходима программа оптимизации производства. Здесь Вам поможет УСУ (Универсальная Система Учета). Программа предоставляет широкие возможности для учета и анализа информации о Вашей фирме. Вы будете видеть, в каком количестве и на что уходят ресурсы фирмы, а также какую выгоду Вы с этого получаете. Существуют разные системы оптимизации производства. С Универсальной Системой Учета Вы можете использовать любой из них. Наша программа универсальна и может подойти любому предприятию. Вы сможете проводить оптимизацию всех жизненно-важных элементов Вашего предприятия:
Оптимизация продукции – минимизация издержек, увеличение объемов производства, облегчение и автоматизация процесса производства – лишь малая часть сложного процесса оптимизации продукции. С УСУ он станет намного легче. УСУ может наглядно продемонстрировать, сколько времени, денег и труда уходит на каждый этап производства, как это сказывается на спросе на продукцию или услугу, и сколько прибыли в итоге получает предприятие. На основании полученной информации Вы сможете проводить эффективную оптимизацию продукции и тем самым увеличивать свой доход;
Оптимизация процесса производства – этот аспект очень тесно связан с оптимизацией продукции. Универсальная Система Учета покажет, по какой цене вы покупаете сырье и материалы, сколько продукции производит каждый сотрудник, как много ресурсов затрачивается на производство единицы продукции и многое другое. Если Вам будет необходима оптимизация ресурсов в производстве, то Вы с легкостью сможете её провести. Вы будете видеть, в каких местах производство застопоривается и устранять такие места;
Оптимизация объема производства. Как много товаров производить? Это один из главных вопросов, который ставит перед любым производством современная экономика. Без правильного ответа на него Вы не сможете осуществить оптимизацию производства. С УСУ Вы получите возможность наблюдать за изменениями в спросе на Вашу продукцию и быстро подстраиваться под них, добиваясь наиболее выгодного объема производства;
Оптимизация управления производством, оптимизация работы производства. Как эффективно работают ваши сотрудники? Как много времени они тратят на каждую задачу? Ответы на все эти вопросы может предоставить Вам наша программа. Вы увидите, кто какую работу сделал за день и сколько времени на неё потратил. Также Вы сможете самостоятельно давать каждому работнику задания, чтобы максимально эффективно использовать рабочее время;
Оптимизация прибыли производства. Куда направить прибыль? Ответ на данный вопрос найти сложнее, чем может показаться на первый взгляд. Необходимо так распределить прибыль, чтобы в последствии получить её еще больше. Универсальная Система Учета покажет, какие элементы Вашего предприятия требуют дополнительных вложений, чтобы раскрыть свой потенциал;
Ассортимент продукции – оптимизация ассортимента не менее важный аспект производства. Вы должны знать, на какую продукцию спрос высокий, а на какую низкий. УСУ предоставит вам возможность вести учет реализации продукции. С такими данными Вы сможете регулировать объемы и ассортимент производства, направляя ресурсы на наиболее прибыльные направления;
Оптимизация цены продукции. Цена – первое, на что смотрят покупатели. Если цена на товар выше рыночной, то спрос на него будет очень низкий. И наоборот, если цена будет ниже рыночной, то спрос будет расти. Поэтому оптимизация стоимости продукции должна быть первоочередной задачей;
Оптимизация поставок продукции. С Универсальной Системой Учета Вы получите возможность отслеживать процесс поступления, транспортировки и отгрузки всей продукции. Программа также может предоставлять информацию о дальности маршрутов, о расходах на эти маршруты, о прибыли, которую Вы получаете от одной поездки. На основе данной информации Вы сможете наиболее эффективно распределять маршруты, минимизировав расходы и максимизировав доход.
Программой могут пользоваться:
Производственнаякомпания
Торгово-промышленнаякомпания
Производственно-промышленныекомплексы
Торговая организация
Любаяпромышленность
Любая другаяорганизация
Скачать программное обеспечение для учета на производстве
Ниже располагаются ссылки для загрузки. Скачать бесплатно можно презентацию программного обеспечения в формате PowerPoint и демонстрационную версию. Причем, демо-версия имеет определенные ограничения: по времени использования и функционалу.
Есть вопросы по демо-версии?Наша служба технической поддержки Вам поможет!Напишите или позвоните нам. Контакты здесь.Скачать программное обеспечение для учета на производстве
Ниже располагаются ссылки для загрузки. Скачать бесплатно можно презентацию программного обеспечения в формате PowerPoint и демонстрационную версию. Причем, демо-версия имеет определенные ограничения: по времени использования и функционалу.
Есть вопросы по демо-версии?Наша служба технической поддержки Вам поможет!Напишите или позвоните нам. Контакты здесь.Скачать программное обеспечение для учета на производстве
Ниже располагаются ссылки для загрузки. Скачать бесплатно можно презентацию программного обеспечения в формате PowerPoint и демонстрационную версию. Причем, демо-версия имеет определенные ограничения: по времени использования и функционалу.
Есть вопросы по демо-версии?Наша служба технической поддержки Вам поможет!Напишите или позвоните нам. Контакты здесь.Скачать программное обеспечение для учета на производстве
Ниже располагаются ссылки для загрузки. Скачать бесплатно можно презентацию программного обеспечения в формате PowerPoint и демонстрационную версию. Причем, демо-версия имеет определенные ограничения: по времени использования и функционалу.
Есть вопросы по демо-версии?Наша служба технической поддержки Вам поможет!Напишите или позвоните нам. Контакты здесь.Возможности контроля и управления оптимизацией производства
Далее представлен краткий перечень возможностей программы Универсальная Система Учета. В зависимости от конфигурации разработанного программного обеспечения список возможностей может меняться.
- Одна программа, в которой учитывается весь производственный процесс;
- Единая база для поставщиков с возможностями сортировки по любым показателям;
- Единая база для клиентов, в которой также можно настроить сортировку;
- Подробные и наглядные отчеты, которые удобно использовать для любых задач;
- Прогнозные отчеты, построенные на фактических данных – чтобы Вы всегда знали, что может Вас ждать;
- Оформление новой первичной документации в едином стандартизированном виде;
- Все документы будут именными, что значит Вам не надо будет каждый раз заново вводить реквизиты. Введите их один раз, а затем УСУ будет вставлять их автоматически, что значительно ускорит процесс документооборота;
- Единая база для всех документов;
- Полная автоматизация всех расчетов, что снижает до минимума вероятность ошибки из-за человеческого фактора;
- Получение документов на любую дату за считанные секунды;
- Универсальность программы. Неважно, каким видом деятельности Вы занимаетесь, УСУ подойдет Вам;
- Модификации программы. Нужна нестандартная функция? Мы модифицируем и подстроим Универсальную Систему Учета под именно под Ваши нужды;
- Простой и понятный интерфейс, на изучение и внедрение которой Вы потратите очень мало времени;
- Калькуляция продукции, расчет как для единицы, так и для партии;
- Постоянное статистическое наблюдение за производством
Презентация программы для управления производством
Заказать автоматизацию производства
Чтобы приобрести данную программу, достаточно позвонить нам по указанным в контактных данных телефонам или скайпу, либо просто написать письмо. Наши специалисты согласуют с Вами подходящую конфигурацию, подготовят договор и счет на оплату.
Смотрите также:
usu.kz
Оптимизация операций на производстве: magician_roman
Когда возникает вопрос оптимизации операций выполняемых работником на производстве, мировая практика использует два метода:1) Заинтересовать самого работника оптимизировать свою работу2) Собрать комиссию / пригласить эксперта для анализаВ мировой практике оба метода весьма действенны, в Японии благодаря кайдзенгу стимулируют оптимизацию силами самих работников - ведь кто лучше всего знает свои обязанности и проблемные места производства и заинтересован в облегчении своего труда - конечно же работник. К тому же это позволяет экономить на экспертах.
В Европе наоборот преобладает принцип приглашения экспертов, которым в принципе на желания работников плевать - их цель создать рабочий и оптимальный механизм на основе стандартов операций в отрасли. Работник видит только свой участок, эксперт видит производство в целом.
А в России... оба метода не работают :) Очень хорошо я об этом когда-то написал в старом посту: Реалии внедрения бережливого производства и собственно до сих пор актуально.
Но лучше расскажу об этих методах у нас. Начнем с первого: заинтересовать работника самому оптимизировать свою работу.
Ну во-первых это работникам практически никто не предлагает, а если и предлагают, то все случается как в посту Что иногда мешает получать предложения по улучшению - это хорошо если систему перестраивают не только на деле, но и в мозгах руководства. Во-вторых - а вот боится наш человек что-то менять, тут действует инстинктивное чувство русского народа "любые изменения приносят проблемы лично для работника" (запомним эту мысль, мы еще к ней вернемся) - это обычно выражается фразами "да нормально все" или "да мы так и работали всегда". И ты им хоть деньгами сули, хоть угрожай - все равно один фиг. Ну тут еще любят вспомнить про зону комфорта, мол ну нравится и привычно человеку 3 дня в Экселе считать, чем сделать одну кнопку и выйти из своей зоны комфорта (хотя эта кнопочка потом вполне может стать новой зоной комфорта). Есть у нашего человека еще одно оправдание не оптимизировать свою работу - мол делать буду больше, а получать так же - на самом деле весьма и весьма часто встречается. Ну еще люди в районе 40 просто боятся что если они оптимизируют свое место, то эту работу сможет выполнять кто-то еще, а их попросят, а у них семья - ну вообщем поняли.
Вообщем нашего работника просто так свою работу упростить заставить сложно. Ну теперь посмотрим приглашение эксперта.
Ну... вы не поверите их мало кто из руководства приглашает, причин две: дорого и у нас уникальная компания со своими уникальными бизнес-процессами. Последнее про уникальность мне сразу напомнило мой другой пост: Блокнотик: о стоимости разработки ПО. Хорошо, даже если пригласили, то экспертов ждет много сюрпризов - начнем с того, что на них сразу смотрят как на врагов, и уж точно не горят им раскрывать свои процессы и как работают, хотя после "кнута" руководства и вынуждены идти на сотрудничество.
Опытные эксперты знают, что интервью (расспрос работника) практически не привносит полезной информации, но все равно его проводят, цель в принципе наладить контакт и чтоб работники привыкли к новой морде. Самое интересное можно почерпнуть только во время самого производства, вот почему хороший эксперт предпочитает пару дней походить по цехам и просто наблюдая работу, и самые ценные наблюдения получаются в первый и последний день. В первый день видно моменты когда работник замешкается (а это значит в этот момент, боясь наблюдающего эксперта, он делает что-то не так как обычно - по правилам, по стандартам), в последний день работник уже привыкает к ходящему эксперту и не обращает на него внимания и вполне может делать операции как привык. Минимальное время наблюдения 3 дня, оптимальное неделя.
К слову, мне нравятся оба метода, ибо каждый имеет недостатки. Реальные результаты у нас, иногда показывает участии экспертов - дело в том, что даже если работник заинтересован в оптимизации своей работы - у него работает шаблонное мышление, иногда человек просто не может подумать о том, что можно делать иначе. Эксперт же может показать и рассказать о других методах. Но тот же самый эксперт будь он хоть пяти прядей во лбу может не знать тонкости отдельных операций - ну не возможно все знать.
Ну и вопрос о сотрудничестве и вообще анализе весьма сложноват. Но вот буквально вчера попалась интересная наработка американской компании, информации о ней ну вот по сути ноль, видимо они считают это своим ноу-хау (наивные), вообщем они предлагают надевать на работников такой вот бейдж:
В нем камера, микрофон, акселерометр и какие-то еще датчики - вообщем работник выполняет свою работу, а машинка все это пишет, а потом значит на основе этих данных анализируют как можно оптимизировать процессы. На самом деле мне идея весьма понравилась как таковая, с учетом реальных данных по перемещениям, словам и записи действий (с возможностью на основе этого делать тайминг по времени на операцию) можно делать куда более точные расчеты по вариантам изменения - строить модели и просчитывать эффективность. Так что если кто из моих френдов занимается бережливым производством - то вполне может взять себе это на вооружение, ну а технические возможности уже считай имеются - камеры пошли миниатюрные.
magician-roman.livejournal.com