Оптимизация критически важных узлов с использованием Fluent Adjoint Solver. Оптимизация ansys
Оптимизация упрощенной конструкции шатуна в Ansys
Published on27-Jul-2015
View205
Download2
Transcript
Рехтер Александр Дантонович, ТОО “Альбион”, тел.(0852) 27-45-51 E-mail [email protected] Оптимизация упрощенной конструкции шатуна с помощью ANSYS 5.4 1. ЦЕЛЬ РАСЧЕТА. Подбор оптимального соотношения размеров упрощенной модели шатуна, обеспечивающих снижение эквивалентных напряжений при минимальном весе конструкции. 2. ОПИСАНИЕ КОНЕЧНО-ЭЛЕМЕНТНОЙ МОДЕЛИ (КЭМ). Вследствие симметрии рассматривается только половина конструкции. С точки зрения геометрии модель включает нижнюю и верхнюю головку в виде полуколец, соединенных ребром толщиной T3 и стенкой толщиной T4. Кроме параметров толщин T3 и T4 модель шатуна (см. рис.1) включает еще 6 конструкторских параметров (DS1, DS2, AL11, DAL1, AL21, DAL2), которые в процессе оптимизации варьируются в пределах заданных ограничений. Моделируется нагружение от действия на шатун газовой силы. Для упрощения принимается, что на нижнюю и верхнюю головку действует равномерное давление в пределах дуги 60°. Давления подобраны так чтобы суммарная нагрузка, действующая на верхнюю головку, была равна суммарной силе, действующей на нижнюю головку. Закрепление узлов в направлении оси X обеспечивает условие симметрии. Один из узлов закрепляется в направлении оси Y для компенсации небольшой разницы в суммарных нагрузках, действующих на нижнюю и верхнюю головку. КЭМ рассчитывает плоско-напряженное состояние модели шатуна. Она состоит из 280 элементов типа PLANE42. Использовалась регулярная схема разбиения. Материал модели сталь с коэффициентом Юнга 20 000 кг/кв.мм и коэффициентом Пуассона – 0,28. Ниже все размеры определены в мм. Давление в кг/кв.мм. 3. ОПИСАНИЕ МЕТОДА ОПТИМИЗАЦИИ. Основным вопросом оптимизации является ориентация ребра жесткости и толщина перемычки между ребрами Не все методы оптимизации дают одинаково хорошие результаты. В данном случае наилучшие результаты дал метод первого порядка FIRST. В тексте пакетного файла заданы ограничения на параметры конструкции и переменную состояния. В качестве переменной состояния использовалось эквивалентное напряжение, соответствующее критерию Мизеса. Минимизируемой объектной переменной являлся вес конструкции. Расчет проводился с помощью Ansys 5.4/ED. Представительство CAD FEM GmbH в СНГ: 107497 Москва, Щелковское шоссе, 77, офис 1703 Тел.: (095) 468-8175 Тел.\факс: (095) 913-2300 e-mail: [email protected] http://www.cadfem.ru 1 Рехтер Александр Дантонович, ТОО “Альбион”, тел.(0852) 27-45-51 4. ЭТАПЫ РЕШЕНИЯ ЗАДАЧИ. Подготовка модели Заголовок задачи Инициализация параметров для построения геометрии модели. Выбор типа расчета Выбор типа и параметров элементов. Определение свойств материала. Задание констант. Построение верхней головки шатуна. Построение нижней головки. Построение ребра. Формирование областей. Определение параметров разбиения. Разбиение модели. Закрепление узлов. Приложение давления к нижней головке. Приложение давления к верхней головке E-mail [email protected] 1. 2. 3. 4. 5. 6. 7. 8. 9. 10. 11. 12. 13. 14. 15. 3. 4. Расчет. 16. Решение модели с заданными граничными условиями. Постпроцессор 17. Определение суммарного объема модели; 18. Определение максимального эквивалентного напряжения. Оптимизация модели 19. Задание геометрических параметров. 20. Задание переменной состояния. 21. Задание целевой функции. 22. Задание метода оптимизации. 23. Назначение рабочего файла . 24. Запуск процесса оптимизации. 25. Анализ полученных результатов. Далее в тексте кнопки, клавиши, пункты меню и выбираемые строки в списках Ansys показаны жирным шрифтом, вводимые с клавиатуры величины даны курсивом 7. ПРОТОКОЛ РЕШЕНИЯ. Подготовка модели. Заголовок задачи. U_M: File ⇒ Change Title 1.1. Наберите заголовок «Piston rod optimization.» 1.2. ОК 2. Инициализация параметров для построения геометрии модели. U_M: Parameters ⇒ Scalar Parameters 2.1. В появившемся окне ввести имена и значения переменных (после набора одной переменной – Enter). DS1=10 DS2=10 T3=30 T4=7 AL11=235 DAL1=10 1. 5. 6. AL21=105 DAL2=10 Для упрощения последующей записи далее вводятся соотношения. AL12=AL11+DAL1 AL22=AL21+DAL2 2.2 Close Выбор типа расчета: M_M:Preprocessor ⇒ Loads ⇒ New Analysis. Включаем кнопку Static и затем OK. Выбор типа и параметров элементов: M_M:Preprocessor ⇒ Element Type ⇒ Add/Edit/Delete. 4.1. Add (добавить новый тип элемента) 4.2. Выберите Quad 4 node 42 (PLANE 42) 4.3. OK 4.4. Options (параметры элемента) 4.5. В списке K3 смените тип анализа с Plane stress на Plane stress w/thk (плосконапряженное состояние с учетом толщины элемента) 4.6. OK 4.7. Нажмите Close в предыдущем окне. Определение свойств материала: M_M:Preprocessor ⇒ Material Props ⇒ Isotropic. 5.1. Ввести номер набора свойств материала 1 и нажмите OK 5.2. Задайте модуль Юнга в поле EX 20 000 5.3. Задать коэффициент Пуассона в поле NUXY 0.28. Нажмите OK Задание констант: M_M:Preprocessor ⇒ Real Constant ⇒ Add/Edit/Delete. 6.1. Add (добавить набор констант) 6.2. OK (в окне выбора типа элемента)Выберите PLANE 42 6.3. Вводим номер набора свойств 1 и толщину элементов 30 для данного набора 6.4. Apply 6.5. Соответственно вводим номер набора 2 и толщину 30 6.6 Apply 6.7 Вводим номер набора 3 и толщину T3 6.8 Apply 6.9 Вводим номер набора 4 и толщину T4 6.10 OK 6.11 Close Построение верхней головки шатуна: 7.1. Создание точки в центре головки: M_M:Preprocessor ⇒ Create ⇒ Keypoints ⇒ In Active CS 7.2. Ввести в поле NPT номер точки 1, в поле X, Y, Z координаты 0,0,0. 7.3. OK 7.4.Перейти к цилиндрической системе координат с центром в точке 0,0,0: 7. Представительство CAD FEM GmbH в СНГ: 107497 Москва, Щелковское шоссе, 77, офис 1703 Тел.: (095) 468-8175 Тел.\факс: (095) 913-2300 e-mail: [email protected] http://www.cadfem.ru 2 Рехтер Александр Дантонович, ТОО “Альбион”, тел.(0852) 27-45-51 U_M:Work Plane ⇒ Change Active CS to ⇒ Global Cylindrical 7.5 Ввод координат опорных точек: M_M:Preprocessor ⇒ Create ⇒ Keypoints ⇒ In Active CS.Последовательно ввести в диалоговом окне номер точки и ее координаты в текущей цилиндрической системе координат. Первая координата – радиус точки, вторая – угол. После каждого ввода нажмите Apply, после последнего ОК. 25,90; Apply 25,180; Apply 25,270; Apply 25+DS1,90; Apply 25+DS1,180; Apply 25+DS1,AL11; Apply 25+DS1,AL12; Apply 25+DS1,270. OK 7.6 Формирование дуг:: M_M:Preprocessor ⇒ Create ⇒ Arcs ⇒ By End KPs & Rad Укажите курсором конечные точки дуги и нажмите OK, затем точку центра дуги и ОК, в последнем окне ввести радиус дуги и Apply. Последовательно для каждой дуги укажите: 3,2 (кон. т.) 1 (т. центра) 25 (радиус) 3,4 1 25 6,5 1 25+DS1 6,7 1 25+DS1 7,8 1 25+DS1 8,9 1 25+DS1 OK 7.7 Формирование прямых линий: M_M:Preprocessor ⇒ Create ⇒ Lines ⇒Straight Line. Последовательно для каждой линии укажите курсором начальную и конечную точки. 2 (нач. т.), 5 (кон. т.) 4, 9 OK Построение нижней головки шатуна: 8.1 Перейти к новой цилиндрической системе координат с началом в центре нижней головки:: U_M:Work Plane ⇒ Local Coordinate Systems ⇒ Create Local CS. ⇒ At Specified Loc. В окне ANSYS Input ввести координаты начала новой системы в глобальной системе 0,-250,0. OK. В следующем диалоговом окне ввести в поле KCN (номер системы) - 11, а в поле KCS (тип системы) выбрать Cylindrical. OK. 8.2. Устанавливаем новую систему координат текущей:: U_M:Work Plane ⇒ Change Active CS to ⇒ Specified Coord Sys. В поле KCN вводим 11. OK. 8.3. Ввод координат опорных точек: M_M:Preprocessor ⇒ Create ⇒ Keypoints ⇒ In Active CS. Последовательно ввести в диалоговом окне номер точки и ее координаты в текущей цилиндрической системе координат. E-mail [email protected] 2 3 4 5 6 7 8 9 8. Первая координата – радиус точки, вторая – угол. После каждого ввода нажмите Apply, после последнего ОК. 10 0,0; Apply 11 45,90; Apply 12 45,180; Apply 13 45,270; Apply 14 45+DS2,90; Apply 15 45+DS2,AL21; Apply 16 45+DS2,AL22; Apply 17 45+DS2,180; Apply 18 45+DS2,270. OK 8.4 Формирование дуг: M_M:Preprocessor ⇒ Create ⇒ Arcs ⇒ By End KPs & Rad Укажите курсором конечные точки дуги и нажмите OK, затем точку центра дуги и ОК, в последнем окне ввести радиус дуги и Apply. Последовательно для каждой дуги укажите: 11,12 (кон. т.) 10 (т. ц.) 45 (рад.) Apply 12,13 10 45 Apply 14,15 10 45+DS2 Apply 15,16 10 45+DS2 Apply 16,17 10 45+DS2 Apply 17,18 10 45+DS2 OK 8.5 Формирование прямых линий: M_M:Preprocessor ⇒ Create ⇒ Lines ⇒Straight Line. Последовательно для каждой линии укажите курсором начальную и конечную точки. 11 (нач. т.), 14 (кон. т.) 13, 18 OK 9. Построение ребра: M_M:Preprocessor ⇒ Create ⇒ Lines ⇒Straight Line. Последовательно для каждой линии укажите курсором начальную и конечную точки. 7 (нач. т.), 16 (кон. т.) 8, 15 9, 14 OK 10. Формирование областей: M_M:Preprocessor ⇒ Create ⇒ Arbitrary ⇒ By Lines. Последовательно укажите курсором для каждой области образующие ее линии. : L1, L2, L8, L6, L5, L4, L3, L7 Apply L9, L10, L16, L14, L13, L12, L11, L15 Apply L5, L17, L12, L18 Apply L11, L18, L6, L19 OK. 11. Определение параметров разбиения.: M_M:Preprocessor ⇒ Size Cntrls ⇒ Picked Lines. Последовательно указывайте на экране по одной линии и затем OK. В следующем диалоговом окне задайте параметры NDIV (число делений) и SPACE ( сгущение) . Знак минус для SPACE указывает на сгущение к концу линии, плюс – к началу. L5 NDIV = 3 SPACE = 1 Apply L6 NDIV = 3 SPACE = 1 Apply Представительство CAD FEM GmbH в СНГ: 107497 Москва, Щелковское шоссе, 77, офис 1703 Тел.: (095) 468-8175 Тел.\факс: (095) 913-2300 e-mail: [email protected] http://www.cadfem.ru 3 Рехтер Александр Дантонович, ТОО “Альбион”, тел.(0852) 27-45-51 E-mail [email protected] 13.1 Выбор линий для закрепления узлов в L15 NDIV = 4 SPACE = 1 Apply направлении оси X. U_M:Select ⇒ Entities L8 NDIV = 4 SPACE = 1 Apply В верхнем списке диалогового окна L18 NDIV = 12 SPACE = 1 Apply выберите тип примитива Lines, в нижнем L4 NDIV = 8, SPACE = -2 Apply списке укажите способ выбора By L3 NDIV = 8, SPACE = 2 Apply Num/Pick и нажмите OK. Укажите L13 NDIV = 12, SPACE = 2 Apply курсором L7, L8, L15, L16, L19 и нажмите L14 NDIV = 12, SPACE = 2 Apply OK. L9 NDIV = 18, SPACE = 2 Apply 13.2 Привязка узлов к выбранным линиям. L10 NDIV = 12, SPACE = 2 OK U_M:Select ⇒ Entities . В верхнем списке 12. Разбиение модели. диалогового окна выберите тип примитива 12.1 Для генерации регулярной элементной Nodes, в нижнем – Attached to и включите сетки разбиваемые области должны переключатель Lines, all. Нажмите OK. включать не более 4 линий. Поскольку 13.3. Задание направления закрепления для (см. п. 10) первая и вторая область выбранных узлов. M_M: Preprocessor ⇒ включали более 4 линий необходимо Loads ⇒ Apply ⇒ Displacement ⇒ On провести их слияние (конкатенацию). Nodes. Нажмите Pick All, в следующем M_M: Preprocessor ⇒ Concatenate ⇒ окне выберите направление закрепления Lines. Последовательно укажите курсором UX и нажмите OK объединяемые линии и нажимайте 13.4. Возврат в набор всех линий модели.. клавишу Apply, для последней линии ОК. U_M:Select ⇒ Entities . В верхнем списке L3, L4, L5, L6 Apply выберите тип примитива Lines, в нижнем L1, L2 Apply способ выбора By Num/Pick, кнопка Full L11, L12, L13, L14 Apply должна быть включена и затем OK. В L9, L10 OK. следующем окне нажмите Pick All. 12.2. Задание признака регулярного разбиения. 13.5. Возврат в набор всех узлов модели.. M_M: Preprocessor ⇒ Mesher Opts U_M:Select ⇒ Entities . В верхнем списке В диалоговом окне включите выберите тип примитива Nodes, в нижнем переключатель Mapped и нажмите OK. В способ выбора By Num/Pick, кнопка Full следующем диалоговом окне выберите из должна быть включена и затем OK. В списка 2D Shape строку Quad следующем окне нажмите Pick All. (четырехугольный элемент) и нажмите OK. 13.6. Закрепление одного из узлов в 12.3. Задание набора констант для первой направлении оси Y.. M_M: Preprocessor ⇒ области. Loads ⇒ Apply ⇒ Displacement ⇒ On . M_M: Preprocessor ⇒ Create ⇒ Elements Nodes. Выберите курсором один из узлов ⇒ Elem Atributes на стержне шатуна и затем OK. В В диалоговом окне из списка REAL следующем окне задайте направление выберите 1 и нажмите OK. закрепления UY и нажмите OK 12.4. Разбиение первой области. 14. Приложение давления к нижней головке . M_M: Preprocessor ⇒ Mesh ⇒ Mapped ⇒ 14.1 Выбор узлов лежащих на дуге радиуса 45 3 or 4 sided. Затем укажите курсором мм в пределах изменения угла от 90° до первую область и нажмите OK. 150°. U_M:Select ⇒ Entities. В верхнем 12.5. Задание набора констант для второй списке выберите тип примитива Nodes , в области.Aналогично п.12.3 с указанием нижнем способ выбора By Location. параметра REAL = 2. Включите кнопку From Full.и X. В поле 12.6. Разбиение второй области. ввода MIN, MAX введите радиус Аналогично п. 12.4 c указанием второй размещения узлов 45 и нажмите Apply. области. Включите кнопку Reselect и Y. В поле 12.7. Задание набора констант для третьей MIN, MAX введите 90, 150 и нажмите OK. области.Aналогично п.12.3 с указанием 14.2. Задание величины давления. M_M: параметра REAL = 3. Preprocessor ⇒ Loads ⇒ Apply ⇒ 12.8. Разбиение третьей области. Pressure ⇒ On Nodes. Нажмите Pick All и Аналогично п. 12.4 c указанием третьей в следующем окне введите в поле Value области. 4.95 и нажмите OK 12.9. Задание набора констант для четвертой 14.3. .Возврат в набор всех узлов модели.. области.Aналогично п.12.3 с указанием параметра REAL = 4. U_M:Select ⇒ Entities . В верхнем списке 12.10. Разбиение четвертой области. выберите тип примитива Nodes, в нижнем Аналогично п. 12.4 c указанием четвертой By Num/Pick, кнопка Full должна быть области. включена, и нажмите OK. В следующем 13. Закрепление узлов. окне нажмите Pick All. 4 Представительство CAD FEM GmbH в СНГ: 107497 Москва, Щелковское шоссе, 77, офис 1703 Тел.: (095) 468-8175 Тел.\факс: (095) 913-2300 e-mail: [email protected] http://www.cadfem.ru 15. 16. 17. 18. Рехтер Александр Дантонович, ТОО “Альбион”, тел.(0852) 27-45-51 E-mail [email protected] SEQV и нажмите OK. Закройте Приложение давления к верхней головке предыдущее окно нажатием на Close. 15.1. Активизация глобальной 18.2 Сортировка напряжений. M_M:General цилиндрической системы координат. Postproc ⇒ List Results ⇒ Sort Elems. (начало координат в центре верхней Введите имя сортируемой таблицы S_EQV головки). U_M:Work Plane ⇒ Change и нажмите OK. 18.3 Присвоение переменной S_EQVMAX Active CS to ⇒ Global Cylindrical максимального значения эквивалентных 15.2 Выбор узлов лежащих на дуге радиуса 25 напряжений. U_M:Parameters ⇒ Get в пределах изменения угла от 210° до 270°. Scalar Data. В левом списке диалогового U_M:Select ⇒ Entities. В верхнем списке окна выбрать строку Results data, в выберите тип примитива Nodes , в нижнем правом – Other operations и нажмите OK. способ выбора By Location. Включите В следующем диалоговом окне ввести кнопку From Full.и X. В поле ввода MIN, имя параметра максимального MAX введите радиус размещения узлов 25 эквивалентного напряжения S_EQVMAX, и нажмите Apply. Включите кнопку в левом списке выберите строку From Reselect и Y. В поле MIN, MAX введите sort oper, в правом - Maximum value и 210, 270 и нажмите OK. OK. 15.3. Задание величины давления. M_M: Оптимизация модели Preprocessor ⇒ Loads ⇒ Apply⇒ Pressure 19. Задание геометрических параметров. ⇒ On Nodes. Нажмите Pick All и в M_M:Design Opt ⇒ Design Variables. В следующем окне введите в поле Value 8.90 диалоговом окне нажмите клавишу Add. В и нажмите OK. следующем окне последовательно выбирайте 15.4. Возврат в набор всех узлов модели.. из списка Name имена переменных, в поле U_M:Select ⇒ Entities. В верхнем списке MIN ввести левую границу диапазона выберите тип примитива Nodes, кнопка переменной, в поле MAX – правую границу. Full должна быть включена и затем OK. В После каждого ввода нажимайте Apply. Ниже следующем окне нажмите Pick All. в скобках указаны параметры для которых Расчет модели вводится левая и правая граница диапазона. Решение модели с заданными граничными 8 условиями. M_M:Solution ⇒ Current LS 20 Apply (DS1) Постпроцессор 8 Определение суммарного объема модели. 20 Apply (DS2) 17.1. Формирование таблицы объемов 15 элементов.M_M:General Postproc ⇒ 30 Apply (T3) Element Table ⇒ Define Table. Нажмите 5 Add. В следующем диалоговом окне 30 Apply (T4) верхнем поле введите имя таблицы VOLU, 225 ниже из левого списка выберите строку 250 Apply (AL11) Geometry, из правого – Elem volume 2 VOLU и нажмите OK. Закройте 20 Apply (DAL1) предыдущее окно нажатием на Close. 100 17.2 Суммирование объемов. M_M:General 120 Apply (AL21) Postproc ⇒ Element Table ⇒ Sum of Each 2 Item. Нажмите OK. 20 OK (DAL2) 17.3 Присвоение переменной суммарного Закройте предыдущее окно нажатием объема. U_M:Parameters ⇒ Get Scalar Close. Data. В левом списке диалогового окна 20. Задание переменной состояния . M_M:Design выбрать строку Results data, в правом – Opt ⇒ State Variables. В диалоговом окне Elem table sums и нажмите OK. В нажмите клавишу Add. В следующем окне следующем диалоговом окне ввести имя выберите параметр S_EQVMAX и введите в параметра суммарного объема TVOL и поле MAX его максимальное значение 25. OK. Нажмите OK. Закройте предыдущее окно Определение максимального эквивалентного нажатием Close. напряжения . 21. Задание целевой функции. M_M:Design Opt ⇒ 18.1 Формирование таблицы эквивалентных Objective. Выберите параметр TVOL. Нажмите напряжений по Мизесу. .M_M:General OK. Postproc ⇒ Element Table ⇒ Define Table. Нажмите Add. В следующем диалоговом окне в верхнем поле введите имя таблицы S_EQV, ниже из левого списка выберите строку Stress, из правого – von Mises Представительство CAD FEM GmbH в СНГ: 107497 Москва, Щелковское шоссе, 77, офис 1703 Тел.: (095) 468-8175 Тел.\факс: (095) 913-2300 e-mail: [email protected] http://www.cadfem.ru 5 Рехтер Александр Дантонович, ТОО “Альбион”, тел.(0852) 27-45-51 E-mail [email protected] 22. Задание метода оптимизации. M_M:Design 24. Запуск процесса оптимизации. M_M:Design Opt ⇒ Method/Tool. Включите кнопку First Opt ⇒ Run . -Order и нажмите OK. (First-Order относится к 25. Просмотр полученных результатов. U_M: методам оптимизации первого порядка). В Parameters ⇒ Scalar Parameters. Ansys следующем окне в поле NITR введите число выводит информационное окно с номером итераций 10, остальные параметры по наилучшего набора параметров. В описанном умолчанию. и нажмите OK. примере сходимость была достигнута на 6 23. M_M:Design Opt ⇒ Assign. Назначение итерации, время расчета на машине с рабочего файла. Проведение оптимизации в процессором Pentium 120 Mhz составило 5162 интерактивном режиме требует рабочего сек. При этом эквивалентные напряжения файла. Им может быть протокол сеанса работы снизились до 27, 836 кг/кв.мм, объем (файл с расширением log). Возможно увеличился до 134202 куб.мм. Остальные потребуется его правка. При правке удаляются параметры приняли следующие значения лишние команды (напр., команды просмотра, (DS1=9.4, DS2=11.9, T3=29.6, T4=5.0, выдачи вспомогательной печати и т.д.). AL11=234.7, DAL1=9.8, AL21=108.3, Выберите из списка файл с расширением log и DAL2=11.4) нажмите OK. Рис.2 Эквивалентные напряжения до оптимизации (максимальное значение 47,551 кг/кв.мм) Рис.3 Эквивалентные напряжения после оптимизации (максимальное значение 27,836 кг/кв.мм) Представительство CAD FEM GmbH в СНГ: 107497 Москва, Щелковское шоссе, 77, офис 1703 Тел.: (095) 468-8175 Тел.\факс: (095) 913-2300 e-mail: [email protected] http://www.cadfem.ru 6
docslide.net
Оптимизация критически важных узлов с использованием Fluent Adjoint Solver
Оптимизация изделий, которые должны вписываться в ограниченное пространство, может быть сложной задачей, даже для самого опытного конструктора. Рассмотрим систему ОВК (отопления, вентиляции и кондиционирования воздуха) автомобиля, которая осуществляет подачу воздуха в кабину транспортного средства. Так как на сегодняшний день система кондиционирования воздуха считается стандартным оборудованием даже для автомобилей начального класса, то производителям необходимо учитывать все её геометрические особенности для правильной установки данной системы в ограниченном пространстве. К критически важным узлам относятся воздуховоды, которые располагаются под капотом автомобиля в условиях плотной компоновки двигателя, радиатора, аккумулятора, коробки передач и вспомогательных агрегатов. Но под капотом не так много места и это лишь одна из проблем.
Автомобильные конструкторы должны поместит ОВК-систему в ограниченное пространство, сохраняя или даже улучшая её производительность. Изображение предоставлено Beaudaniels.com
Помимо плотной компоновки, инженеры-конструкторы должны оптимизировать общий расход воздуха для того, чтобы ОВК-система соответствовала конкретным требованиям. Во-первых, в машину должно поступать достаточное количество воздуха. Во-вторых, поступающий воздушный поток, должен быть равномерным, чтобы пассажиры на задних сиденьях чувствовали себя комфортно. Кроме того, исходя из требований потребителей, производителей и контролирующих организаций, ОВК-система должна быть энергоэффективной. Проектно-расчетным группам необходимо в кратчайшие сроки разрабатывать высокопроизводительные изделия, на производство которых будет затрачено как можно меньше ресурсов. Другими словами, необходимо разработать систему, которая сработает с первого раза.
В результате инженеры должны разработать правильную геометрию воздуховода, чтобы вписаться в ограниченное пространство под капотом автомобиля и минимизировать падение давления для обеспечения надлежащего распределения потока. Кроме того, уменьшение перепада давления через воздуховод между входом и выходом может уменьшить потребление энергии, а повышение равномерности потока помогает обеспечивать циркуляцию воздуха по всему салону автомобиля.
Когда-то инженеры-конструкторы использовали трудоемкие методы проб и ошибок для оптимизации воздуховодов, геометрическая форма которых может быть чрезвычайно сложной и управляться сотнями параметров (или более). Естественно, рассмотреть их все физически невозможно. Как убедиться в том, что вы выбрали подходящие параметры? Даже если вы выбрали только один набор ключевых параметров, определяющих форму конструкции, вы все еще имеете очень большое количество вариантов конструкции для оценки производительности. Следовательно, такой подход не очень эффективен, поскольку проектная группа должна создать геометрию и сетку, выполнить множество тестов, проанализировать обратную связь, создать новую геометрию и сетку, затем сделать ещё большее количество тестов, и повторить цикл, чтобы найти оптимальное решение и, возможно, это решение не будет лучшим и, вероятно, продукт не удастся запустить в срок.
Когда заказчики, занимающиеся автомобильной тематикой, сказали ANSYS, что они устали угадывать геометрические параметры и перебирать сотни расчетных точек, разработчики решили создать систему моделирования, которая бы автоматизировала изучение динамики стесненных течений. Благодаря совместной работе Min Xu (разработчик программных продуктов ANSYS, в том числе модуля Adjoint Solver) и Chris Hill (ведущий специалист подразделения ANSYS по развитию продуктов вычислительной гидрогазодинамики) удалось разработать программный продукт, который использует технологию морфинга сеточной модели. Данная технология дает быстрое и конкретное представление о поиске идеальных решений для задач, в которых необходимо снизить перепад давления.
После преодоления ряда технических трудностей и удовлетворения всех требований заказчика, разработчики решили внедрить данную технологию повсеместно, так как у компании ANSYS была уверенность в том, что новая технология морфинга сетки может положительно повлиять на процесс проектирования во многих организациях и в ряде отраслей промышленности.
Решатель ANSYS Adjoint Solver позволяет автоматически осуществлять улучшение конструкции и изменять сеточную модель для обеспечения более оптимальной формы геометрии и повышения производительности изделия. Для того, что произвести оптимизацию необходиом импортировать STL-файл, определяющий реальное физическое пространство, в котором будет находится исследуемый объект. Данный файл вы можете легко создать в CAD-пакете, сеточном генераторе или другой системе проектирования. В Adjoint Solver после задания ограничивающего пространства можно определить какие области являются наиболее чувствительными к результатам, к которым вы стремитесь, а какие области не оказывают существенного воздействия на результаты расчета.
В нижнем примере, общий перепад давления вдоль выпускного коллектора минимизируется путем изменения геометрии коллектора, а также снижается неравномерность потока. Геометрия коллектора может изменяться в пределах сложной ограничивающей поверхности, которая определяется импортированной сеткой, в то время как входной и выходной участки зафиксированы. В данном случае, ANSYS Adjoint Solver снизил общий перепад давления вдоль коллектора между входным и выходным участками на 75% и повысил равномерность потока на выходной границе на 45% за 50 итераций.
Снижение общего перепада давления (левая вертикальная ось и квадратные маркеры) и изменение массового расхода на выходе (правая вертикальная ось и треугольные маркеры) в течении 50 итераций.
Геометрия коллектора и ограничивающая поверхность (прозрачно-зеленая)
Линии тока окрашены по давлению. Отсутствие зоны рециркуляции предполагает более эффективное перемещение потока.
В заключении хотелось бы сказать, что компания ПЛМ Урал приглашает вас на вебинар, посвящённый использованию модуля топологической оптимизации ANSYS Adjoint Solver, который пройдет 24 октября 2017 г. в 13:00 по МСК. Для регистрации на вебинаре необходимо перейти по ссылке.
Подробнее о содержании вебинара вы можете прочитать в анонсе.
Как вы считаете, является ли технология Adjoint Solver перспективной? Может ли она заменить традиционный подход параметрической оптимизации?
Оригинальный текст статьи: http://www.ansys-blog.com/critical-components-adjoint-solver/
cae-club.ru
Этапы оптимизации конструкций в ANSYS
Оптимизации конструкций в ANSYS
Новая высокоэффективная технология многокритериальной оптимизации IOSO (Indirect Optimization on the base of SelfOrganization; автор — д.т.н., профессор И. Егоров) от компании «Сигма Технология» базируется на собственных оригинальных методах и алгоритмах оптимизации, дающих возможность выполнить сложные задачи поиска оптимума, которые ранее не решались ввиду отсутствия эффективного метода. Стратегия решения задач оптимизации принципиально отличается от известных подходов нелинейного программирования, обладает более высокой эффективностью и обеспечивает существенно более широкие возможности. В соответствии с логикой работы алгоритмов IOSO на каждой итерации осуществляется построение поверхностей отклика критериев оптимизации и ограничиваемых параметров. Далее выполняется оптимизация с использованием полученных поверхностей отклика и в найденной точке проводится прямое обращение к математической модели исследуемой системы. В процессе оптимизации осуществляется накопление информации об исследуемой системе в окрестности оптимального решения, что приводит к повышению качества поверхностей отклика. В данной статье мы рассмотрим процесс нахождения оптимальной конструкции металлической башни при помощи программного обеспечения ANSYS и алгоритмов оптимизации IOSO. Целью оптимизации является подбор наиболее экономически эффективных параметров конструкции антенной опоры башенного типа. Этот алгоритм также может быть применен для поиска оптимальной конструкции башенных кранов и различных вантовых сооружений. С растущей в геометрической прогрессии зоной покрытия сигналом операторов сотовой связи требуется всё больше и больше точек для размещения антенного оборудования. Не всегда на такой территории есть дымовые трубы или подобные высокие объекты, подходящие для его размещения, поэтому часто приходится возводить новые конструкции, которые бы отвечали всем нормативным требованиям, но при этом их производство должно быть экономически обоснованно и эффективно, а это подчас два взаимоисключающих фактора. Моделью является пространственная ферменная конструкция высотой 20 м, состоящая из десяти одинаковых секций. Секция имеет в плане квадратное сечение. Все элементы конструкции — равнополочные уголки. Направление раскосов и диагональных распорок по высоте чередуется для придания конструкции дополнительной жесткости (рис. 1). В качестве материала конструкции была принята сталь марки С245 (одна из самых часто применяемых при изготовлении проката).
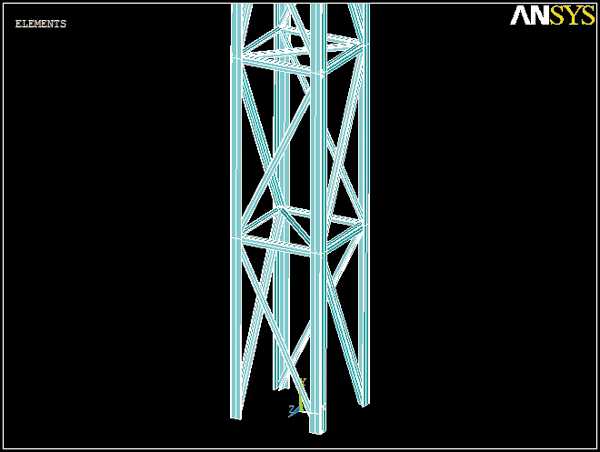
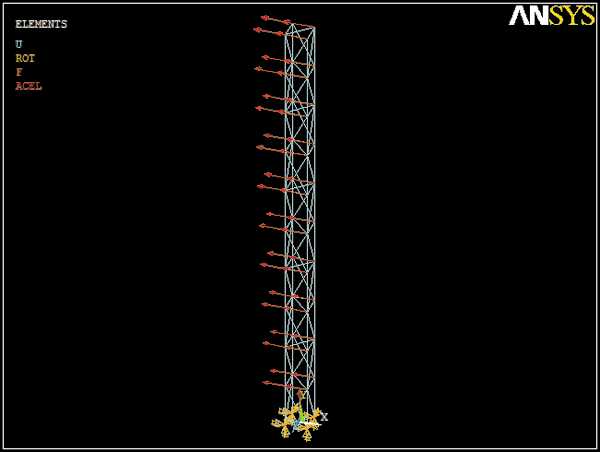
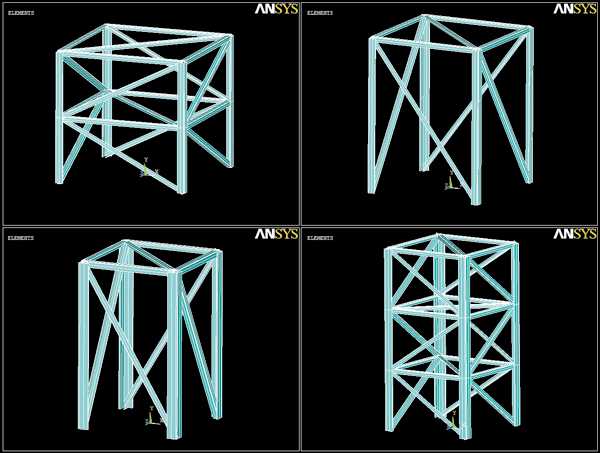
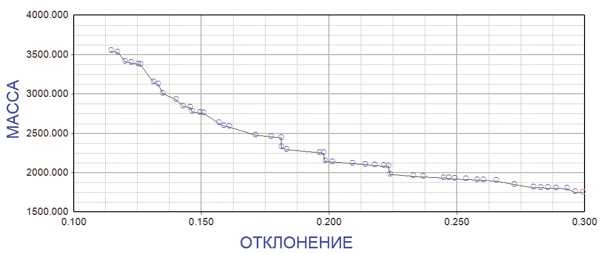
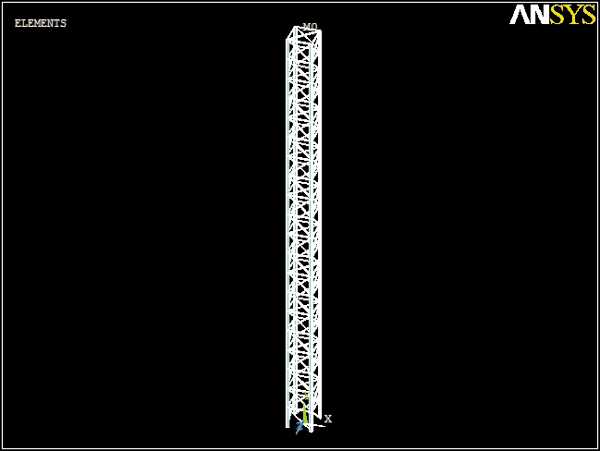
fem-constructions.blogspot.com
РЕАЛИЗАЦИЯ МЕТОДИКИ РЕШЕНИЯ ЗАДАЧИ ОПТИМИЗАЦИИ КОНСТРУКЦИИ ТЕПЛООБМЕННОГО АППАРАТА НА ПЛАТФОРМЕ ANSYS WORKBENCHКретинин А.В., Куликова Е.Е., Булыгин К.Д. Воронежский государственный технический университет» [email protected], [email protected]Для решения задачи оптимизации конструкции теплообменного аппарата средствами пакета конечно-элементного анализа ANSYS создана параметризованная геометрическая модель проточной части теплообменника в ANSYS Design Modeler. Решение уравнений гидродинамики осуществляется в модуле ANSYS CFX. Нелинейная оптимизация проводится в модуле DesignXplorer.Ключевые слова. ANSYS, оптимизация, компьютерная динамика жидкости Для решения задачи оптимизации конструкции теплообменного аппарата средствами пакета конечно-элементного анализа ANSYS необходимо создать параметризованную геометрическую модель проточной части теплообменника в сочетании с автоматическим генератором расчетной сетки, сформировать расчетную модель CFD (компьютерной динамики жидкости), создать параметрически замкнутый расчетный блок и подключить к нему модуль нелинейной оптимизации. Геометрическая модель коллекторного устройства имеет вид, представленный на рис. 1. Для повышения тепловой эффективности теплообменного аппарата необходимо обеспечение равномерного распределения теплоносителя по трубкам теплообменника. Таким образом, стоит задача подбора диаметров трубок теплообменника так, чтобы расходы рабочего тела через них были одинаковы. Для параметрических исследований и оптимизации формируется расчетный блок на платформе Ansys Workbench (рис. 2). Рис. 1. Геометрическая модель теплообменника Рис. 2. Параметрически замкнутый расчетный блокВажным этапом создания расчетного блока является подключение к твердотельной модели проточной части автоматического генератора расчетной сетки. Для этого используется модуль ANSYS Meshing. Ключевым моментом является назначение параметров автоматического построения сетки. В целом ряде работ [1-5] отмечается, что при различных вариантах построения сетки для одних и тех же граничных условий могут получиться различные результаты. Исследование влияния сетки на расчет приводится ниже. Формирование расчетной модели для гидродинамического моделирования осуществляется в соответствии с возможностями модуля ANSYS CFX. Ключевые моменты сформированной расчетной модели представлены ниже. 1. Система уравнений Система уравнений для гидродинамического расчета включает следующие уравнения: уравнение неразрывности; три уравнения количества движения Навье-Стокса, осредненные по Рейнольдсу [6], в проекциях на оси декартовых координат; два уравнения дифференциальной двухпараметрической модели турбулентности k-ε для энергии турбулентных пульсаций и скорости диссипации энергии турбулентности [7]. 2. Граничные условия В качестве рабочего тела используется вода при температуре 25°С. На входе в расчетную область задается массовый расход. На выходе из теплообменника тип граничных условий - Outlet со значением Relative Pressure равным 101300 Па. 3. Параметры решателя Для одного расчета устанавливается максимальное количество итераций равное 400, критерий сходимости - RMS-ошибка принимается равной 10-4. 4. Результаты решения Основными результатами расчета являются значения расходов через трубки теплообменного аппарата. Кроме того, по этим результатам в модуле СFX - CFD Post были сформированы синтетические критерии, которые также автоматически рассчитывались с использованием редактора выражений Expressions: критерий неравномерности распределения компонента по трубкам . Данные критерии выводились в качестве выходных параметров ANSYS Workbench и таким образом формировался параметрически замкнутый расчетный блок. Для проведения оптимизации использовался инструмент Response Surface Optimization, предусматривающий оптимизацию по поверхности отклика. В рамках верификации модели проведена серия расчетов по определению параметров автоматического построения расчетной сетки. На рис. 3 представлены результаты расчета расходов в трубках теплообменника, полученные на последовательно измельченных сетках. Рис. 3. Зависимости расходов в трубках от размера сеткиПо результатам расчетов можно сделать вывод, что не удалось найти параметры автоматического построения сетки, при которых дальнейшее ее измельчение не влияет на результаты расчета. Более того, не удалось достичь сходимости решения по всем уравнениям к значению RMS=0.0001. При попытке достичь этого значения, решая задачу во Fluent, также был получен отрицательный результат. Поэтому в дальнейших оптимизационных расчетах было принято значение RMS=0.0005. Задачу оптимизации можно охарактеризовать как задачу нелинейной условной оптимизации, которая заключается в отыскании такого вектора , , при котором , где ; ; - ограничения на диапазон изменения вектора варьируемых переменных; . Метод построения поверхности отклика базируется на полном квадратичном полиноме, план эксперимента - композиционный центрально-ортогональный. В качестве метода оптимизации по поверхности отклика использован метод последовательного квадратичного программирования Шитковского NLPQL. На рисунке 4 показан оптимизированный вариант конструкции теплообменника. Рис. 4. Результаты оптимизацииВ данной работе для оптимизации конструкции теплообменника применена методика, которую можно считать типовой для решения задач оптимизации с использованием моделей компьютерной динамики жидкости. Методика включает следующие основные этапы: создание параметризованной геометрической модели, построение сеточной модели на основе автоматического генератора расчетной сетки, формирование расчетной CFD модели (выбор уравнений, выбор модели турбулентности, постановка граничных условий), создание параметризованного расчетного блока с выводом в качестве параметров критериев оптимизации, задание области оптимизационного поиска, построение поверхности отклика, нелинейная оптимизация по поверхности отклика. Литература
IMPLEMENTING DECISION PROCEDURE OF OPTIMIZATION PROBLEM FOR HEAT PIPES USING ANSYS WORKBENCH Voronezh State Technical University Kretinin A.V., Kulikova E.E., Bulygin K.D.Abstract. To solve the problem of the heat exchanger design optimization by the finite element analysis using ANSYS software it is necessary to create a parameterized geometric model of the heat exchanger liquid end. This paper shows a technique that can be considered as standard model for solving optimization problems with the use of computer fluid dynamics models. Key words: ANSYS, optimization, computer fluid dynamics |
l.120-bal.ru